Module data, Status data, Module – ProSoft Technology MVI71-DNP User Manual
Page 23: Data
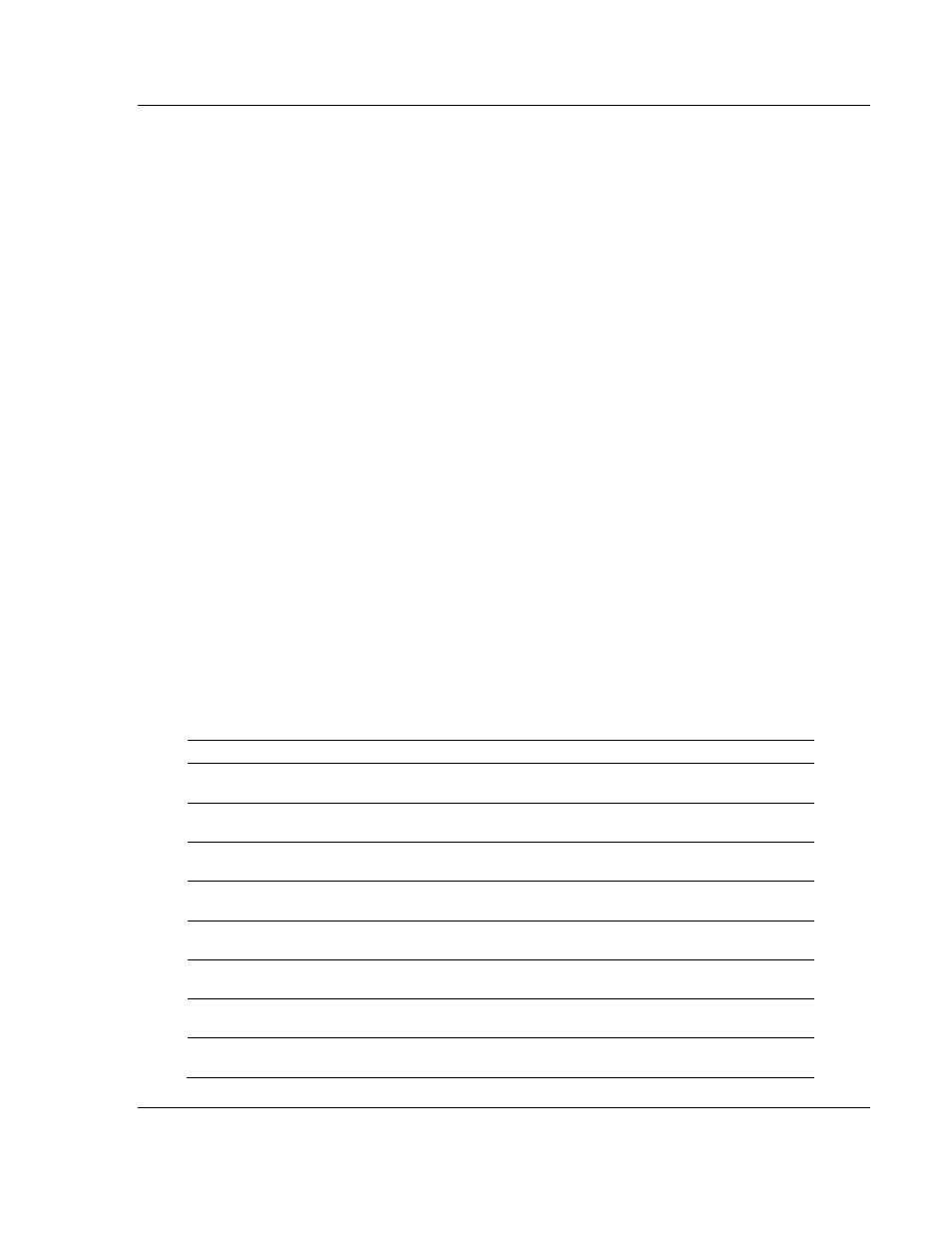
Installing and Configuring the Module
MVI71-DNP ♦ PLC Platform
DNP 3.0 Master/Slave Communication Module
ProSoft Technology, Inc.
Page 23 of 172
August 23, 2007
Special care must be taken when defining the files for the side-connect interface.
Because the module directly interacts with the PLC processor and its memory,
any errors in the configuration may cause the processor to fault and it may even
lose its configuration and program. After defining the files and populating them
with the correct data, download the program to the processor, and place the
processor in run mode. If everything is configured correctly, the module should
start its normal operation.
The module is now and ready to be used with your application. Insert the module
in the rack (with the power turned off) and attach the serial communication cable.
Download the new application to the controller and place the processor in run
mode. Download the new DNP.CFGfile to the module using a terminal emulation
program. If all the configuration parameters are set correctly and the module is
attached to a network, the module's Application LED (APP LED) should remain
off and the backplane activity LED (BP ACT) should blink very rapidly. Refer to
the Diagnostics and Trouble Shooting section if you encounter errors. Attach a
computer or terminal to Port 0 on the module and look at the status of the module
using the Configuration/Debug Menu in the module.
2.1 Module
Data
All data related to the MVI71-DNP module is stored in a user defined data file. It
is the responsibility of the ladder logic programmer to construct all the data files
required by the program and to write the ladder logic required to interface to
these files.
2.1.1 Status
Data
When the side-connect interface is employed in the application, the status data is
automatically transferred from the module to the first file used by the interface.
The data is placed at an offset of 0 in the file and has the following format:
Word
Variable Name
Description
0
Scan Counter
Program scan counter incremented each time the program
loop is executed.
1 to 2
Product Name (ASCII)
These two words contain the product name of the module
in ASCII format.
3 to 4
Revision (ASCII)
These two words contain the product revision level of the
firmware in ASCII format.
5 to 6
Operating System
Revision (ASCII)
These two words contain the module's internal operating
system revision level in ASCII format.
7 to 8
Production Run
Number (ASCII)
These two words contain the production 'batch' number for
the particular chip in the module in ASCII format.
9
Read Block Count
Total number of blocks transferred from the module to the
processor.
10
Write Block Count
Total number of blocks transferred from the processor to
the module.
11
Parse Block Count
Total number of blocks parsed by the module that were
received from the processor.