Rockwell Automation SP200 AC Drive, 1 2 Channel Analog, Preset Speed User Manual
Page 34
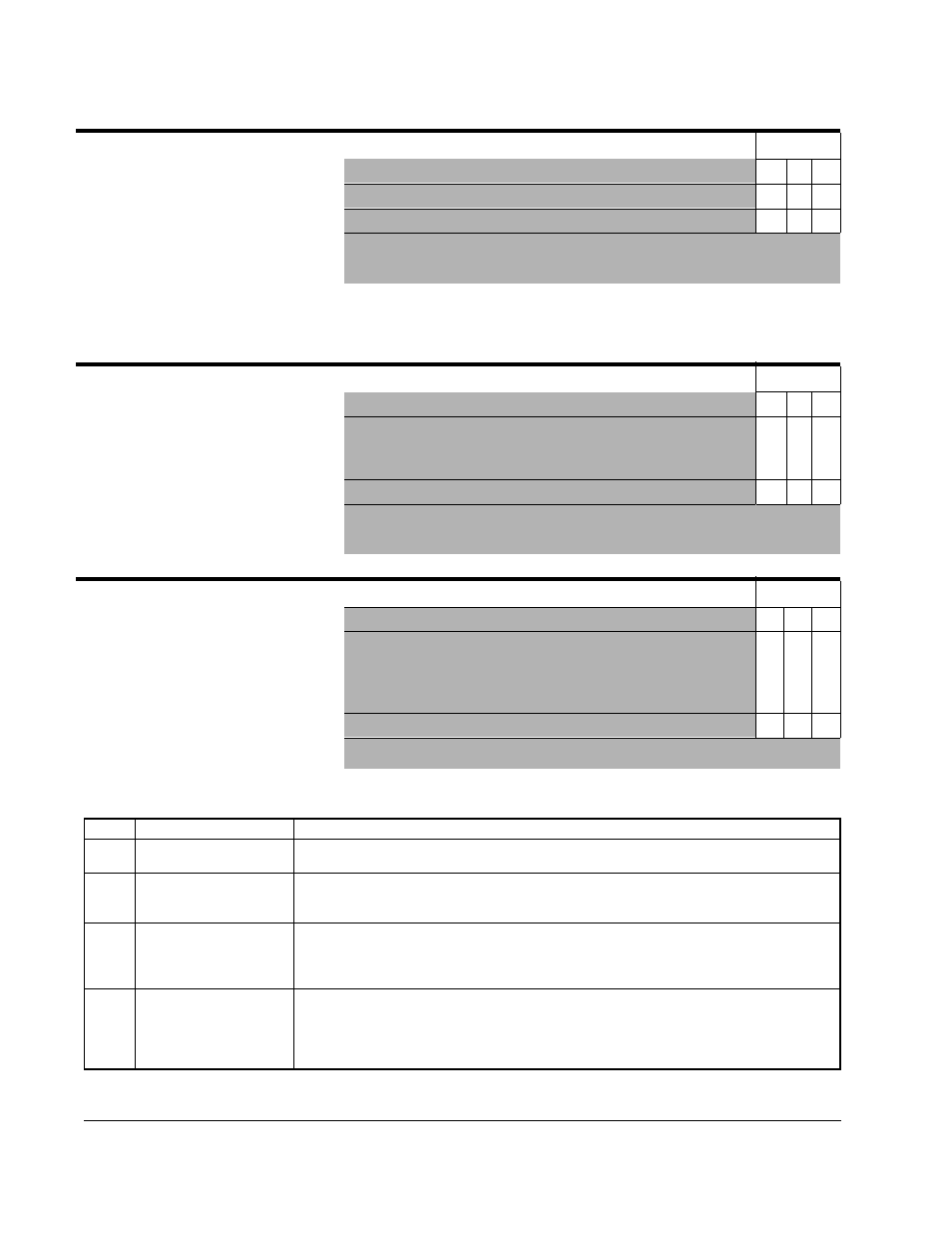
7-12
Installing and Operating the SP200 AC Drive
P-27 Process Integral Gain
Model
A
B
C
Use this parameter to specify the
integral gain (Kp) for the closed loop
process PI controller. It is used only
when P-29 (Process Operation) is
set to 2 or 3 to select PI control or
Parameter Range:
0 to 10.00 (x.x decimal)
X
Default Setting:
0
X
Running Access:
RW
inverted PI control. This parameter is scaled so that when it is set to 1.0, the process response is 10 Hz/sec
when the process error is 1 Hz. The correct value for this parameter depends on the dynamics of the process
being controlled, as well as the desired response.
P-28 Process Reference
Model
A
B
C
Use this parameter to select the
reference source for (P-29) Process
Operation.
Parameter Range:
0 = Analog Input 1
1 = Keypad
2 = Internal/Jog Frequency
X
X
X
Default Setting:
0
X
Running Access:
RW
P-29 Process Operation
Model
A
B
C
Use this parameter to specify the type
of operation performed by the
process controller. It is used only
when P-20 (Main Speed Reference)
is set to the value 4 to select the
process output as the main speed
reference. The table below describes
Parameter Range:
0 = Add
1 = Multiply
2 = PI Control
3 = Inverted PI Control
X
X
X
X
Default Setting:
0
X
Running Access:
RW
the different types of process operations.
Value
Process Operation
Description
0
Add
Add the process reference selected by P-28 and Analog Input 2. The resultant sum is the process
output.
1
Multiply
Multiply the process reference selected by P-28 by Analog Input 2. The resultant product is the
process output. In this case, Analog Input 2 is a gain that ranges from 0.0 when the input is equal
to P-24 (Analog Input 2) Offset to 1.0 when the input is equal to P-25 (Analog Input 2 Gain).
2
PI Control
Calculate the process error by subtracting Analog Input 2 from the process reference selected by
P-28. This error along with P-26 (Process Proportional Gain) and P-27 (Process Integral Gain)
are used to calculate the process output so that the process error is forced to zero. Use this setting
to control a system variable that is directly proportional to motor speed.
3
Inverted PI Control
Calculate the process error by subtracting the process reference selected by
P-28 from Analog Input 2. This error along with P-26 (Process Proportional Gain) and P-27
(Process Integral Gain) are used to calculate the process output so that the process error is
forced to zero. Use this setting to control a system variable that is inversely proportional to motor
speed.