Ransburg, Appendix l: pushout, Rcs-2 user manual - appendix – Ransburg RCS 2 Ratio Control System User Manual
Page 75
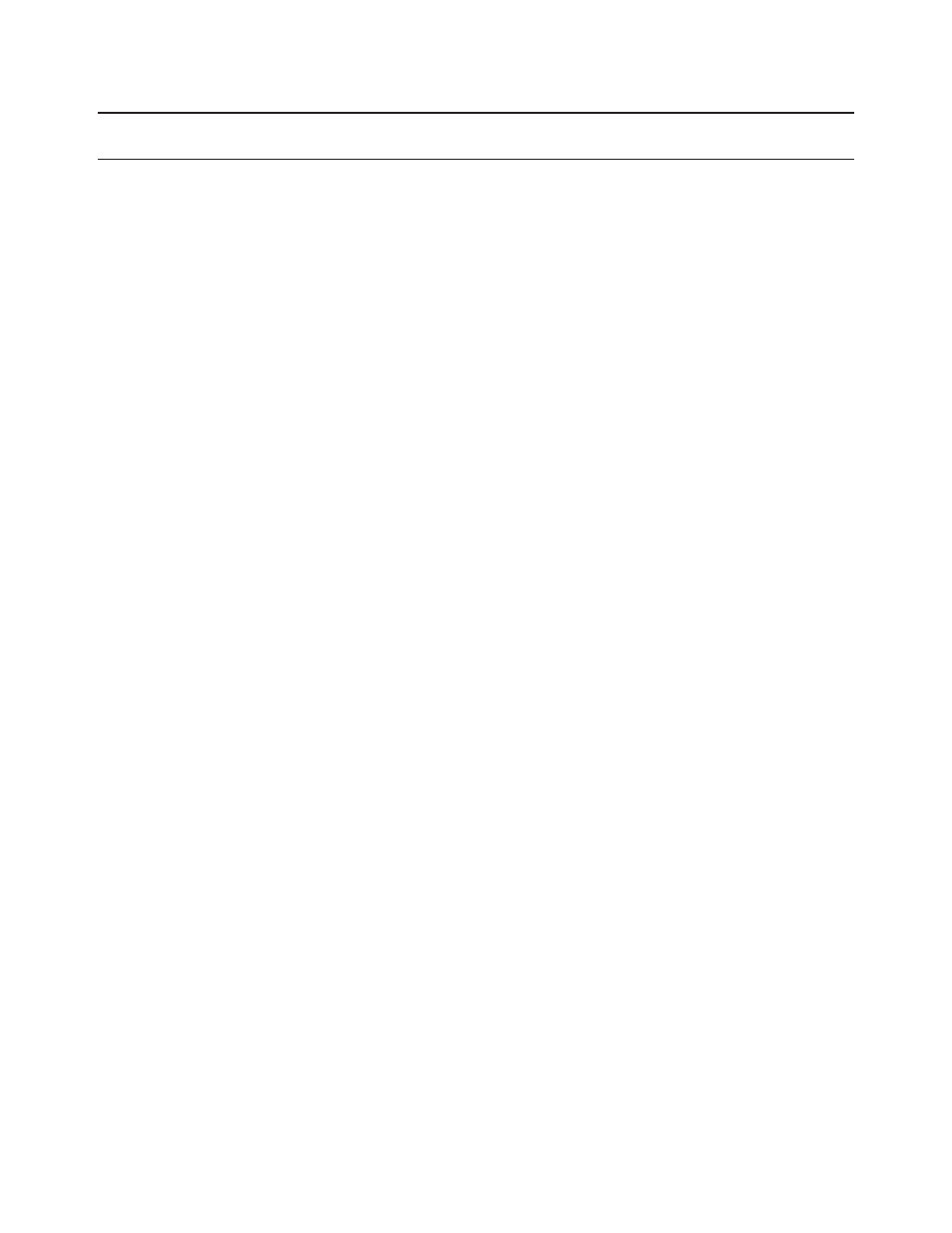
A new feature has been added to the RCS-2
software called “Pushout”. This feature allows a
customer that uses dual purge applicators to use
two resin pumps that share a common catalyst
pump and pushout the resin with solvent on one
side of the dual purge applicator while loading the
other side of the applicator with the next material
to be sprayed.
The system employs a small relay panel that
switches the command signals for the catalyst
motor drive between two slave channels in the
RCS-2 control console. (Contact Ransburg for
design details for this relay panel.)
The process steps to implement this feature are
outlined below:
1. Assume the applicator is running 2 component
material through one side of a dual purge applicator
and that material is being controlled by channels
1 and 2 of the RCS-2 where channel 1 is the resin
and channel 2 is the catalyst.
2. As the last part, buck, rack, etc. approaches
the robot for the presently running color, either
the PLC or the robot sends a “Pushout” signal to
the RCS-2. At that instant, the RCS-2 will imme-
diately turn off the catalyst pump and speed up
the resin pump to maintain the target flow rate
that was being sprayed prior to the initiation of the
pushout signal. (Note that this pushout signal is
a maintained signal.)
3. Simultaneous with the pushout signal being
turned on, the PLC or robot will turn off the color
valve and turn on the solvent valve on the resin
color valve stack connected to the first resin pump.
Depending on how the catalyst is controlled, it
may be necessary to also switch off the catalyst
valve or at least change its direction. Note that
not all pumps are capable of accurately dispensing
solvent (because of its low viscosity). It is up to
the user to ascertain if the pump they are using
is accurate enough when metering solvent to
maintain a proper film builds on their parts.
APPENDIX L: PUSHOUT
4. The RCS-2 will continue to deliver fluid out of the
first dual purge side until the volume programmed
in for mixed volume has been sprayed and then
that gun (in this case Gun #1) will automatically
be halted (taken out of run mode). This state will
be recognized by the PLC or robot when the Run
output from the RCS-2 turns off.
5. The PLC or robot must then energize a series of
relays in the relay panel which switches the signals
connected between the catalyst motor drive and
the channel card from channel 2 to channel 4.
6. While the first dual purge side is being pushed
out, gun #2 (configured as channels 3 and 4) can
begin to load dual component material, using the
resin pump connected to channel 3 and the cat-
alyst pump that is now controlled by channel 4.
(Single component material can also be loaded
by using the proper 1k ratio programmed in the
job parameters.)
7. As the applicator continues to spray dual com-
ponent material out of the second side, the first
side can be flushed using A Fill, solvent/air chops,
pump bypass signals, etc. Note: The pushout
signal must be asserted with the A Fill signal or
the software will attempt to enable the channel B
motor drive. (This is done to prevent backflow of
resin in the catalyst line on 2k configured guns.)
8. When the last part approaches the robot for the
presently running color occurs again, the proce-
dure repeats for the second side of the dual purge
applicator (see step 2, above) with the exception of
in step 5, the relays are de-energized to reconnect
the catalyst motor drive to channel 2.
RCS-2 User Manual - Appendix
72
LN-9407-00.2
Ransburg