2 f undamentals of p a th f unctions – HEIDENHAIN iTNC 530 (340 49x-05) User Manual
Page 190
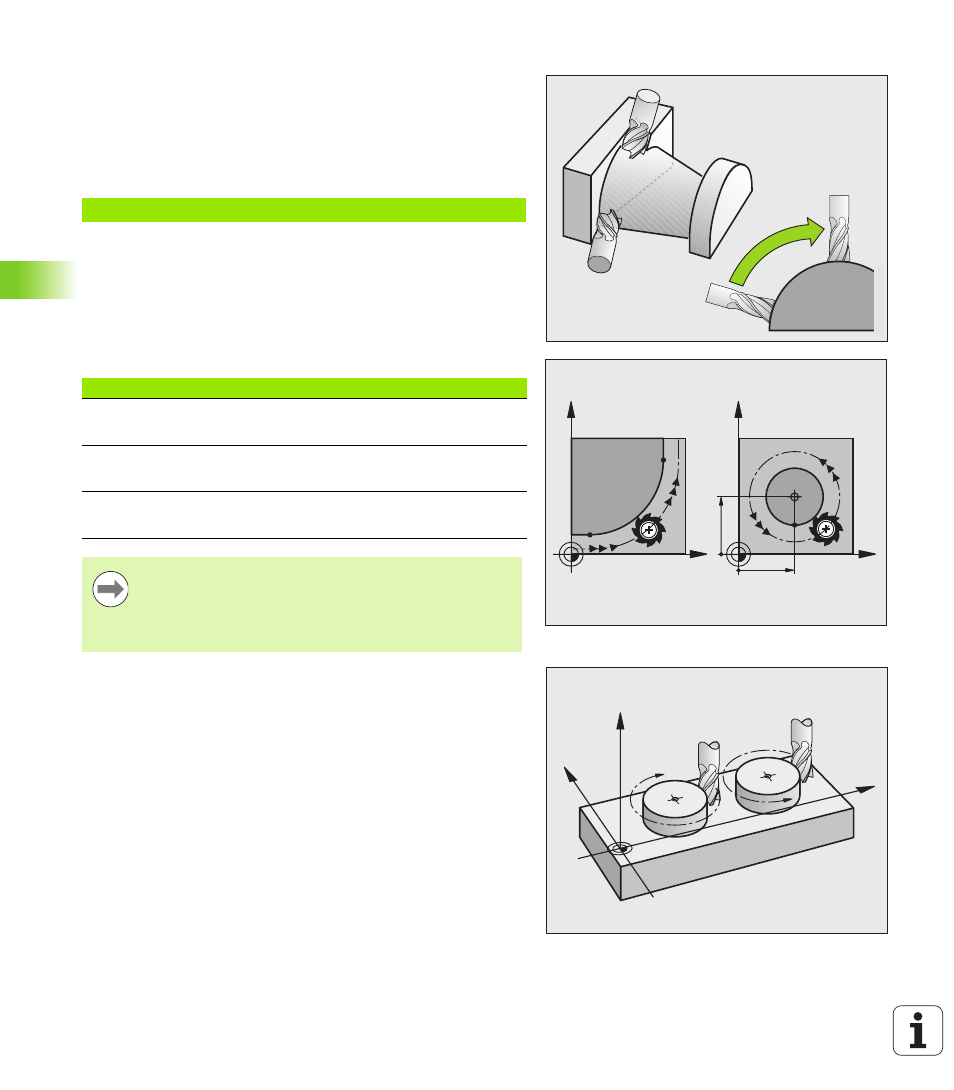
190
Programming: Programming Contours
6.2 F
undamentals of P
a
th F
unctions
Entering more than three coordinates
The TNC can control up to 5 axes simultaneously (software option).
Machining with 5 axes, for example, moves 3 linear and 2 rotary axes
simultaneously.
Such programs are too complex to program at the machine, however,
and are usually created with a CAM system.
Example:
Circles and circular arcs
The TNC moves two axes simultaneously on a circular path relative to
the workpiece. You can define a circular movement by entering the
circle center CC.
When you program a circle, the control assigns it to one of the main
planes. This plane is defined automatically when you set the spindle
axis during a TOOL CALL:
Direction of rotation DR for circular movements
When a circular path has no tangential transition to another contour
element, enter the direction of rotation as follows:
Clockwise direction of rotation: DR-
Counterclockwise direction of rotation: DR+
Radius compensation
The radius compensation must be in the block in which you move to
the first contour element. You cannot activate radius compensation in
a circle block. Activate it beforehand in a straight-line block (see “Path
Contours—Cartesian Coordinates,” page 200)or approach block
(APPR block, see “Contour Approach and Departure,” page 192).
Pre-positioning
Before running a part program, always pre-position the tool to prevent
the possibility of damaging it or the workpiece.
L X+20 Y+10 Z+2 A+15 C+6 R0 F100 M3
X
Y
X
Y
CC
X
CC
Y
CC
Spindle axis
Main plane
Z
XY, also
UV, XV, UY
Y
ZX, also
WU, ZU, WX
X
YZ, also
VW, YW, VZ
You can program circles that do not lie parallel to a main
plane by using the function for tilting the working plane
(see User's Manual for Cycles, Cycle 19, WORKING
PLANE) or Q parameters (see “Principle and Overview,”
page 274).
CC
CC
DR
DR+
X
Z
Y