12 fan speed measurement, 13 smart fan speed measurement, 0 inputs/outputs – Rainbow Electronics LM93 User Manual
Page 17: 1 alert output, 2 reset input/output, 3 pwm1 and pwm2 outputs, 4 scsi_termx inputs, 0 functional description
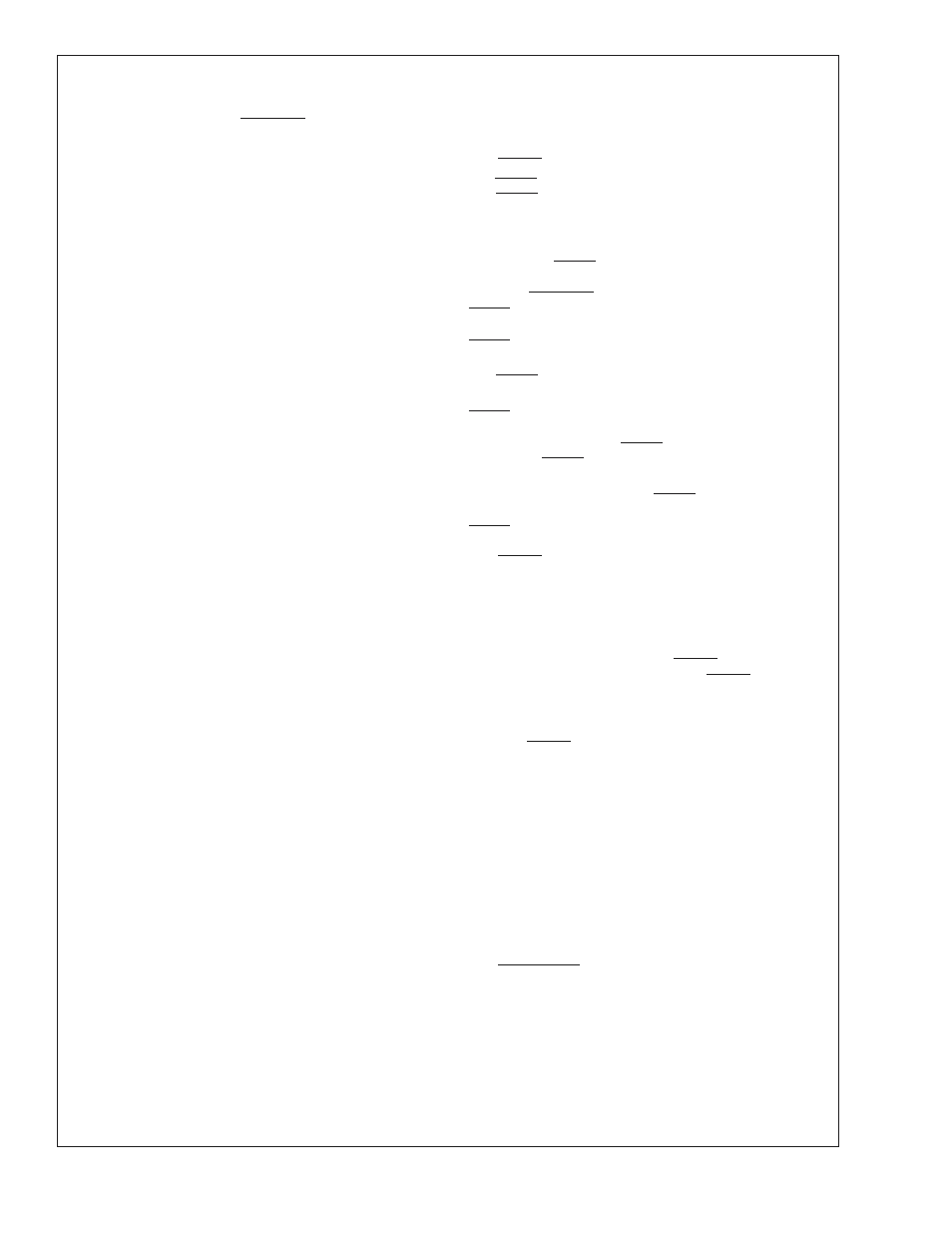
12.0 Functional Description
(Continued)
is configured to short the PROCHOT signals together, it
always asserts them together whenever this function is en-
abled.
12.12 FAN SPEED MEASUREMENT
The fan tach circuitry measures the period of the fan pulses
by enabling a counter for two periods of the fan tach signal.
The accumulated count is proportional to the fan tach period
and inversely proportional to the fan speed. All four fan tach
signals are measured within 1 second.
