Shaft encoder motor – endat 2.1 and 2.2 [x2.1/2, 18 v – Festo Контроллер двигателя CMMD-AS User Manual
Page 108
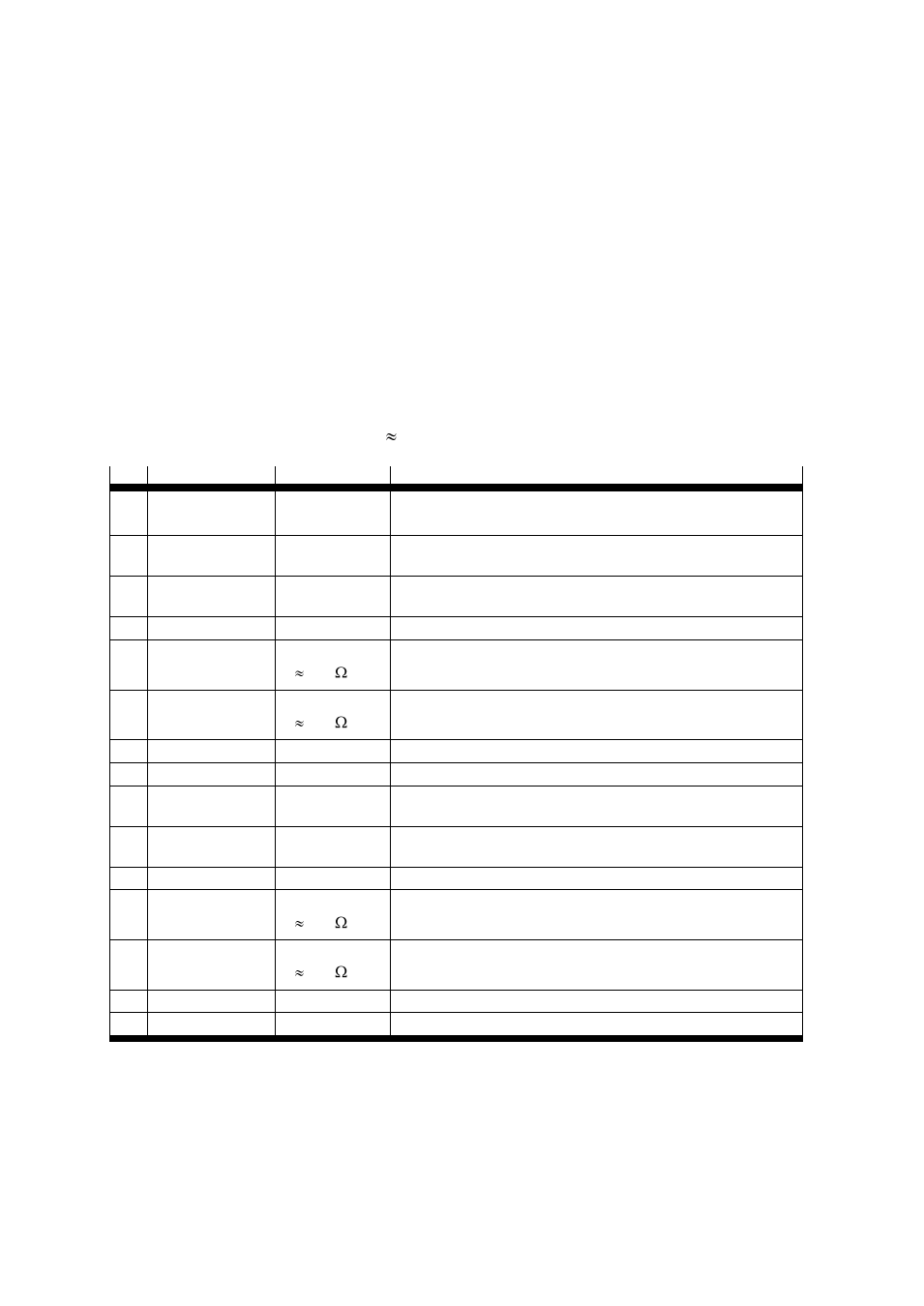
6. Electrical installation
108
Festo P.BE-CMMD-AS-HW-EN 1002NH
6.4.2
Shaft encoder motor – EnDat 2.1 and 2.2 [X2.1/2]
Only encoders with digital EnDat 2.1 or 2.2 interface with a maximum power consumption
of 200 mA are supported.
Operating voltage for the encoder is taken from the internal +5 V logic supply. An
adjustment to maximum power of the voltage drops on the encoder connection cable is
not planned (and for EnDat 2.2/22 encoder also not necessary).
The tolerance of the encoder supply voltage is limited downward in order to operate older
Heidenhain encoders with EnDat 2.2/01 interface. But depending on power consumption
and cable length, it may be necessary to double the wiring of the supply lines.
Example:
Encoder wiring with the cross section of 0.5 mm²
Cable length of 25 m, (= 50 m line to and from)
Double wiring
Voltage drop with single wiring U
diff
0.18 V
Pin Designation
Value
Specification
1
MT+
+3.3 V / 3 mA
Motor temperature sensor, NC, PTC, KTY...
Not occupied with NEBM lines
2
U_SENS-
5 V –0
% / +5
%
I
max
= 200 mA
Connected internally with pin 3
3
GND
0V
Reference potential for encoder supply and motor
temperature sensor
4
n.c.
5
#DATA
5 V
ss
R
I
120
Bidirectional RS485 data cable (differential) Zero impulse
transmission with HYPERFACE
6
#SCLK
5 V
ss
R
I
120
Cycle output RS485 (differential) for data transfer
via the EnDat interface
7
n.c.
8
n.c.
9
U_SENS+
5 V -0
% / +5
%
I
max
= 200 mA
Connected internally with pin 10
10
US
5 V -0
% / +5
%
I
max
= 200 mA
Operating voltage for EnDat encoder
11
n.c.
12
DATA
5 V
ss
R
I
120
Bidirectional RS485 data cable (differential) Zero impulse
transmission with HYPERFACE
13
SCLK
5V
ss
R
I
120
Cycle output RS485 (differential) for data transfer
via the EnDat interface
14
n.c.
15
n.c.
Table 6.6 Pin allocation of shaft encoder motor EnDat 2.1 and 2.2. [X2.1/2]