Yaskawa i80M Connecting Manual User Manual
Page 280
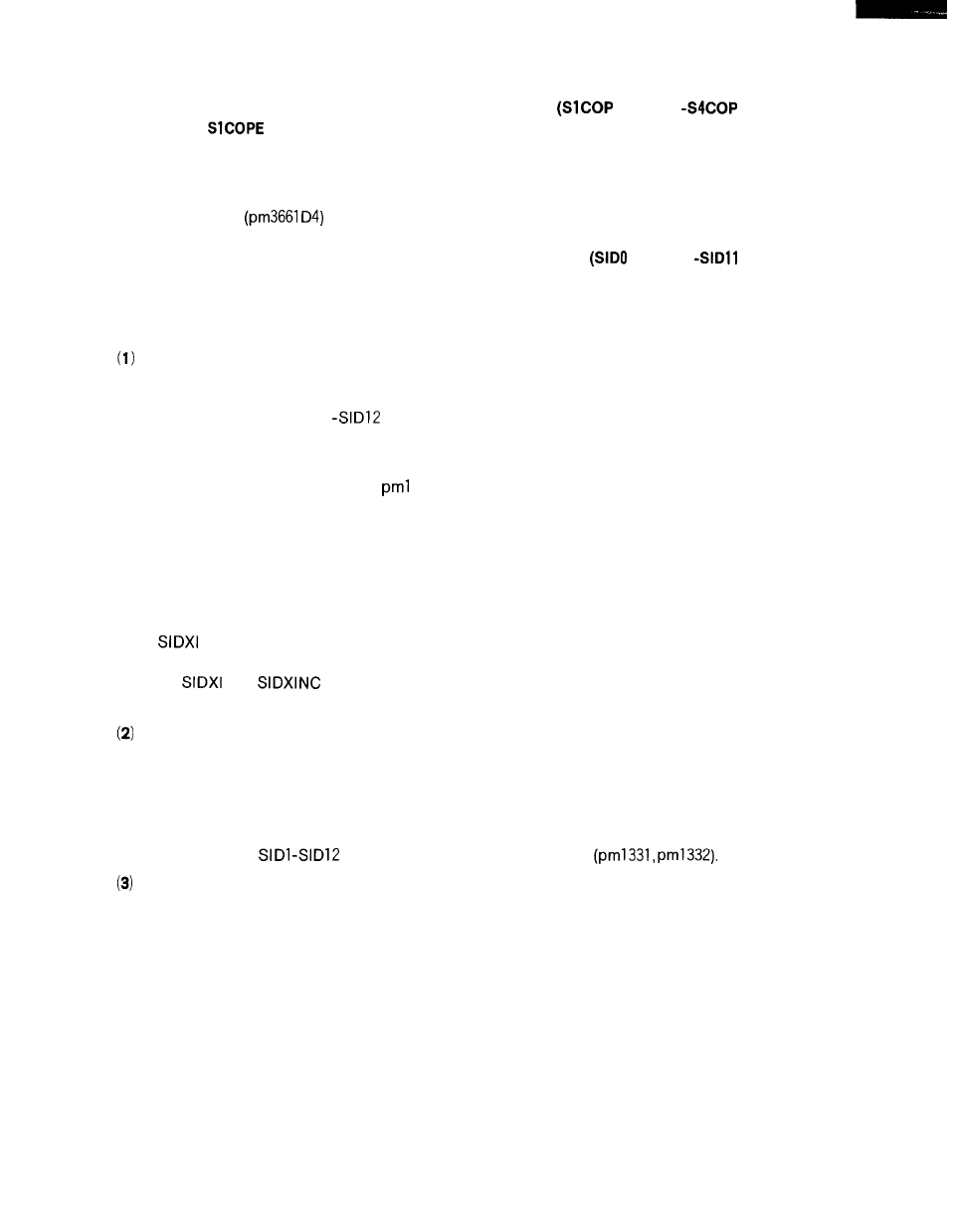
21. 3.4.6 SPINDLE INTERLOCK INPUTS AND OUTPUTS
# 31150
# 31153,
# 36514-S4COPE # 36517)
These signals are used to rotate two spindles at the same speed.
When, for instance, copying the first spindle command to the second spindle, set the second
spindle control S1 COP to 1 (pm3125 DO = 1). While a copy is being made, the second spindle
control S1 COPE
is 1.
21. 3.4.7 SPINDLE INDEX FUNCTION INPUTS AND OUTPUTS
# 31180
#31193)
These 1/0 signals are used to exercise the “spindle index function” so that the S5-digit analog
output is controlled by the pulse output from the spindle pulse generator to stop the spindle at a
desired position.
Input Signals
(a) SIDO-SID11 : Binary 12-bit (0-4095) input for spindle stop position designation. It corres-
ponds to the pulse output (4096 pulses/rev) from the spindle pulse generator. The stop
position is usually SID1
input number of pulses away from the phase C pulse (1
pulse/rev) of the spindle pulse generator.
NOTE: The stop position can be shifted away from the phase C pulse by the amount de-
fined by parameters pml414 and
434.
(b) SIDX: This input request the control to perform spindle indexing.
When this input is closed during spindle rotation, the spindle stop command is issued, and
then the spindle indexing operation is performed after the spindle is stopped.
After completion of spindle indexing, the spindle rotating speed command analog voltage
remains as the spindle positioning command unless this input turns OFF, and the control
continues with spindle indexing.
(c)
: Spindle indexing restart input
SIDXINC: Spindle stop position selection incremental input
The
and
inputs are provided for the repeated spindle indexing sequence.
For details refer to (5) “Spindle Indexing Function Expansion Inputs”.
Output Signals
(a)
SIDXO: This output is ON while the control is executing the spindle indexing function
(while the creep rotating speed command and spindle positioning command outputs are
generated).
(b) SIDXA: Spindle indexing completion output.
This output is ON while the spindle indexed by the control is positioned within the range
defined by the
input and parameter setup pulses
Typical Spindle Indexing Time Charts
(a) Performing spindle indexing with the M code while the spindle is stopped
(Fig 21. 19)
(The spindle positioning mode is cleared after completion of spindle indexing.)
(b) Performing spindle indexing with the M code while the spindle is rotating in the normal
direction
(Even after completion of spindle indexing, the spindle positioning operation is continued
until the next spindle rotation command is issued.)
280