5 mother board a5, 7 heat sink assembly a7, Mother board a5 -16 – KEPCO MBT Series User Manual
Page 122: Heat sink assembly a7 -16
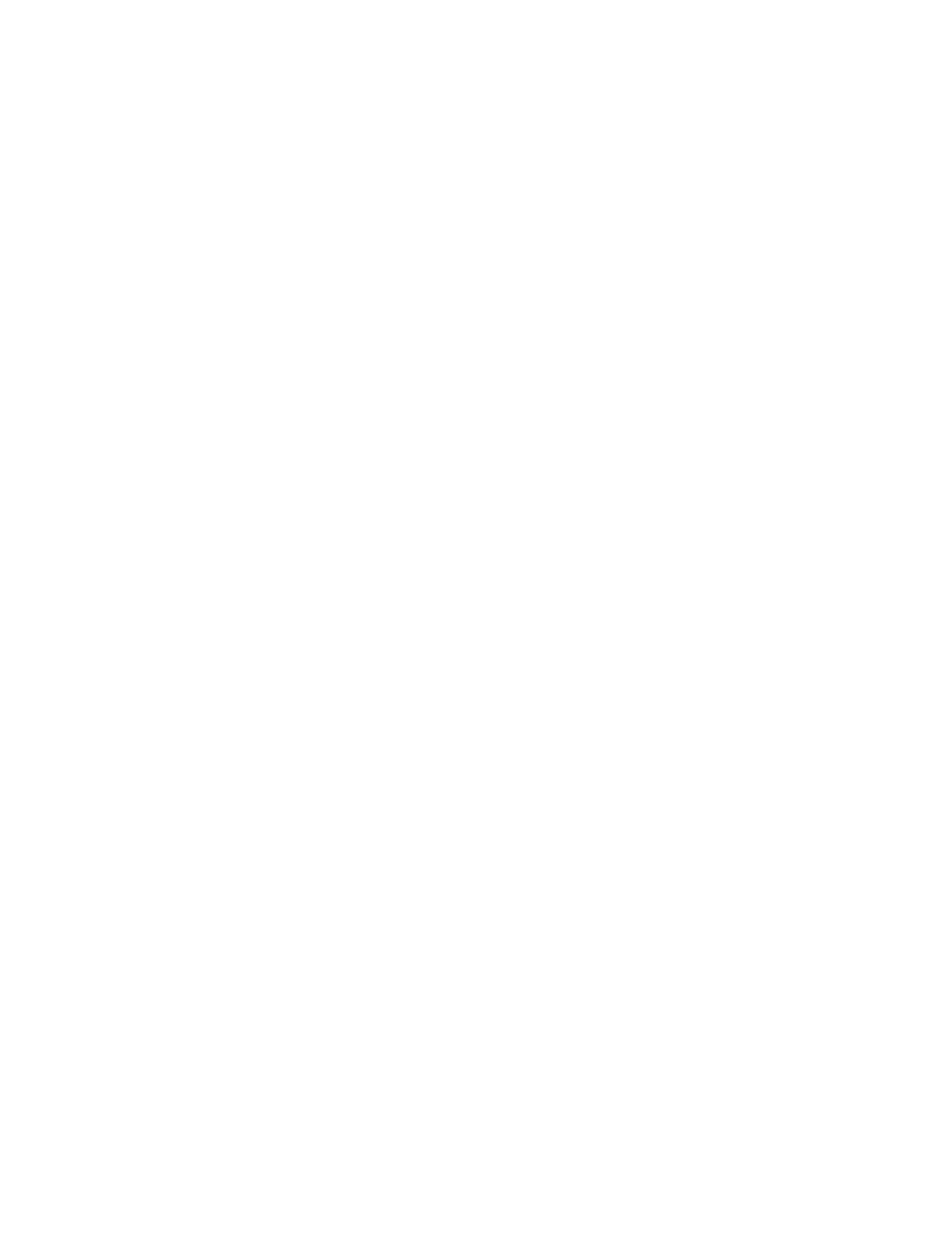
4-16
MBTSVC111609
4.3.5
MOTHER BOARD A5 (See Schematic Diagram, Figure 6-23)
Mother Board A5 provides interconnections between various power supply components and is
identical for all MBT models and options. Boards A1, A2, A3, and A4 plug directly into connec-
tors A5J3, A5J2, A5J1, and A5J4, respectively (see Figure 6-7 for component locations). Con-
nector A5J5 provides connections to/from heat sink assemblies A7, A10 and (for MR and MGR
units) the Relays Assembly; connector J6 provides interconnections for Front Panel Board A8.
4.3.6
A-C INPUT CIRCUIT AND MAIN D-C SUPPLY (CHASSIS A6) (See Main Schematic Dia-
gram, Figure 6-17)
A-C source power is received via the rear panel-mounted 3-pin AC INPUT connector A6J1,
routed to the front panel POWER circuit breaker A6CB1, and applied to distribution terminal
block A6TB1. Circuit breaker A6CB1 functions to protect the MBT Power Supply by opening if
either an overcurrent condition in the primary a-c circuit appears, or if the voltage circuit breaker
coil is activated by the Crowbar and Circuit Breaker Command circuit (see PAR. 4.3.2).
The two primary windings of main line transformer A6T1 are connected either in parallel for
115V a-c nominal line voltage, or in series for 230V a-c nominal line voltage, using rear panel-
mounted AC INPUT SELECTOR switch A6S1. Terminal block A6TB1 also distributes source
power (115V a-c) to the fan, the auxiliary line transformer on Auxiliary Power Supply Board A4
via Relay and Flags Board A2, and, for MG and MGR option units, the separate FMP 5-2K aux-
iliary “G” option power module, A15.
The fan is powered through power resistor A6R2; when the heatsink temperature is high
enough to close thermostat A6S2, but not high enough to close overtemperature thermostat
A6S1, resistor A6R2 is shorted. This effectively allows the fan to operate at two speeds: low
speed for low power dissipation by the heat sink and low ambient temperature, or high speed for
high power dissipation by the heat sink and/or high ambient temperature conditions.
The main d-c voltage is obtained by rectifying the main transformer A6T1 secondary winding
voltage using silicon diodes configured as either a full wave bridge or, for MBT 6-32, a full wave
center-tapped rectifier circuit (A6CR1). This voltage is filtered by the parallel-connected main fil-
ter capacitors A6C1 and A6C2.
4.3.7
HEAT SINK ASSEMBLY A7 (See Main Schematic Diagram, Figure 6-17)
The heat sink assembly or pass element is equivalent to a bipolar NPN transistor working in an
emitter follower configuration having a very high d-c current amplification factor. There are two
different configurations of heat sink assembly A7: one for the six low voltage models and one for
the two high voltage models and some slight differences between models of each configuration.
The low voltage configuration (MBT 6-32M, 15-20M, 25-14M, 36-10M, 55-7M, 75-5M) has 13
NPN transistors cascaded on three levels, with the 11 output transistors in parallel.
The high voltage configuration (MBT 100-3.6M, 150-2.4M) employs two series branches of tran-
sistors that divide the voltage across them. Each branch is cascaded on two levels and has the
final five transistors in parallel.
The pass element is connected in series with the unregulated main d-c supply and the output.
The series equivalent resistance of the pass element, and therefore the voltage across it, is
changed to keep either the output voltage (in Voltage Mode) or output current (in Current Mode)
constant.