1 accuracy effects of diode non-ideality factor, 2 pcb layout for minimizing noise, 10 fan control – Rainbow Electronics LM93 User Manual
Page 28: 1 automatic fan control algorithm, 0 using the lm93
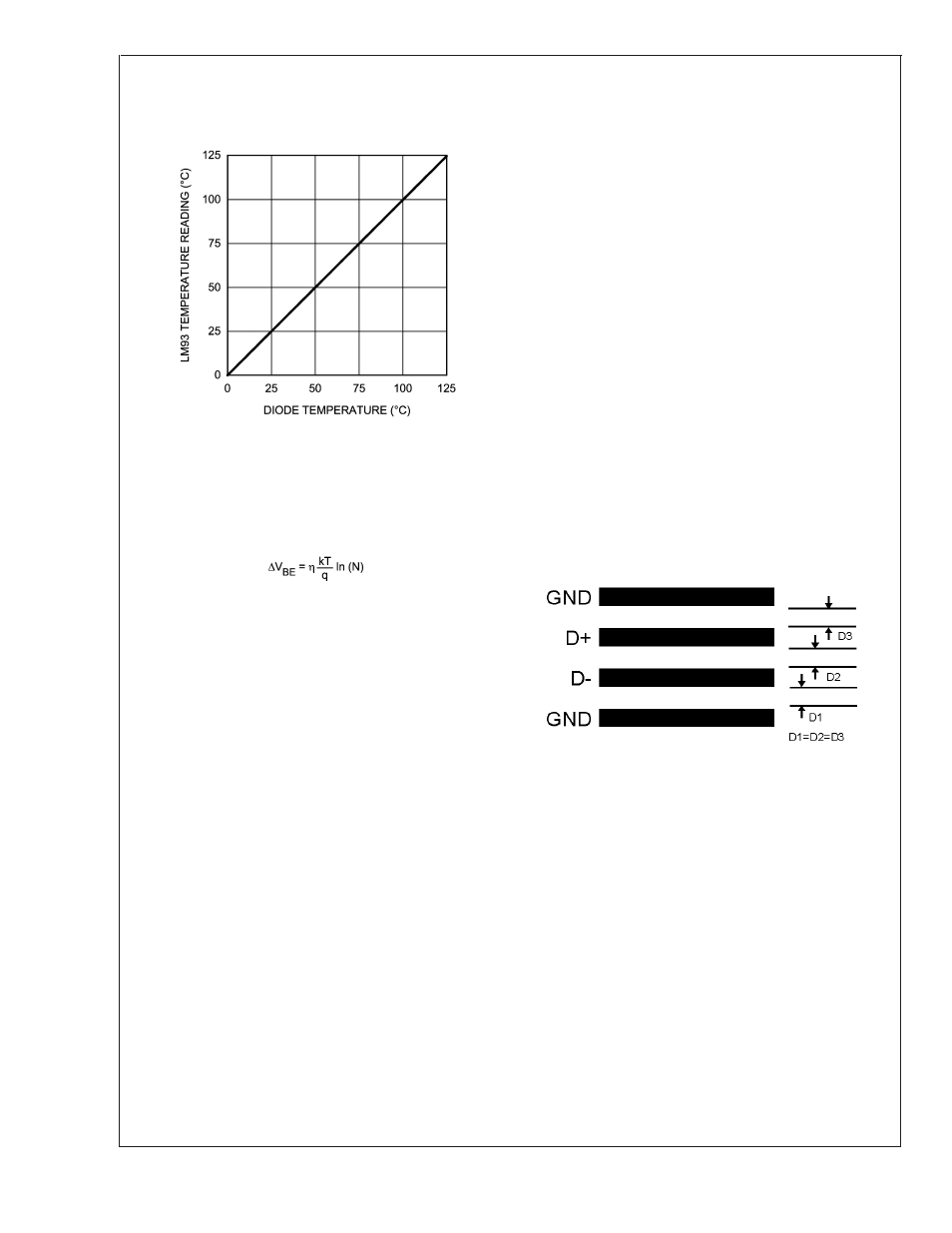
15.0 Using The LM93
(Continued)
Thermal Diode Temperature vs. LM93 Temperature
Reading
20068215
15.9.1 Accuracy Effects of Diode Non-Ideality Factor
The technique used in today’s remote temperature sensors
is to measure the change in V
BE
at two different operating
points of a diode. For a bias current ratio of N:1, this differ-
ence is given as:
where:
-
η is the non-ideality factor of the process the diode is
manufactured on,
- q is the electron charge,
- k is the Boltzmann’s constant,
- N is the current ratio,
- T is the absolute temperature in ˚K.
