12 special functions – HEIDENHAIN CNC Pilot 4290 User Manual
Page 176
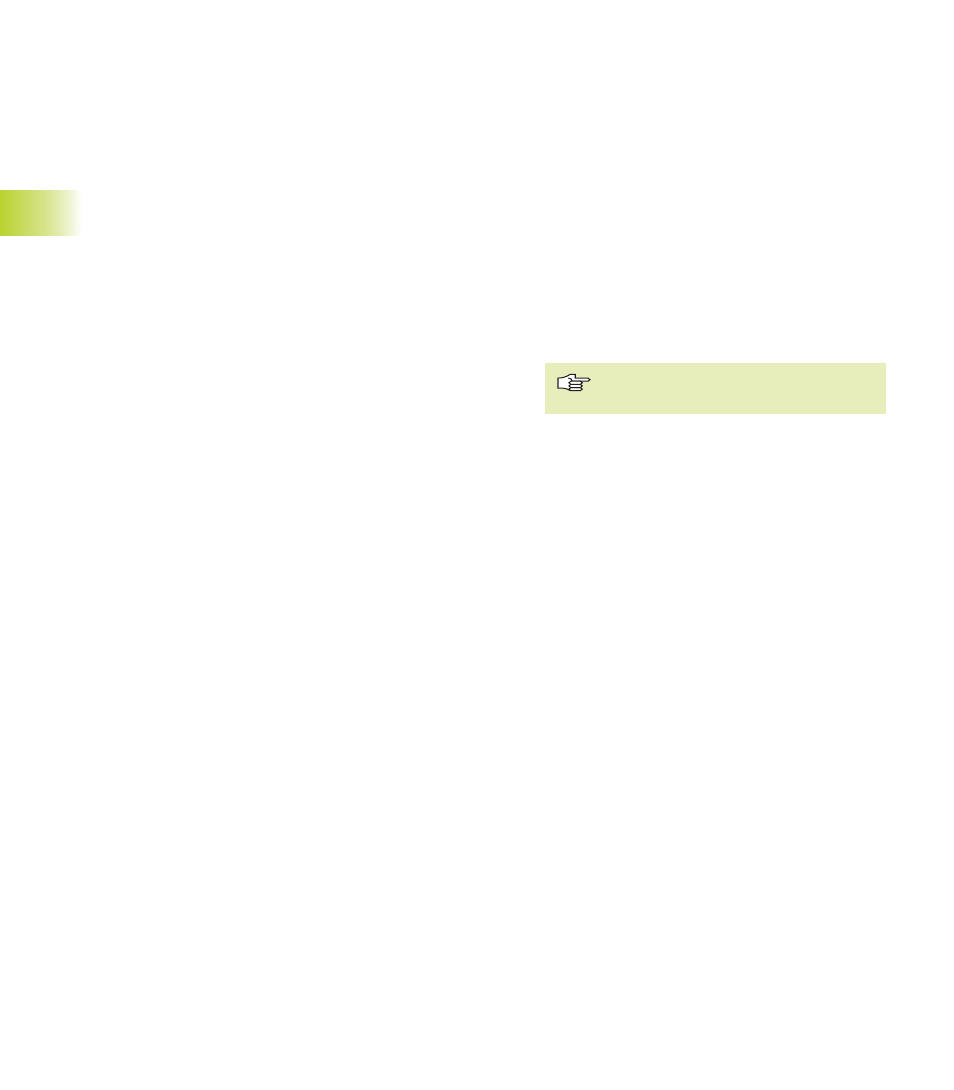
4 DIN PLUS
164
Values for controlled parting G992
G992 overwrites machine parameters 808, 858, ... for controlled
parting.
The new parameters are effective from the next NC block and are
retained until G992 is reprogrammed or the parameters are edited.
Parameters
S:
Speed difference (in revolutions per minute)
E:
Monitoring time (in ms)
4.12 Special Functions
4.12.4 Contour Follow-Up
The following G functions can be used to influence contour
regeneration (see section ”
4.10.2 Contour Repetitions”). Examples:
Program repeats (for the machining of bars), program branches, etc.
Storing/loading contour follow-up G702
Parameters
Q:
Loading/saving the contour
■
Q=0: Save – saves the current contour – no influence on the
contour follow-up
■
Q=1: Load – loads the saved contour – the contour follow-up
is resumed with the ”loaded contour”
Contour follow-up G703
With an IF, WHILE or SWITCH statement, the contour follow-up is
switched off. With ENDIF, ENDWHILE or ENDSWITCH it is switched
on again.
G703 switches the contour follow-up on for theTHEN, ELSE or CASE
branch.
Parameters
Q:
Contour regeneration On/Off
■
Q=0: Off
■
Q=1: On
K default branch G706
With IF or SWITCH statements with V variables, G706 defines the
”default branch.” The commands of the default branch are used for
updating the ”technology data” (tool, tool position, contour follow-up,
TRC, etc.). After the branch, the result of the ”default branch” goes
into effect. Without the default branch, the technology data remain
undefined after the branch.
Parameters
Q:
K branch
■
Q=0: No default branch defined;
■
Q=1: THEN branch as default branch
■
Q=2: ELSE branch as default branch
■
Q=3: Current branch as default branch
Program G702 for one slide only – usually,
for slide 1.
Programming notes:
Program:
■
G706 Q0, 1, 2: before the branch
■
G706 Q3: at the beginning of the THEN, ELSE or
CASE branches