2 mac hine p a ra met ers – HEIDENHAIN CNC Pilot 4290 User Manual
Page 356
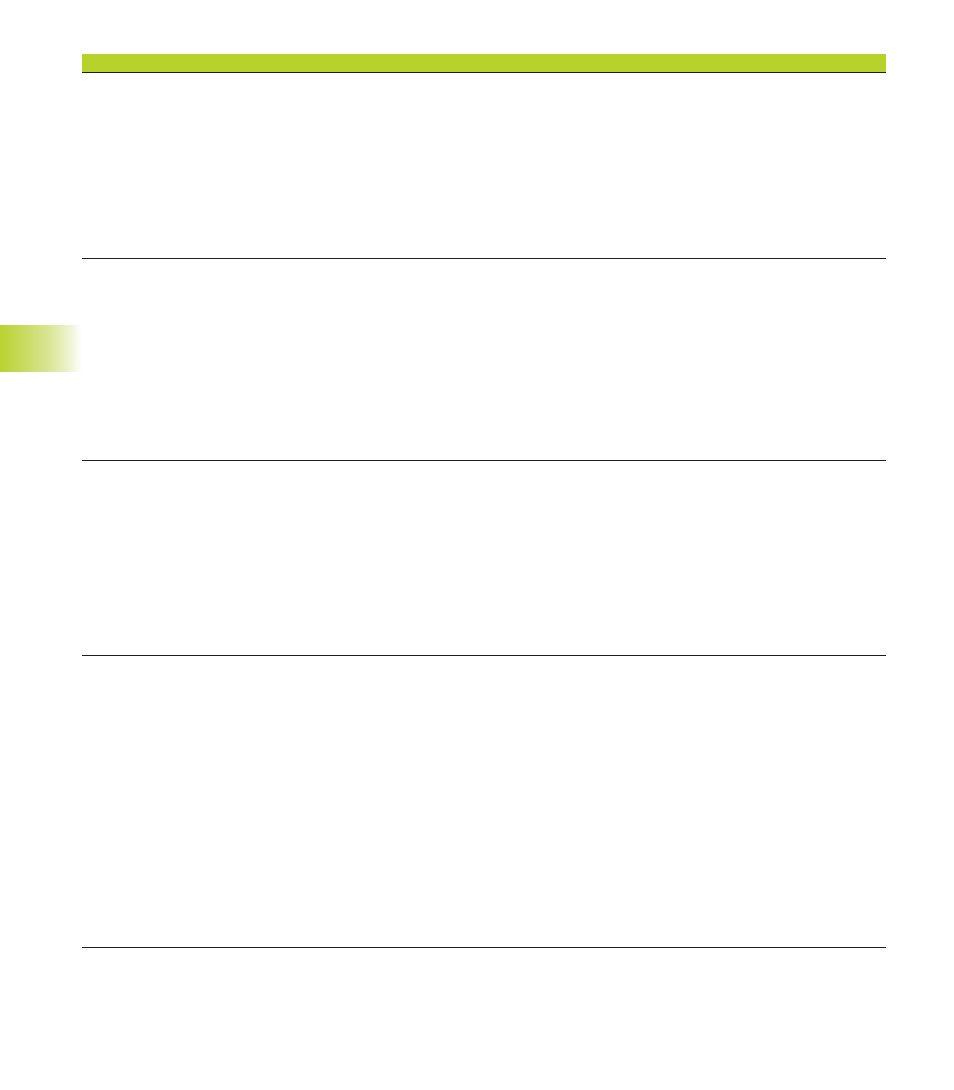
7 Parameters
344
7.2 Mac
hine P
a
ra
met
ers
Parameters for spindles (continued)
Status ”Synchronization reached”: If the actual speed difference and
the actual position difference between the spindles to be synchronized
lies within the tolerance range, the status is reached. When the status
”Synchronization reached” is attained, the torque of the guided spindle
is limited.
Note: The tolerances which are actually attainable on the machine must
not be undercut when setting these parameters. The value
programmed here must be set to a value greater than the sum of the
maximum differences in the speeds of the guiding and guided spindles
(approx. 5 to 10 rpm).
807, 857, ... Angular offset measuring (G906),
spindles
Evaluation: G906 Measuring angular offset during spindle
synchronization
■
Maximum permissible change in position: Tolerance window for the
change of position offset after the spindles have gripped the workpiece
at both ends during synchronized operation. If the offset change
exceeds the maximum value, an error message appears.
A normal fluctuation of approx. 0.5° must be taken into account.
■
Waiting time, measuring offset: Measuring period (duration)
808, 858, ... Cut-off control (G991), spindle
After the parting operation has been completed, the
phase angle of the two synchronized spindles
changes without the nominal values (speed/angle of
rotation) being changed. If the speed difference is
exceeded during the monitoring time, the workpiece
is considered as being cut off.
Evaluation: G991 Controlled parting using spindle monitoring
■
Speed difference
■
Monitoring time
809, 859, ... Load monitoring, spindles
Evaluation: Load monitoring
■
Start-up time for monitoring [0..1000 ms] – (only evaluated if ”Omit
paths of rapid traverse” is active) The load monitoring function is not
activated if the nominal acceleration of the spindle exceeds the limit
value (limit value = 15% of acceleration ramp / brake ramp). As soon
as nominal acceleration falls below the limit value, the monitoring
function is activated after the start-up time for monitoring has elapsed.
■
Number of measured values to be averaged [1..50]: The mean value
is calculated from the number of values to be averaged. This reduces
the sensitivity to short-term peak load during monitoring.
■
Reaction delay time P1, P2 [0..1000 ms]
The system reports a limit violation as soon as the delay time for P1 or
P2 (limit torque 1 or 2) has been exceeded.
■
Maximum torque – not used at present