Safety instructions – Lenze EVF9333−xV User Manual
Page 32
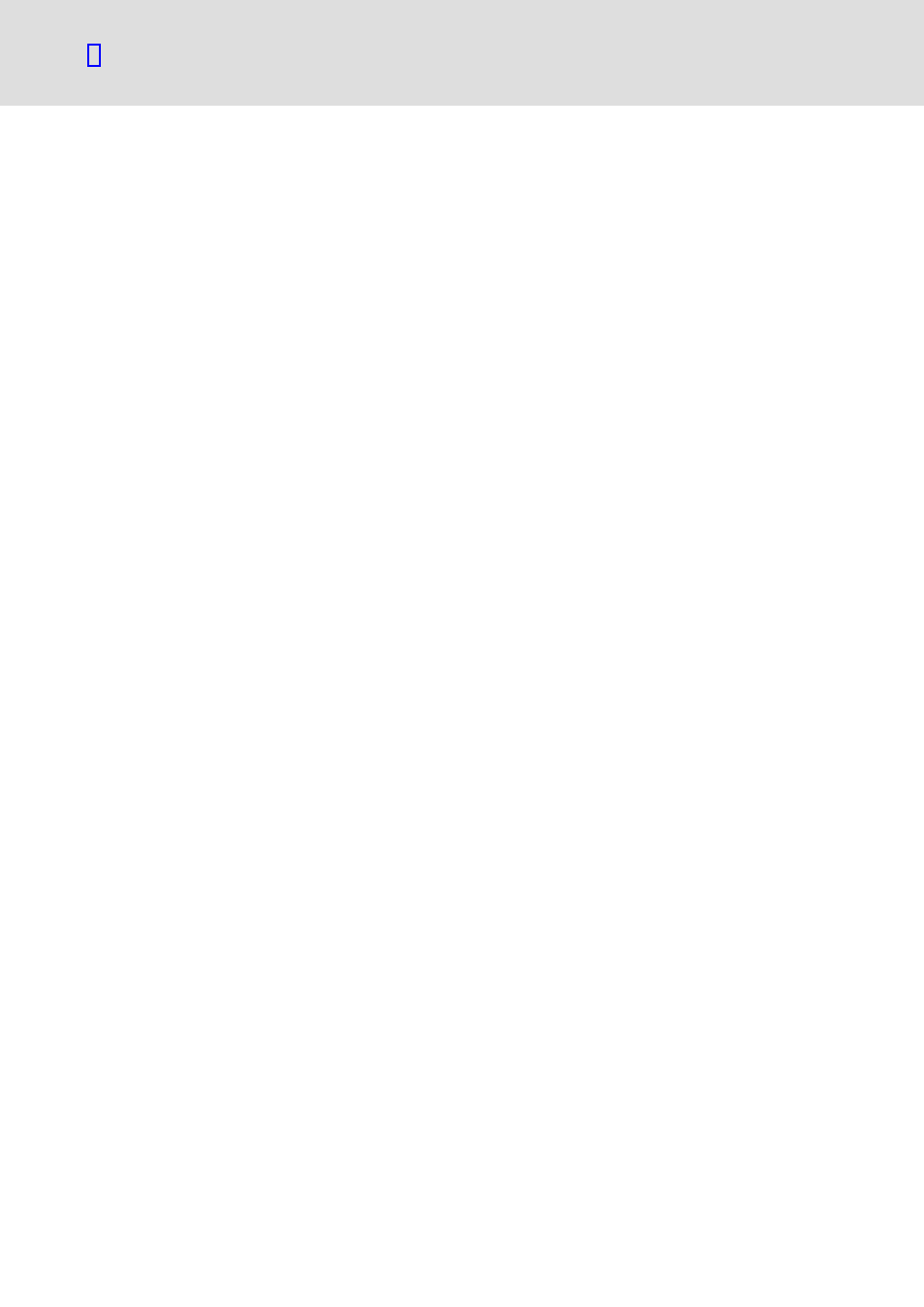
Safety instructions
Residual hazards
2.3
l
2.3−2
EDSVF9333V EN 6.2−04/2012
ƒ Controllers can cause a DC current in the PE conductor. If a residual
current device (RCD) or a fault current monitoring unit (RCM) is used
for protection in the case of direct or indirect contact, only one
RCD/RCM of the following type can be used on the current supply side:
– Type B for the connection to a three−phase system
– Type A or type B for the connection to a single phase system
Alternatively another protective measure can be used, like for instance
isolation from the environment by means of double or reinforced
insulation, or isolation from the supply system by using a transformer.
ƒ Frequent mains switching (e.g. inching mode via mains contactor) can
overload and destroy the input current limitation of the drive
controller:
– At least 3 minutes must pass between switching off and restarting
the devices EVF9321−xV and EVF9322−xV.
– At least 3 minutes must pass between two starting procedures of the
devices EVF9323−xV ... EVF9333−xV.
– Use the "safe torque off" safety function (STO) if safety−related mains
disconnections occur frequently. The drive variants Vxx4 are
equipped with this function.
ƒ For some controller settings, the connected motor may overheat (e.g.
when operating the DC injection brake or a self−ventilated motor at
low speed for longer periods).
– Using an overcurrent relay or a temperature monitoring device
provides a large degree of protection against overload.
– We recommend to use PTC thermistors or thermal contacts for motor
temperature monitoring. (Lenze three−phase AC motors are equipped
with thermal contacts (NC contacts) as standard)
– PTC thermistors or thermal contacts can be connected to the
controller.
ƒ Drives can attain dangerous overspeeds (e.g. setting of high output
frequencies with motors and machines not qualified for this purpose).
Device protection
Motor protection