A.4 gain setting references – Yaskawa Sigma Mini User Manual
Page 259
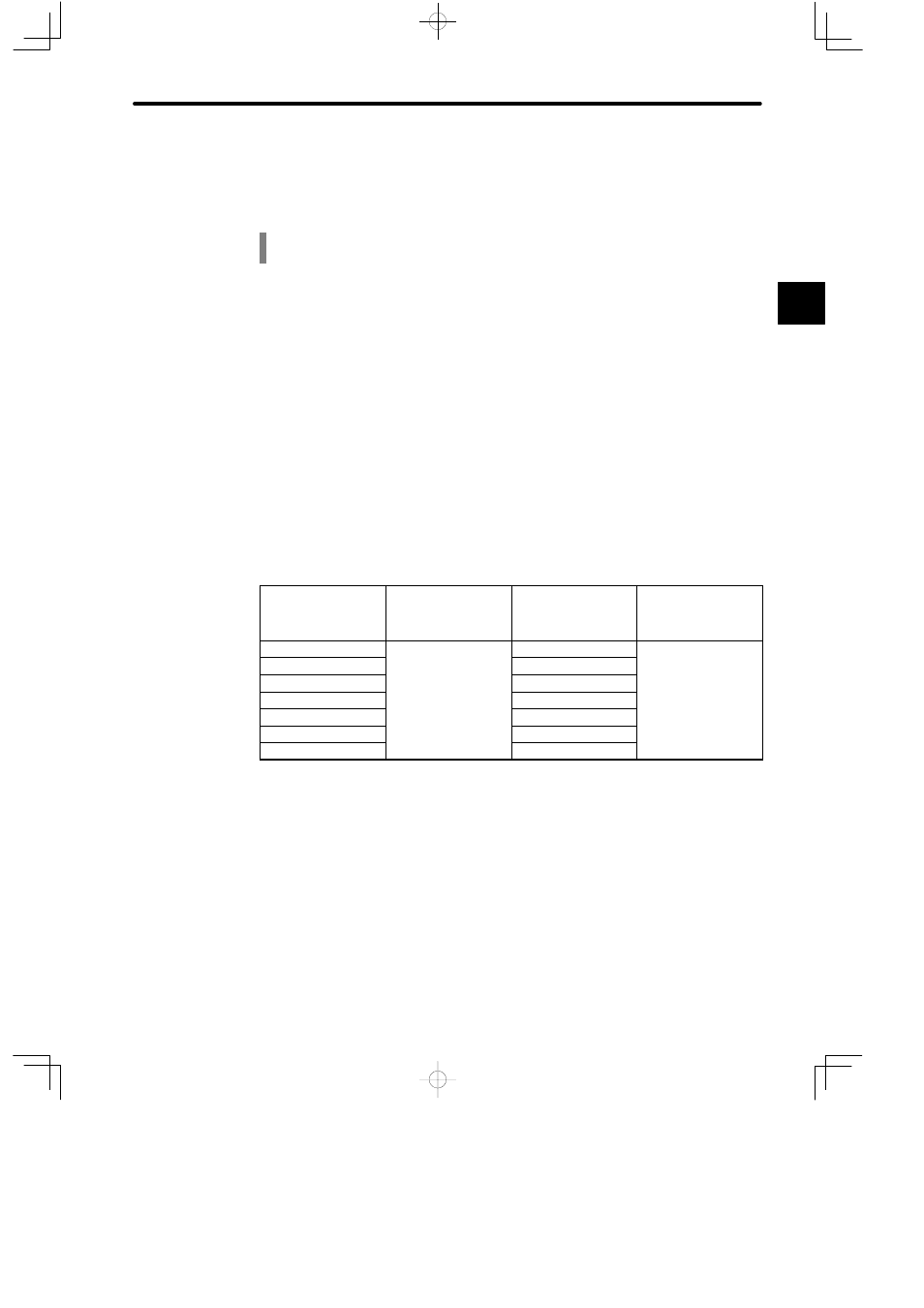
A.4 Gain Setting References
— A-13 —
A.4 Gain Setting References
This section presents tables of load moment of inertia values for reference when
adjusting the gain.
A.4.1 Guidelines for Gain Settings According to Load Inertia Ratio
Adjustment guidelines are given below according to the rigidity of the mechanical system and
load moment of inertia. Use these values as guidelines when adjusting according to the pro-
cedures described above.
These values are given as guidelines only. Oscillations and poor response may occur inside
the specified value ranges. Observe the response (waveform) when optimizing the adjust-
ment.
Higher gains are possible for machines with high rigidity.
Machines with High Rigidity
Ball Screw, Direct Drive Machines
Example: Chip mounter, IC bonder, precision machine tools
Load/Inertia Ratio
(GD
L
2
/GD
M
2
)
Position Loop Gain
(Cn-1A) [1/s]
Speed Loop Gain
(Cn-04) [Hz]
Speed Loop
Integration Time
Constant
(Cn-05) [ms]
1 x
50 to 70
50 to 70
5 to 20
3 x
100 to 140
Slightly increase for
5 x
150 to 200
Slightly increase for
inertia ratio of 20 x, or
greater
10 x
270 to 380
greater.
15 x
400 to 560
20 x
500 to 730
30 x
700 to 1100
Note
For an inertia ratio of 10 x, or greater, slightly reduce the position loop gain and speed loop
gain below the values shown and set the integration time constant to a higher value before
starting the adjustment.
As the inertia ratio increases, set the position loop gain and speed loop gain to the lower limit
of the range of values specified. Conversely, increase the speed loop integration time
constant.
A