Fans in general do not over-speed if run from the correct
voltage, so the failure condition of interest is under speed
due to electrical or mechanical failure. For this reason only
low-speed limits are programmed into the limit registers for
the fans. It should be noted that, since fan period rather than
speed is being measured, a fan tach error event occurs
when the measurement exceeds the limit value.
12.13 SMART FAN SPEED MEASUREMENT
If a fan is driven using a low-side drive PWM, the tachometer
output of the fan is corrupted. The LM93 includes smart
tachometer circuitry that allows an accurate tachometer
reading to be achieved despite the signal corruption. In
smart tach mode all four signals are measured within 4
seconds.
A smart tach capture cycle works according to the following
steps:
1.
Both PWM outputs are synchronized such that they
activate simultaneously.
2.
Both PWM output active times are extended for up to 50
ms.
3.
The number of tach signal periods during the 50 ms
interval are tracked:
a) If less than 1 period is sensed during the 50 ms exten-
sion the result returned is 3FFh.
b) After one period occurs the count for that period is
memorized.
c) If during the 50 ms interval 2 periods do not occur, the
tach value reported is the 1 period count multiplied by
2.
d) If 2 periods do occur, the 2 period count is loaded into
the value register and the 50 ms PWM extension is
terminated.
The lowest two bits in each of the Fan Tach value registers
are reserved. The smart tach feature takes advantage of
these bits. In normal tach mode, these bits return 00. In
smart tach mode the two bits determine the accuracy level of
the reading. 11 is most accurate (2 periods used) and 10 is
the least accurate (1 period used). If less than 1 period
occurred during the measurement cycle, the lower two bits
are set to 10.
In smart fan tach mode, the TACH_EDGE field is honored in
the LM93 Status/Control register. If only one edge type is
active, the measurement always uses that edge type (rising
or falling). If both are active, the measurement uses which-
ever edge type occurs first.
Typically the minimum RPM captured by smart fan tach
mode is 900 RPM for a fan that produces two pulses per
revolution at about 50% duty cycle.
13.0 Inputs/Outputs
Besides all the pins associated with sensor inputs the LM93
has several pins that are assigned for other specific func-
tions.
13.1 ALERT OUTPUT
The ALERT output is an active-low open drain output signal.
The ALERT output is used to signal a micro-controller that
one or more sensors have crossed their corresponding limit
thresholds. This is generally not a fatal event unless the
micro-controller decides it to be.
If enabled, the ALERT output is asserted whenever any bit in
any BMC Error Status register is set (with the exception of
the fixed PROCHOT threshold bits). By definition, when
ALERT is enabled, it always matches the inverse of the
BMC_ERR bit in the LM93 Status/Control register. When the
ALERT output is disabled, an alert event can still be deter-
mined by reading the state of the BMC_ERR bit.
The ALERT functions like an interrupt. The LM93 does not
support the SMBus ARA (Alert Response Address) protocol.
ALERT is only de-asserted when there are no error status
bits set in any BMC Error Status registers. Alternatively,
software can disable the ALERT output to cause it to de-
assert. The ALERT output re-asserts once enabled if any
BMC Error Status register bits are still set.
Further information on how the ALERT output behaves can
be found in Section 15.7 MASKING, ERROR STATUS AND
ALERT.
13.2 RESET INPUT/OUTPUT
This pin acts as an active low reset output when power is
applied to the LM93. It is asserted when the LM93 first sees
a voltage that exceeds the internal POR level on its +3.3V
S/B V
DD
input. The internal registers of the LM93 are reset to
their defaults when power is applied.
After this reset has completed, the RESET pin becomes an
input. When an external device asserts RESET, the LM93
clears the LOCK bit in the LM93 Configuration register. This
feature allows critical registers to be locked and provides a
controlled mechanism to unlock them.
Asserting RESET externally causes the Sleep State Control
register to be automatically set to S4/5. This causes several
error events to be masked according to the S4/5 masking
definitions. Refer to the register descriptions for more infor-
mation.
13.3 PWM1 AND PWM2 OUTPUTS
The PWM outputs are used to control the speed of fans. The
output signal duty cycle can automatically be controlled by
the temperature of one or more temperature zones. It is also
influenced by various other inputs and registers. See Section
15.10 FAN CONTROL for further information on the behavior
of the PWM outputs.
13.4 SCSI_TERMx INPUTS
These inputs can be used to monitor the status of the
electronic fuse on each of the SCSI channels. In prior imple-
mentations the reference voltage out to the terminators was
measured. When LVDS SCSI was introduced this reference
voltage could take on multiple voltage levels depending on
the mode of the SCSI bus. Also when the SCSI terminators
were disabled, the V
REF
voltage could not be guaranteed.
Monitoring individual terminators was also pin intensive. All
LM93
www.national.com
17