Siemens SIMATIC NET PROFIBUS User Manual
Page 373
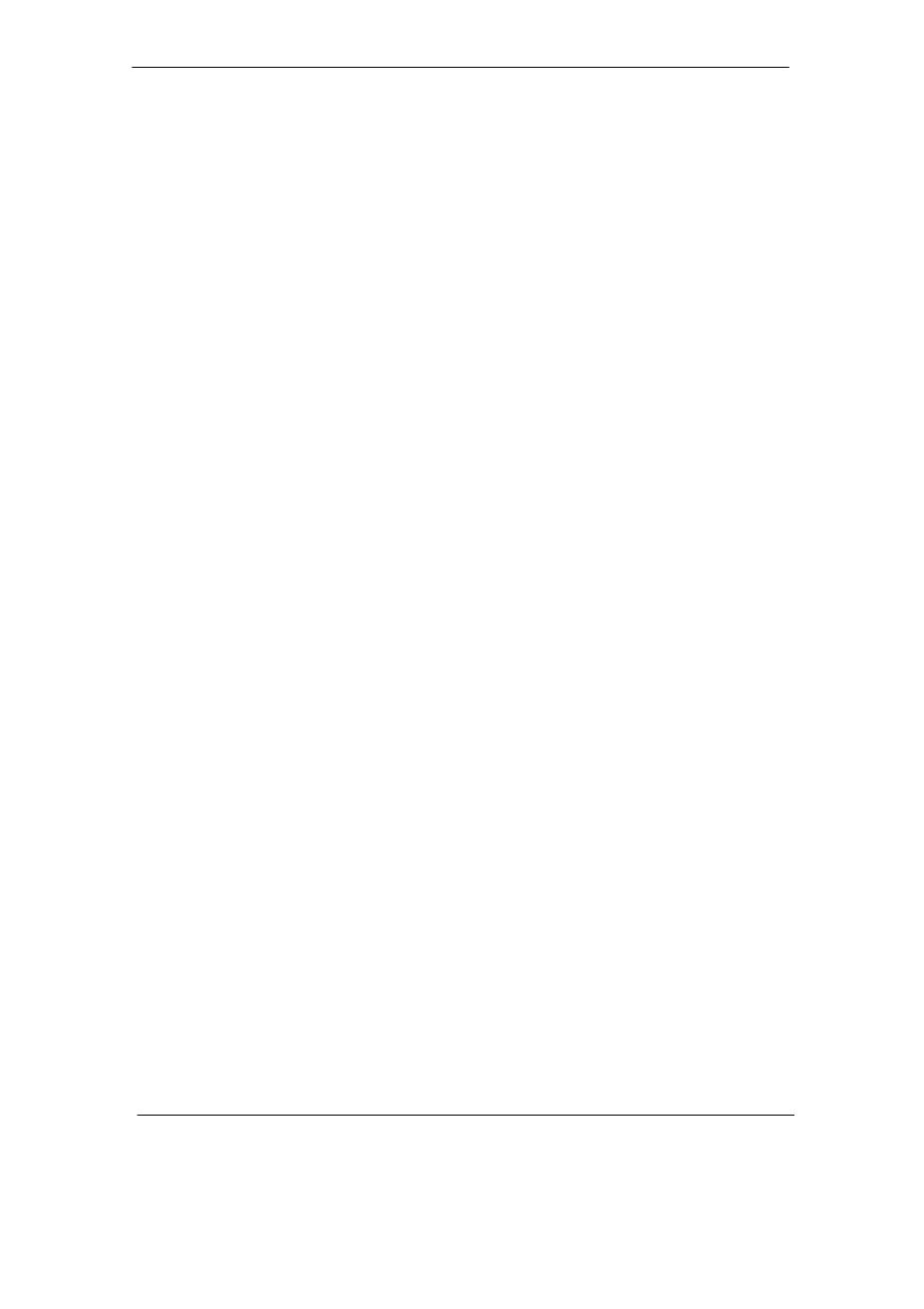
Infrared Link Modul (ILM)
6ZB5530–3AC30–0BA1
31
Copyright
by Siemens
Make sure that there are no infrared sources in the illumination cone in front of a PROFIBUS ILM. There
should also be no reflecting surfaces in any part of the illumination cone to avoid reflecting back the modules
own emission.
Before mounting the PROFIBUS ILM, connect the power supply and PROFIBUS cables if the site where the
module is being installed is awkward to reach.
Mount the PROFIBUS ILM on a low-resistance and low-inductance earthed metal wall, support or mounting
plate. Make sure that there is a reliable electrical connection between the ILM casing and the mounting plate.
Use toothed washers under the screw heads to break through any paint. Secure the modules with machine
screws (for example M 4 x 30).
The most suitable way of mounting the PROFIBUS ILM is to use a support that allows the module to be aligned
with the partner station.
A suitable support would be as follows:
-
Mechanically stable
-
Low-resistance and low-inductance connection to ground or the vehicle chassis
-
Adjustable so that optimum alignment along the optical axis to the partner station is possible.
-
Simple and cheap to make
-
Corrosion-proof depending on the characteristics of the installation site.
One possible design of a support is the mounting angle shown in Figure 12. This can be made easily in any
workshop (cutting sheet metal, bending, drilling). Each support requires two identical angles to allow
adjustment in two axes.
The angles are bolted together with standard components such as M4 or M6 bolts, washers or toothed
washers and M4 and M6 nuts.
3 mm thick sheet aluminum is, for example, suitable or galvanized 2 mm sheet steel. If suitable profile material
is available, this makes construction even simpler since it is not necessary to bend the arm.