Plc-5 block transfer instructions, Application program #1, 10ć3 – Rockwell Automation 1771-QB Linear Pos. User Manual
Page 147: Sample application programs chapter 10
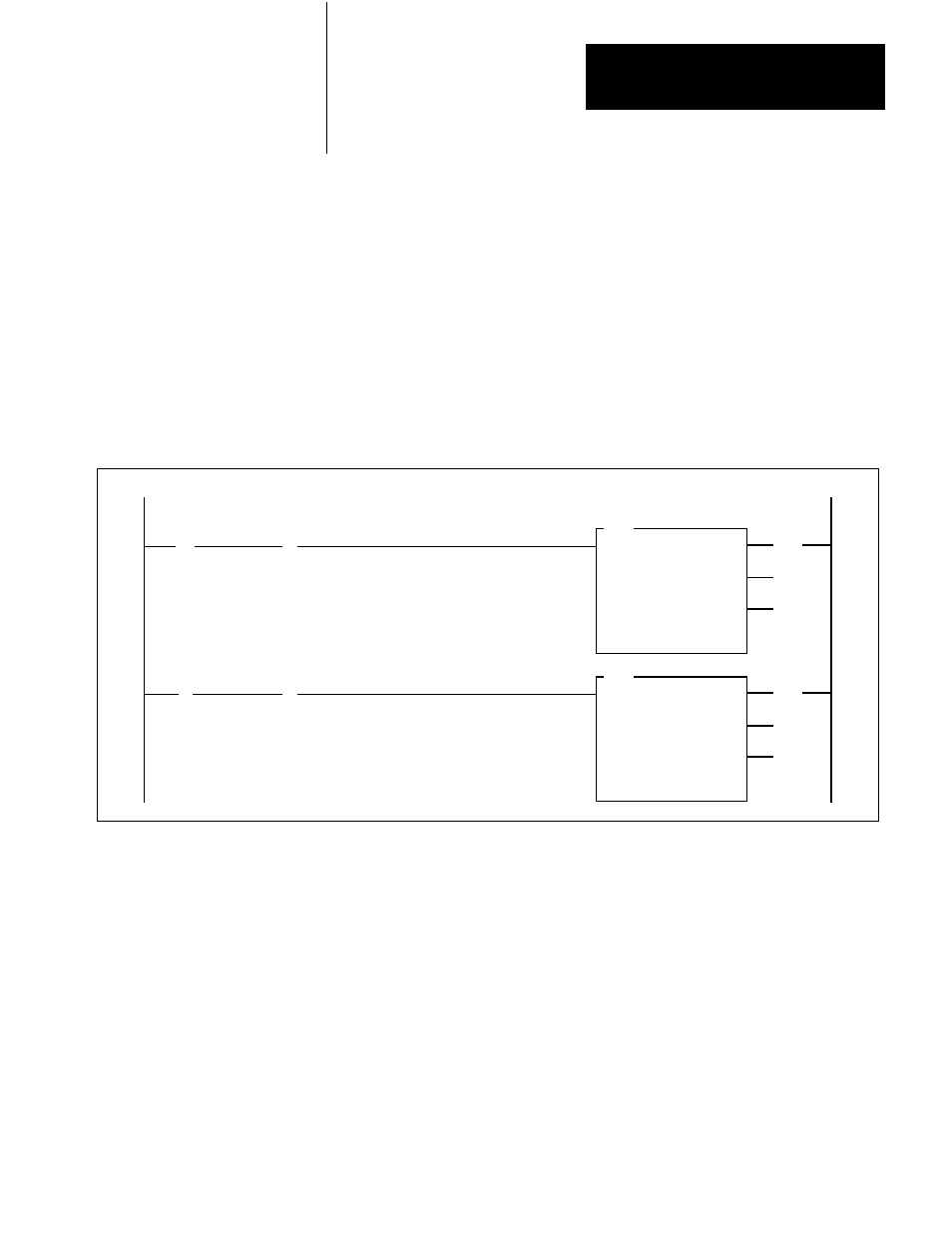
Sample Application Programs
Chapter 10
10Ć3
You should program a PLC-5 processor’s block transfer to use the bidirectional
method to avoid problems when troubleshooting the module. However, block
transfer writes only need to be enabled when a command block, motion blocks,
setpoint blocks or a parameter block must be sent to the module.
Important: Processor execution of block transfer instructions is asynchronous
to the program scan. The status of these bits could change at any point in the
program scan. If the data must be synchronized to the program scan, transfer the
block transfer read instruction to a storage location via a file-to-file move. The
program can then examine data in the storage location.
Figure 10.2
Block Transfer Instructions for PLCĆ5 Controllers
50112
BTR
ENABLE
N7:0
] / [
15
BTW
ENABLE
N7:5
] / [
15
BTR
BLOCK TRNSFR READ
Rack 00
Group 0
Module 0
Control Block N7:0
Data file N44:1
Length 33
Continuous N
( EN )
( DN )
( ER )
BTR
ENABLE
N7:0
] / [
15
BTW
ENABLE
N7:5
] / [
15
BTW
BLOCK TRNSFR WRITE
Rack 00
Group 0
Module 0
Control Block N7:5
Data file N45:131
Length 0
Continuous N
( EN )
( DN )
( ER )
With this simple application program, the module controls the motion of a
single axis. Figure 10.3 shows the axis movement profile. Four setpoints in the
setpoint block control axis motion for this loop. The first three setpoints specify
local velocity and acceleration/deceleration, while the fourth setpoint uses the
global velocity and acceleration/deceleration defined in the parameter block.
Setting the fourth setpoint’s local acceleration and deceleration words to zero
forces it to use global parameters. The first three setpoints cause axis movement
in one direction, while the fourth returns the axis to the original position.
PLCĆ5 Block Transfer
Instructions
Application Program #1