Ransburg, Fluid panels, Rcs-2 user manual - introduction – Ransburg RCS 2 Ratio Control System User Manual
Page 12
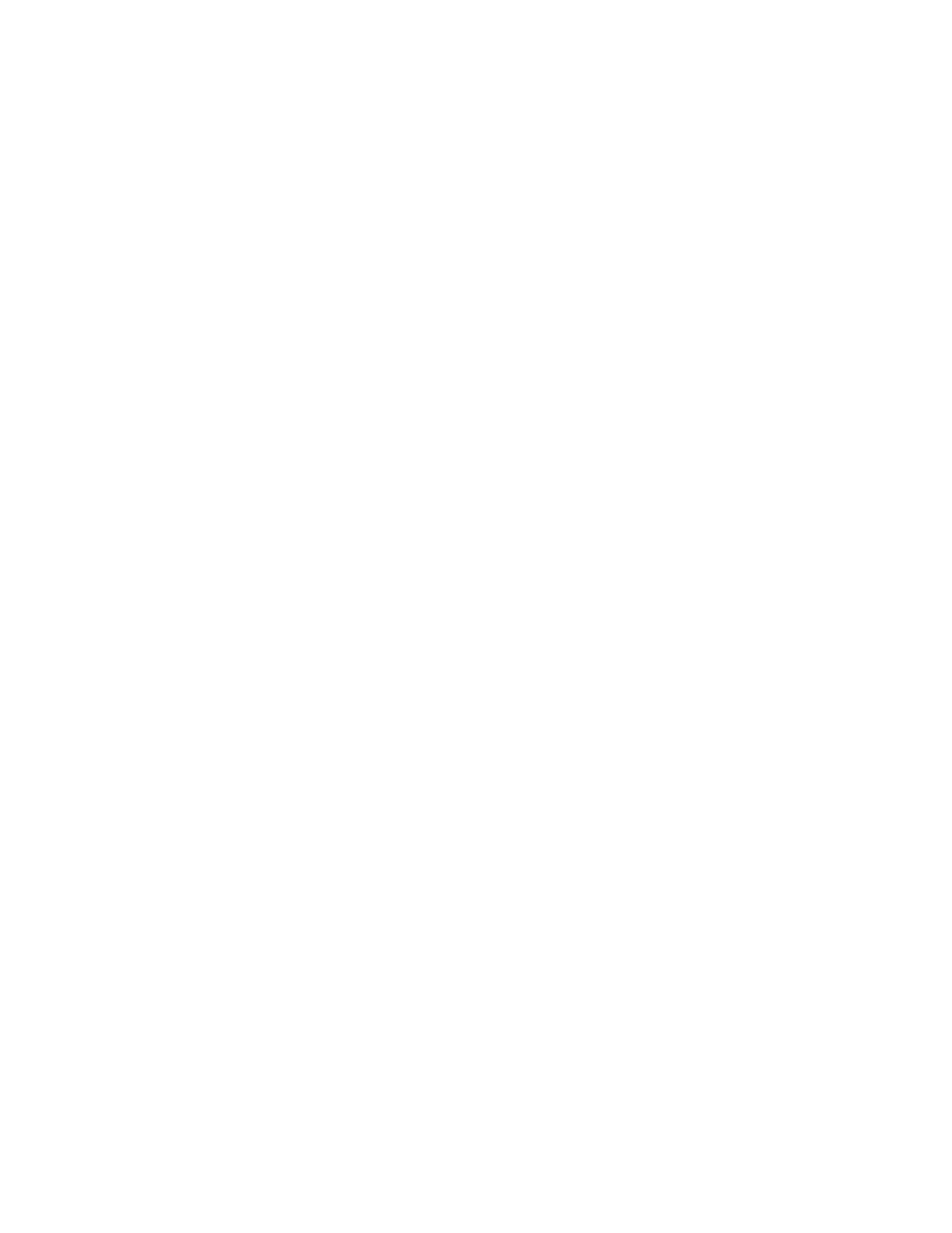
typically used in the catalyst line of the fluid panel.
An additional module converts the flow signal to
a 4 to 20 mA signal that is proportional to the flow
rate of the catalyst. That signal is then fed back
to the channel card so it can be used to generate
faults when catalyst flow falls below a preset point
or if air is detected in the supply line.
The
24 VDC power supply powers the E to P
transducers, the pressure sensors, catalyst flow
sensor modules, and the optional Remote Oper-
ators's Panel.
If the optional color change sequencer is installed,
this power supply will also have a +5 VDC output
to power the color change sequencer.
The optional
Color Change Sequencer is a small
P.L.C. like processor that controls the flush, load,
and color change sequences for each gun and
job number. Each time a job number is loaded
into a gun, the flush and load sequences are
downloaded to this controller. (A color change
sequence is simply a flush sequence followed by
a load sequence.)
Fluid Panels
The Fluid Panels contain all of the "wetted" com-
ponents for the RCS-2 as well as the drive motors.
These include:
• Gear Pumps
• Pump Manifolds
• Servo Motors
• Pressure Sensors
• Catalyst Flow Sensor (optional)
• Mix-Block
• Spiral Mix Tube
• Color Valve Stack (optional)
• Solvent Manifold
• Pump Bypass Valve
The
gear pumps are available in various sizes for
various materials and flow rates. Users should
consult Ransburg technical support group to
determine which pumps are required for their
specific application. (Refer to "Appendix B" for a
list of currently available pump sizes.)
The
pump manifolds house the magnetic cou-
plings which tie the servo motors to the gear pumps.
The
servo motors actually house both an AC drive
servo motor and a feedback resolver in the same
physical housing. They get their drive signals
from the motor drive amplifiers and the resolvers
feed their rotational information back to the motor
drive amplifiers. (Explosion proof servo motors
are available as an option.)
The
pressure sensors convert the fluid pressure
from the fluid inlet and outlet of the pumps to a
4 to 20 mA signal which is then fed through the
zener barriers and back to the channel boards (in
the control rack). Standard units have a pressure
range of 0 psi to 200 psi.
The
catalyst flow sensor is a thermal shedding
type flow sensor that is immersed in the catalyst
flow stream. It detects flow by heating the sensor
and then sensing how much of the heat is being
removed from the sensor by the flow of catalyst.
(More flow = more heat removed from the sensor
head.) An optional explosion-proof version of this
sensor is available for use in hazardous areas.
The
Mix-Block is a three-port manifold that brings
the fluid from the outlet of the resin pump together
with the outlet of the catalyst pump. The block
houses a check valve in the catalyst stream to
prevent resin from backing up into the catalyst
flow stream. Attached to the bottom of the Mix-
Block is a solvent flush valve for quick flushing of
only the mixed material from the Mix-Block out to
the applicator.
Attached to the outlet of the Mix-Block is the
spiral
mix tube. This is simply a piece of tubing with a
helical-shaped element inside the tube. This ele-
ment causes the two materials (resin and catalyst)
to be "folded" together numerous times as the
materials pass through it, thus causing it to mix.
The optional CCV style
color valve stack allows
users to do color changes on the resin side of up
to 10 colors.
RCS-2 User Manual - Introduction
9
LN-9407-00.2
Ransburg