The temperature sensor then measures
∆V
BE
and converts
to digital data. In this equation, k and q are well defined
universal constants, and N is a parameter controlled by the
temperature sensor. The only other parameter is
η, which
depends on the diode that is used for measurement. Since
∆V
BE
is proportional to both
η and T, the variations in η
cannot be distinguished from variations in temperature.
Since the non-ideality factor is not controlled by the tempera-
ture sensor, it directly adds to the inaccuracy of the sensor.
For example, assume a
±
1% variation in
η from part to part
(Xeon processors targeted for the LM93 do not have pub-
lished thermal diode specifications at the time of this printing,
therefore this is probably a very conservative estimate).
Assume a temperature sensor has an accuracy specification
of
±
3˚C at room temperature of 25˚C and the process used
to manufacture the diode has a non-ideality variation of
±
1%. The resulting accuracy of the temperature sensor at
room temperature is:
TACC =
±
3˚C + (
±
1% of 298˚K) =
±
6˚C
The additional inaccuracy in the temperature measurement
caused by
η, can be eliminated if each temperature sensor is
calibrated with the remote diode that it is paired with. The
LM93 can be paired with an MMBT3904 when not being
used to monitor the thermal diode within an Intel Processor.
15.9.2 PCB Layout for Minimizing Noise
In the following guidelines, D+ and D− refer to the RE-
MOTE1+, REMOTE1−, REMOTE2+, REMOTE2− pins.
In a noisy environment, such as a power supply, layout
considerations are very critical. Noise induced on traces
running between the remote temperature diode sensor and
the LM93 can cause temperature conversion errors.
The following guidelines should be followed:
1.
Place a 0.1 µF and 100 pF LM93 power bypass capaci-
tors as close as possible to the V
DD
pin, with the 100pF
capacitor being the closest. Place 10 µF capacitor in the
near vicinity of the LM93 power pin.
2.
Place 100 pF capacitor as close as possible to the LM93
thermal diode Remote+ and Remote− pins. Make sure
the traces to the 100 pF capacitor are matched and as
short as possible. This capacitor is required to minimize
high frequency noise error.
3.
Ideally, the LM93 should be placed within 10 cm of the
thermal diode pins with the traces being as straight,
short and identical as possible. Trace resistance of 1
Ω
can cause as much as 1˚C of error.
4.
Diode traces should be surrounded by a GND guard ring
to either side, above and below, if possible. This GND
guard should not be between the Remote+ and
Remote− lines. In the event that noise does couple to
the diode lines, it would be ideal if it is coupled to both
identically, i.e. common mode. That is, equally to the
Remote+ (D+) and Remote−(D-) lines. (See figure be-
low):
Recommended Diode Trace Layout
20068220
5.
Avoid routing diode traces in close proximity to any
power supply switching or filtering inductors.
6.
Avoid running diode traces close to or parallel to high
speed digital and bus lines. Diode traces should be kept
at least 2 cm apart from the high speed digital traces.
7.
If it is necessary to cross high speed digital traces, the
diode traces and the high speed digital traces should
cross at a 90 degree angle.
8.
Leakage current between Remote+ and GND should be
kept to a minimum. 1 nA of leakage can cause as much
as 1˚C of error in the diode temperature reading. Keep-
ing the printed circuit board as clean as possible mini-
mizes leakage current.
15.10 FAN CONTROL
15.10.1 Automatic Fan Control Algorithm
The LM93 fan speed control method is optimized for fan
power efficiency, fan reliability and minimum cost. The
PWMx outputs can be filtered using an external switching
regulator type output stage that provides 5V to 12V DC for
fan power. A high PWM frequency is required to minimize the
LM93
www.national.com
28