Planned certified configurations, Safety manual (aadvance controller) – Rockwell Automation AADvance Controller Safety Manual User Manual
Page 48
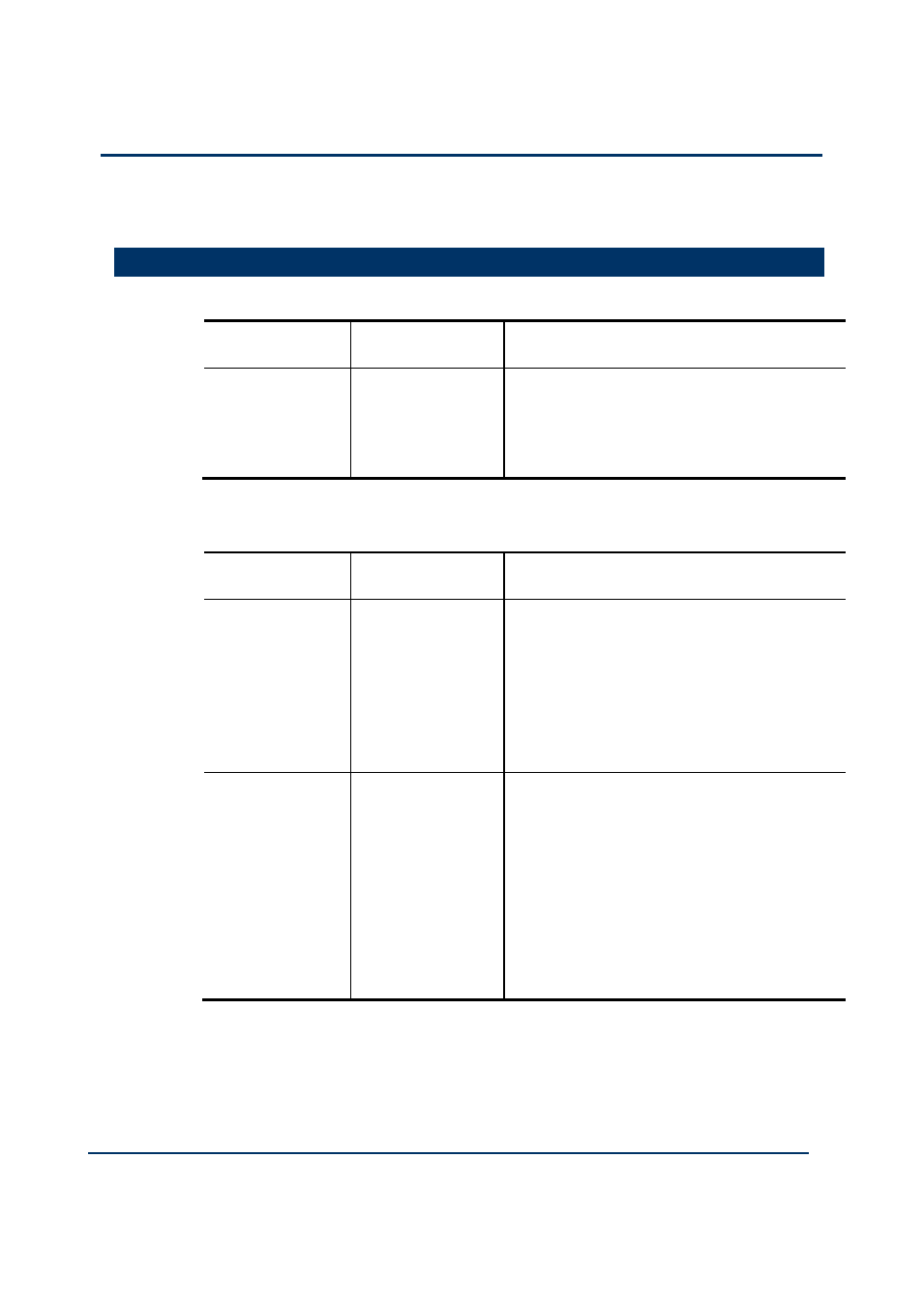
3-14
Document: 553630
ICSTT-RM446K-EN-P Issue: 10
_C
Safety Manual (AADvance Controller)
Planned Certified Configurations
Table 10:
Central Modules
Modules
TÜV Certified
Configuration
Conditions
Processor Module
T9110
1oo1D, 1oo2D,
2oo3D
Safety-related and can be used for safety-critical
applications in SIL2 with 1 module fitted and SIL3
applications with 2 or 3 modules fitted.
Note: For High Demand applications you must use
a minimum of two processors.
Table 11:
Input Modules
Modules
TÜV Certified
Configuration
Conditions
Digital Inputs
T9401/2, 24V dc,
8/16 Channel,
isolated.
+
T9801/2/3 Digital
Input TA, 16 channel,
Simplex/Dual/TMR
1oo1D, 1oo2D,
2oo3D
De-energized to action (normally energized): SIL3
with 1, 2 or 3 modules fitted.
Energize to action (normally de-energized): with 1, 2
or 3 modules fitted
Note: when the integrity level is at 1oo1D then the
faulty module must be replaced to restore the
integrity level back to 1oo2D.
Analogue Inputs
T9431/2, 8/16
Channel, isolated
+
T9831/2/3 Analogue
Input TA, 16
Channel,
Simplex/Dual/TMR
1oo1D, 1oo2D,
2oo3D
Within the manufactures specified safety accuracy
limits of 1%. The safety state of the analogue input
has to be set to a safe value which is a calculated
value based on a count value of 0mA. (refer to the
AADvance Configuration Guide Doc no: 553633 for
more details)
SIL3 with 1, 2 or 3 modules fitted.
Note: when the integrity level is at 1oo1D then the
faulty module must be replaced within the MTTR
assumed for the PFD calculations to restore the
integrity level back to 1oo2D.