Fig. 3.12 behaviour with teach input – Festo Контроллер двигателя CMMD-AS User Manual
Page 68
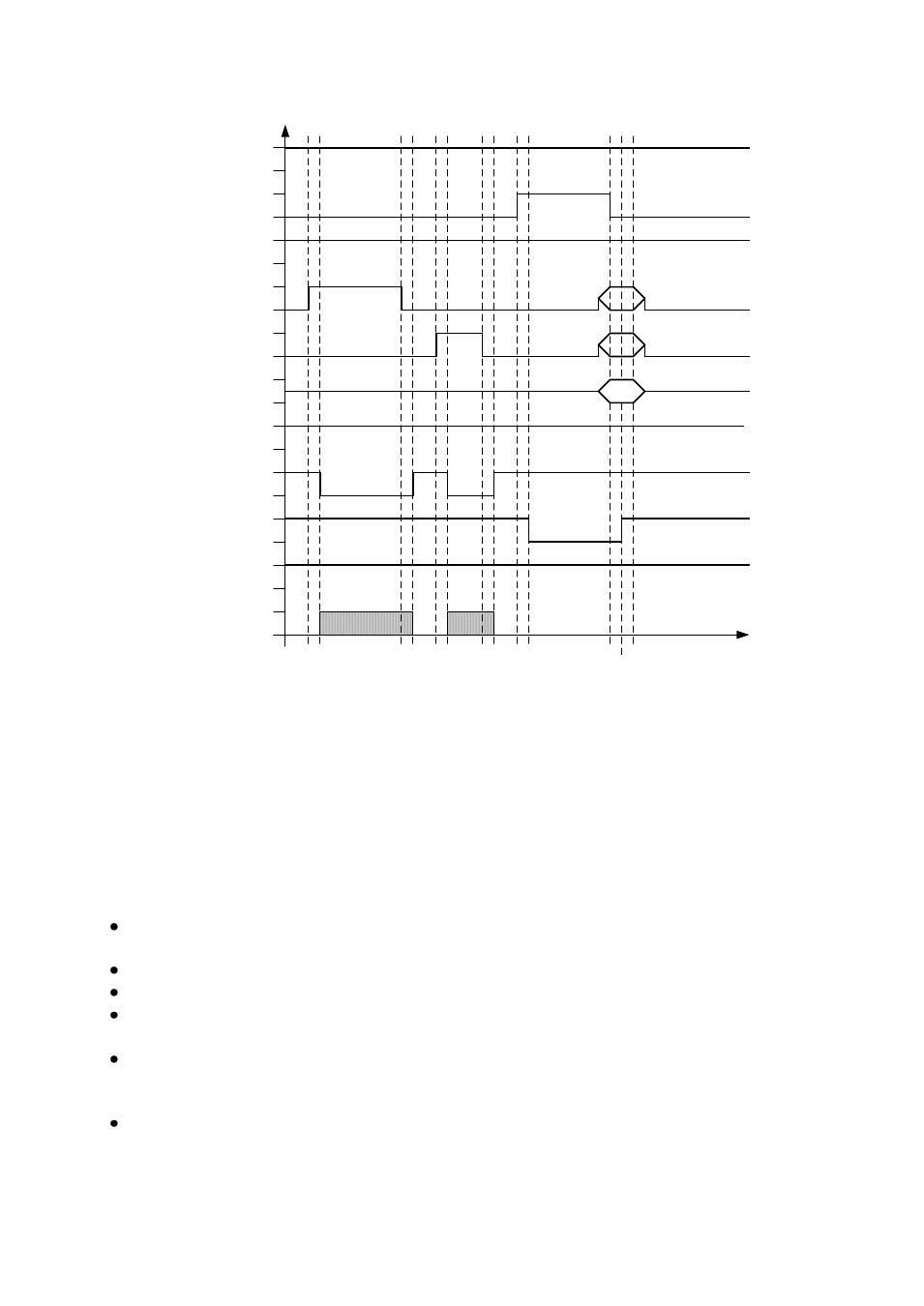
3. Product description
68
Festo P.BE-CMMD-AS-HW-EN 1002NH
ENABLE
START / TEACH
STOP
1
0
1
0
1
0
1
0
1
0
1
0
1
0
1
0
1
0
–
1
0
+
(1)
(1)
DIN0 - DIN3
1
0
(1)
DOUT0: READY
DOUT1: MC
DOUT2: ACK-TEACH
DOUT3: ERROR
t1
t1
tx
tx
t1
t1
t1
DIN11: Tipp -
DIN10: Tipp +
t1
= 1.6 ms
tx
= x ms (dependent on brake ramps)
(1)
Setting of the target position to be programmed
Fig. 3.12 Behaviour with teach input
3.7.12 Position record linking with positioning/torque control
switching
The route program allows multiple positioning jobs per axle to be linked in a sequence.
These positions are travelled to one after another.
The characteristics of the route program are:
All 63 position records of the positioning record table per axle can be set in the route
program. The positioning records of the two axes cannot be combined with each other.
Besides linear sequences, ring-shaped linkages are also allowed (endless linkage)
For each route program step, a free following position can be set.
As a step enabling condition, 2 digital inputs per axle are available as NEXT 1 and
NEXT 2.
There are 7 possibilities to jump into the route program with I/O control, that is,
7 different sequences per axle are possible. Under FHPP, the entry is freely selectable
and the number limited only by the maximum number of position sets.
The program lines of the route program are worked off every 1,6 ms. This ensures that
an output set by the route program remains set for at least 1.6 ms.