5 mac hining p a ra met ers – HEIDENHAIN CNC Pilot 4290 User Manual
Page 370
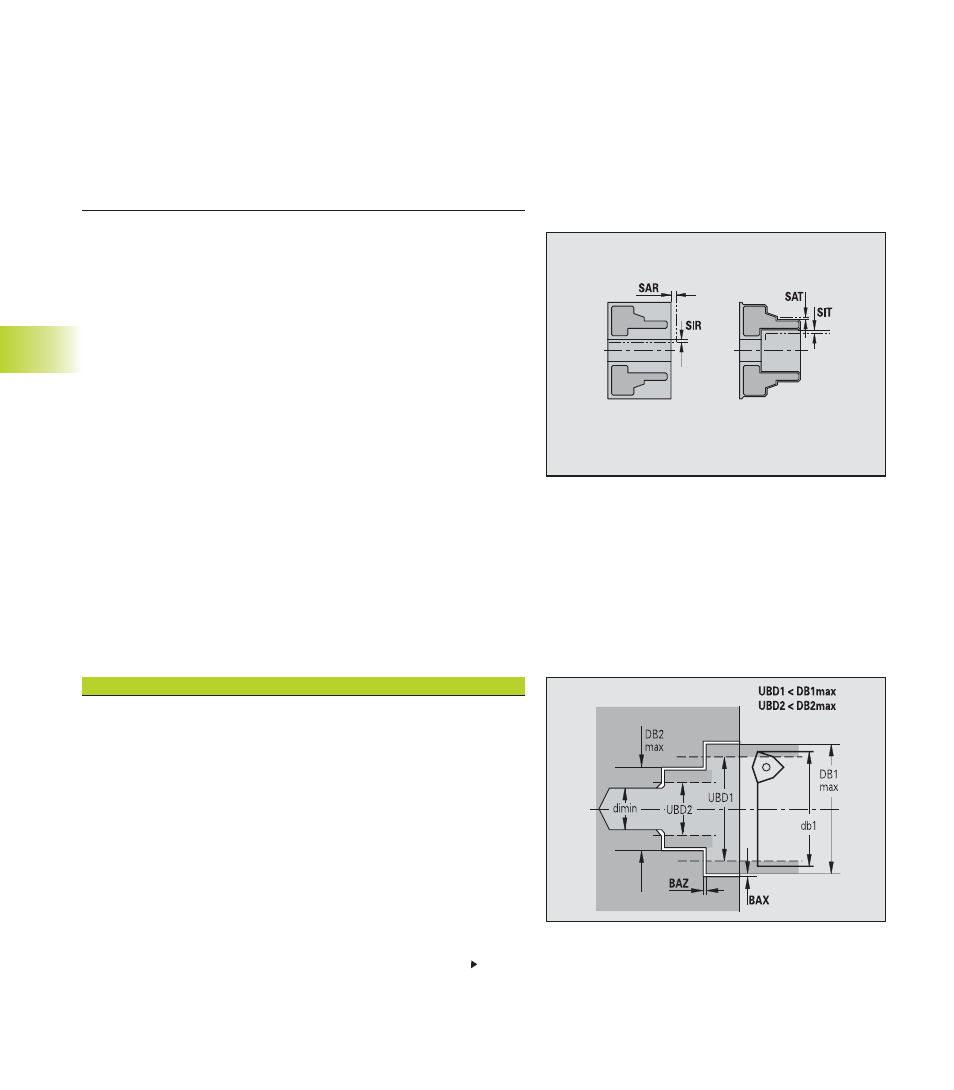
7 Parameters
358
7.5 Mac
hining P
a
ra
met
ers
Continued
AWG – Definition of approach mode: Respective machining
parameters;Tool change position: Defined tool change point
■
2: Moving to tool change position with G14.
■
3: Moving to a calculated change position with G0 – TURN PLUS
uses the current and subsequent tool to calculate the optimum
change position
■
Speed limitation [SMAX]: Global speed limitation – You can define
a lower speed limitation in the TURN PLUS program head (see
”
6.2.2 Program Head”).
Global safety clearance
■
External on blank [SAR] – Safety distance on the outside blank
■
Internal on blank [SIR] – Safety distance on the inside blank
■
External on machined part [SAT] – Safety distance on the outside
premachined workpiece contour
■
Internal on machined part [SIT] – Safety distance on the inside
premachined workpiece contour
TURN PLUS takes account of SAR/SIR for all rough-turning cycles
and for centric predrilling.
SAT/SIT on the premachined parts apply to:
■
Finish-machining
■
Recess turning
■
Contour recessing
■
Recessing
■
Thread cutting
■
Measuring
3 – Centric predrilling
Centric predrilling - tool selection, allowances
For predrilling, a maximum of three drilling steps is used:
■
1st predrilling step (diameter limit UBD1)
■
2nd drilling step (diameter limit UBD2)
■
Finish-drilling step
■
1st drilling diameter limit [UBD1]
■
1st predrilling step, where UBD1 < DB1max
■
Tool selection: UBD1 <= db1 <= DB1max
■
2nd drilling diameter limit [UBD2]
■
2nd predrilling step, where UBD2 < DB2max
■
Tool selection: UBD2 <= db2 <= DB2max
■
Finish drilling is performed with: dimin <= UBD2
■
Tool selection: db = dimin