Functional safety engineering, General information and intended use, 1 general information and intended use – Festo Контроллер двигателя CMMD-AS User Manual
Page 77
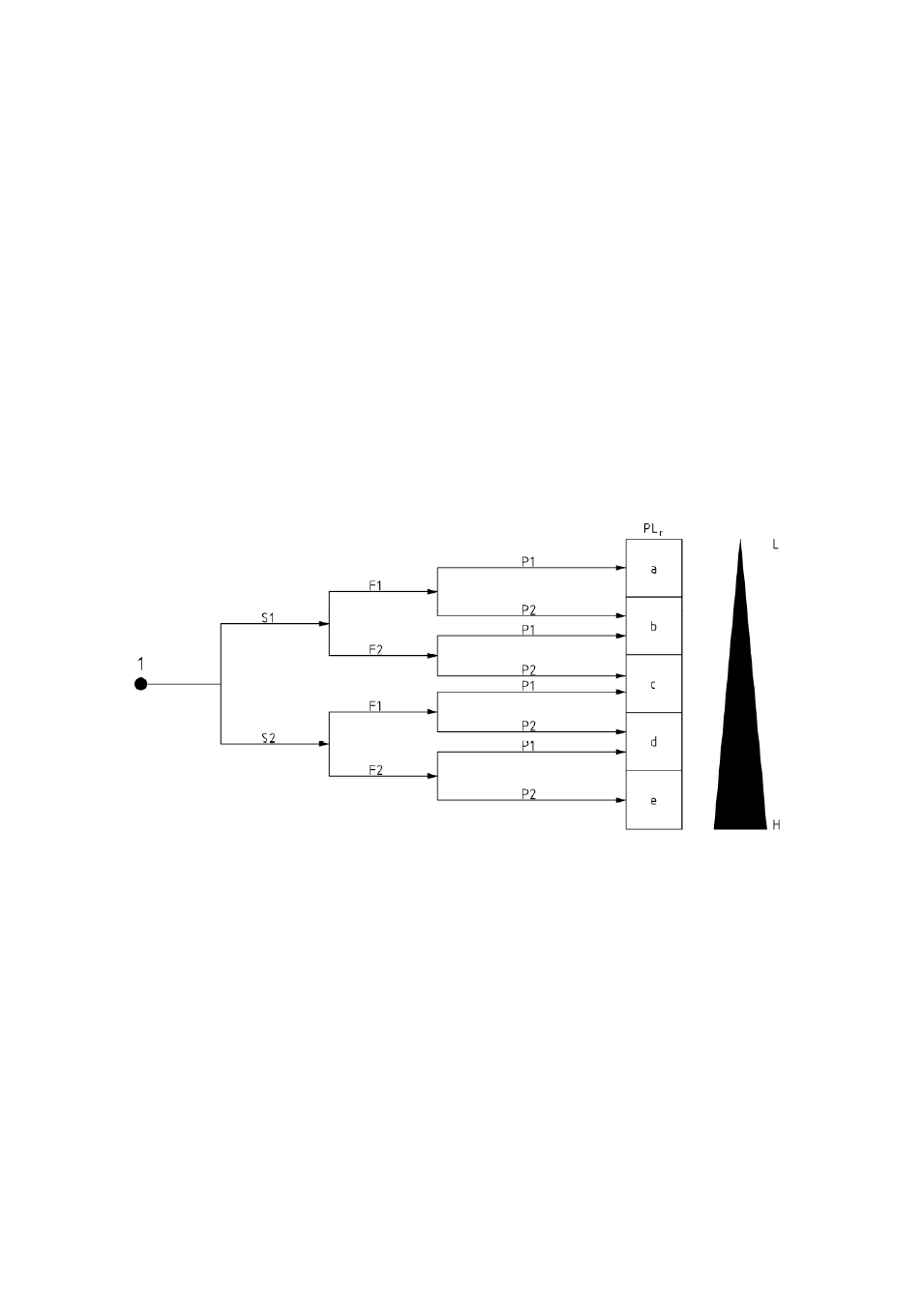
4. Functional safety engineering
Festo P.BE-CMMD-AS-HW-EN 1002NH
77
4.
Functional safety engineering
4.1
General information and intended use
The CMMD-AS family of position controllers supports the "Safe torque off (STO)" and
"Safe Stop 1 (SS1)" safety function, providing protection against unexpected starting up
in accordance with the requirements of the standard EN 61508, SIL 2 as well as
EN ISO 13849−1, PL d.
Bringing the machine to a standstill must be carried out and ensured by the machine
control system. This especially applies to vertical axes without automatic-locking
mechanics or counterbalancing.
Based on a danger analysis/risk evaluation performed in accordance with the
EC machinery directive 2006/42/EC or EN ISO 12100 and EN 14121, the machine
manufacturer must design the safety system for the entire machine, including all
integrated components. This also included the electric drives.
The new EN ISO 13849 standard uses a changed risk graph for risk analysis and
a deviating principle to achieve the requirements compared to EN 9549.
1
Starting point for evaluation of the risk reduction contribution
L
Low contribution to risk reduction
H
High contribution to risk reduction
PL
r
Required performance level
Risk parameter
S
Severity of injury
S1
Slight (generally reversible injury)
S2
Serious (generally irreversible injury, including death)
F
Frequency and/or duration of the exposure to hazard
F1
Seldom to less often and/or the time of the exposure to hazard is short
F2
Frequent to continuous and/or the time of the exposure to hazard is long
P
Possibility to avoid the hazard or limit the damage
P1
Possible under certain conditions
P2
Scarcely possible
Fig. 4.1 Risk graph for definition of the PLr for each safety function