Zero algorithms 62 – MTS SWIFT 20 Ultra Sensor User Manual
Page 62
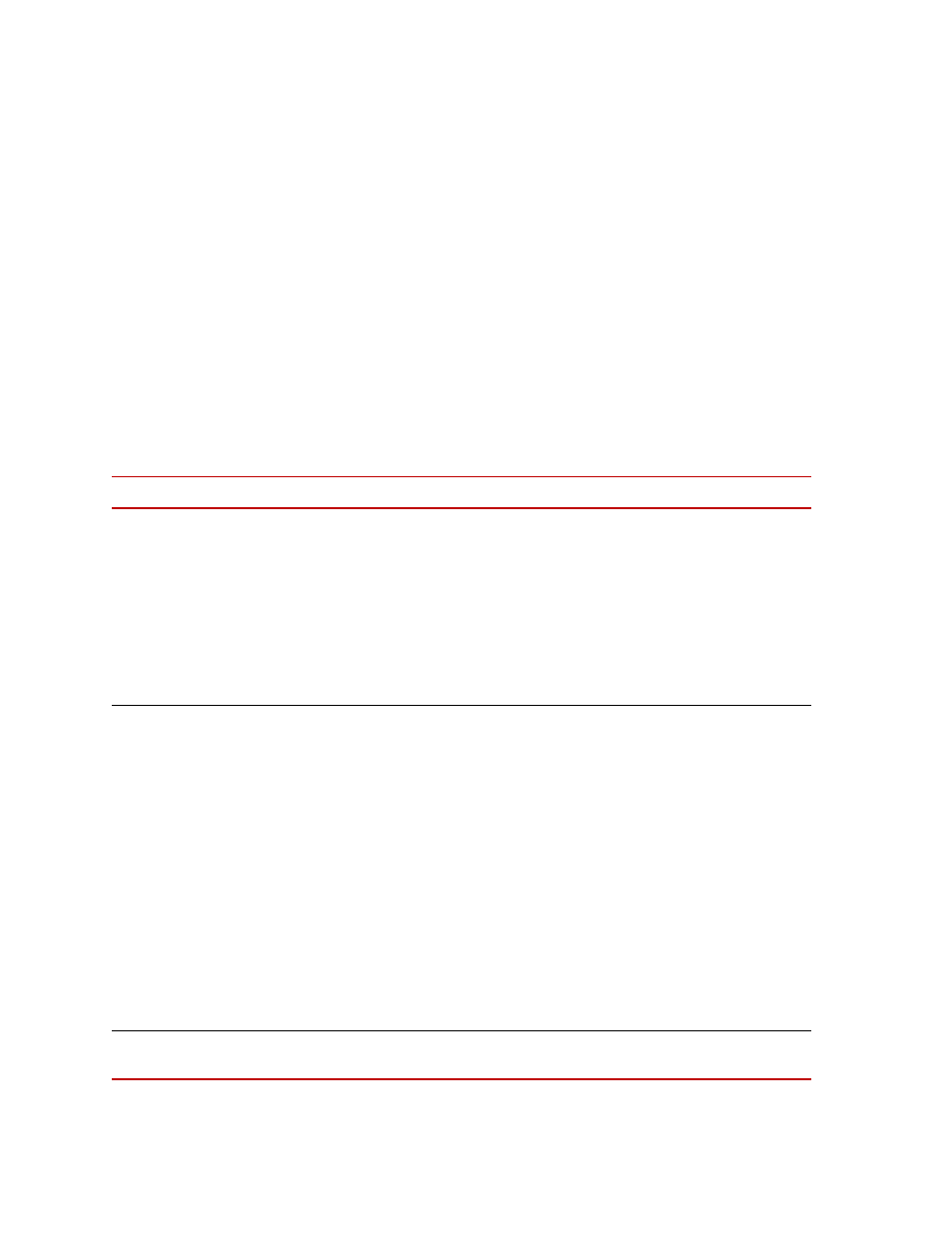
SWIFT 20 Sensors
62
Select a Zero Method
Setting up the Low-Profile Transducer Interface
Items you may edit
•
OutputPolarities–defines the polarities of the six outputs. Change these
only if your application requires different polarities from those on the
transducer label.
•
ZeroAlgorithm–selects a zero algorithm for the application.
•
AngleMode–selects the mode used for determining the encoder sine and
cosine.
•
AngleFixed–used for non-spinning applications.
•
AngleOffset–used for spinning applications. Normally you do not need to
change this value.
•
EncoderSize–defines the size of the encoder. The value will typically be 1
for the spinning slip ring.
•
Zero Algorithms
The following table lists the different values available and the angle zero
and bridge zero functions that they perform:
Zero Algorithm Values Defined (part 1 of 2)
Zero Algorithm
When to Use
Bridge Zero
Angle Zero
0
Use this algorithm
for non-spinning
(road simulator)
applications.
(AngleMode=1)
When you press the Bridge
Zero button, the TI measures
the static transducer bridge
offsets. It sets up zero DACs
to provide 0.0 V raw bridge
output.
The Bridge Zero LED will
light for 3–4 seconds, and will
go off when the zero process
is complete.
The Angle Zero button is non-
functional.
1
This is the
algorithm for
spinning (test
track) applications.
You will need to
mechanically level
the SWIFT sensor.
The transducer is
unloaded during
the zero process.
(AngleMode=0)
When you press the Bridge
Zero button, the TI will
collect one revolution of raw
bridge data, average the data,
and remove the DC offset by
setting the zero DACs to the
average value.
The Bridge Zero LED will
light continuously until the
wheel is turned for one
revolution (index-to-index).
After one revolution of data is
collect, it will flash (at
approximately 4 Hz) for 30
seconds while the bridge zero
values are computed.
When you press the Angle Zero
button, the TI will read the current
angle and use the value to set the
angle sum to 0.0 degrees.
The Angle Zero LED will light for a
few seconds while the TI sets the
angle offset value.
If you do not press the Angle Zero
button, the value for AngleOffset
will not be updated in the calibration
file.
The wheel must be rotated past the
encoder index pulse at least once
after power up so that the electronics
can determine the absolute angular
position.
2
Reserved for future
use.
N/A
N/A