Functional overview, General concepts, Module power up and configuration – ProSoft Technology MVI71-DNP User Manual
Page 78: E 78), Functional, Overview
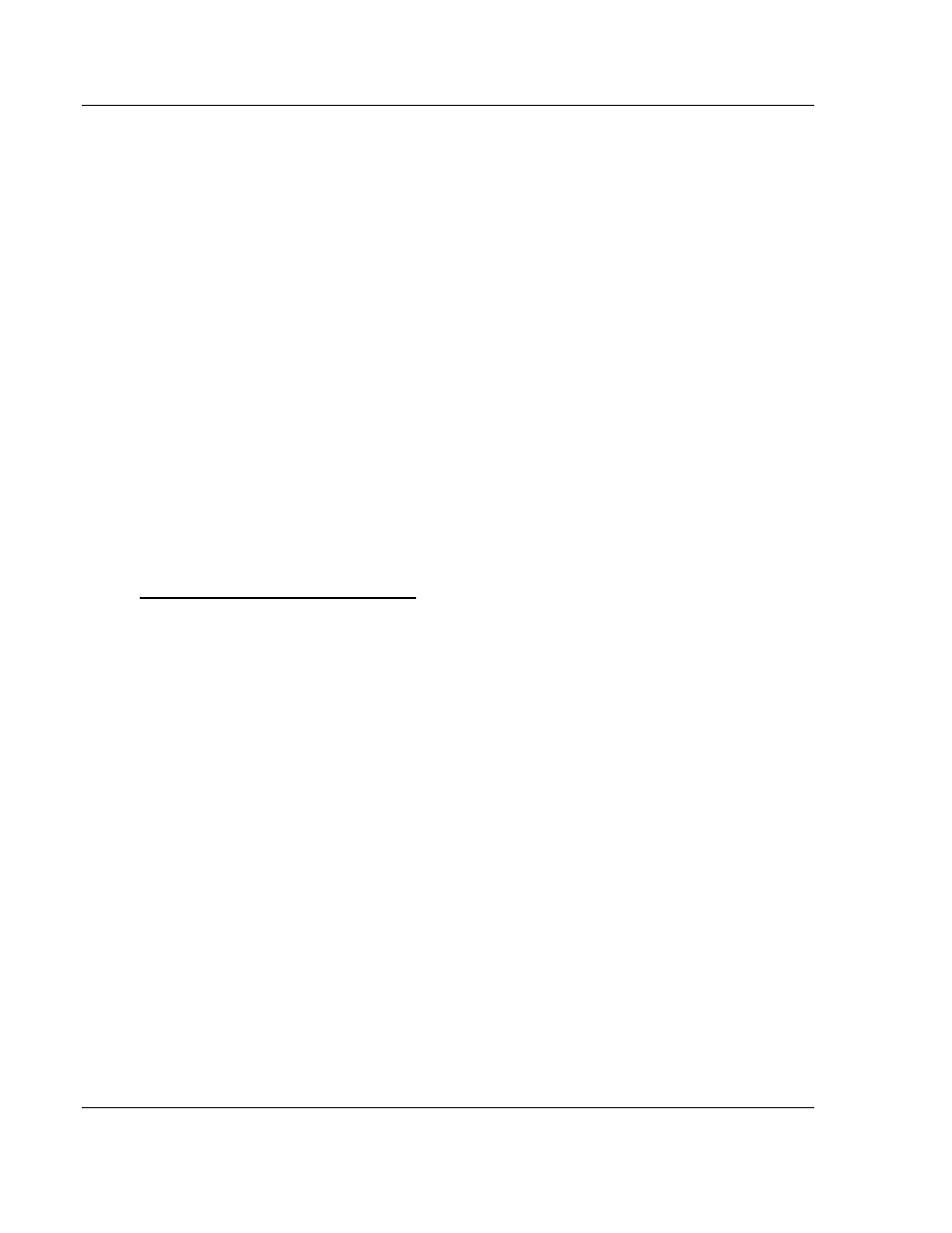
MVI71-DNP ♦ PLC Platform
Reference
DNP 3.0 Master/Slave Communication Module
Page 78 of 172
ProSoft Technology, Inc.
August 23, 2007
5.2 Functional
Overview
This section provides an overview of how the MVI71-DNP module transfers data
using the DNP protocol. You should understand the important concepts in this
chapter before you begin installing and configuring the module.
5.2.1 General
Concepts
The following topics describe several concepts that are important for
understanding the operation of the MVI71-DNP module.
1
On power up the module begins performing the following logical functions:
2
Initialize hardware components
o
Initialize PLC backplane driver
o
Test and Clear all RAM
o
Initialize the serial communication ports
3
Reads configuration from the DNP.CFG file
4
Allocate and initialize Module Register space
5
Enable Slave Driver on selected ports
6
Enable Master Driver on selected port if configured
After the module has received the Module Configuration, the module will begin
communicating with other nodes on the network, depending on the configuration.
Module Power Up and Configuration
Configuration information is stored on the module's Compact Flash. Setup of the
module requires software configuration using the RSLogix 5 program and the
DNP.CFG configuration file on the Compact Flash. The easiest method to
implement the module is to start with the example provided with the module
(MVI71DNP.RSP) and the example configuration file (DNP.CFG). Module
Configuration describes how to use and/or modify the two files.
If the DNP master port is to be used, the module reads the slave configuration
information and builds the slave list during the configuration process. The module
also reads the command list from the .CFG file. Valid commands will be added to
the command list. Binary input, counter and analog input objects will be added to
the point lists for each slave based on the commands processed. In addition, the
RBE (Report By Exception) flags for the binary and analog input points are set in
the RBE flag database.
The module next checks the DNP BO/AO (Binary Output / Analog Output) preset
flag to determine if the DNP binary and analog output data must be read from the
PLC. The option permits the PLC to set these read-only data at startup. There is
no static memory available on the module to remember the last values for these
data types. In order to prevent "shock" to the system at boot time, this option can
be used to set the module's database to the last transferred set of data. Ladder
logic must transfer the data to the module using BTR/BTW instructions for these
data types.