6 automatic collection of motor data, Automatic collection of motor data, Commissioning – Lenze EVF9333−xV User Manual
Page 202
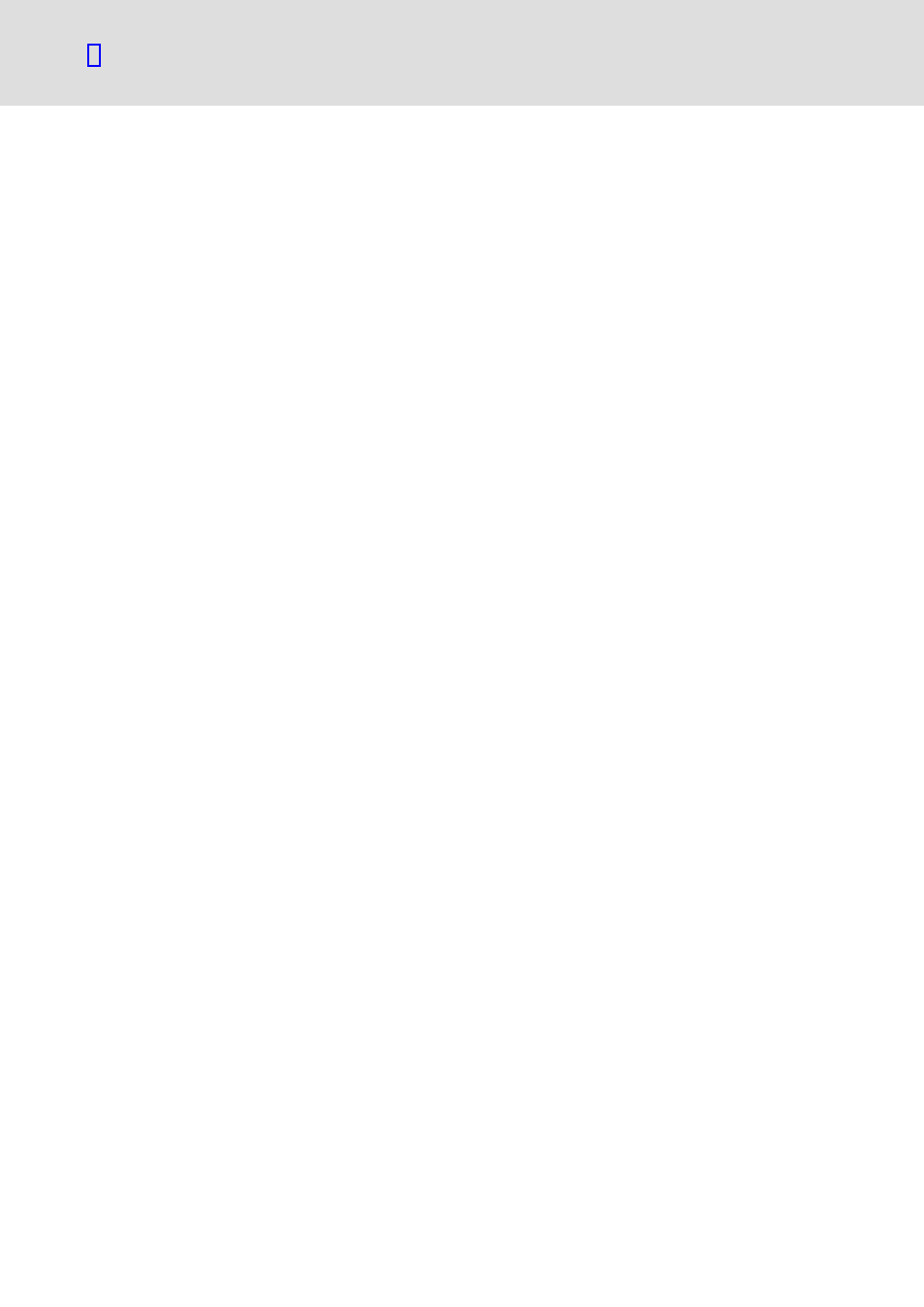
Commissioning
Adjusting the motor
Automatic collection of motor data
6.6
6.6.6
l
6.6−14
EDSVF9333V EN 6.2−04/2012
ƒ Set the acceleration and deceleration times so that the drive can follow
the speed profile without reaching I
max
of the drive controller.
ƒ A correct current control in generator mode is only possible with an
external brake resistor.
ƒ Drive behaviour with overload in motor or generator mode
(C0054 > C0022 or C0023):
– The drive controller reduces the speed up to 0 min
−1
.
– The drive controller cancels the change of the speed if the load falls
below the limit value again.
ƒ When operating with a switching frequency > 8 kHz or 4 kHz, C0022
and C0023 must be adapted to the permissible output currents
(Derating).
ƒ Correct current (C0075, C0076) in generator mode is only possible with
connected brake chopper or DC−bus operation with energy exchange.
6.6.6
Automatic collection of motor data
The motor data identification serves to detect the required motor data and
influences of the motor cable.
Before executing the identification you must manually enter the motor data
from the motor nameplate into the corresponding codes.
Vector control (C0006 = 1)
In the vector control mode the motor data identification must be executed
before initial commissioning.
ƒ In case of vector control without temperature feedback, the heating of
the motor in the motor model is not taken into consideration.
ƒ In case of vector control with thermal sensor KTY a motor temperature
of 20 °C in the motor model is considered.
Important: The temperature feedback must be activated (C0594 = 0 or
C0594 = 2) before you execute the motor data identification.
V/f characteristic control (C0006 = 5)
In the Lenze setting, the controllers are defined for a power−adapted motor
with 10 m of motor cable. Therefore the motor data identification is not
essential.
ƒ The identification of the motor data also influences the smooth
running behaviour. When identifying the motor data for this operating
mode, you can optimise the smooth running behaviour at low speeds.
Adjustment
Description