7 t u rning cy cles – HEIDENHAIN CNC Pilot 4290 User Manual
Page 150
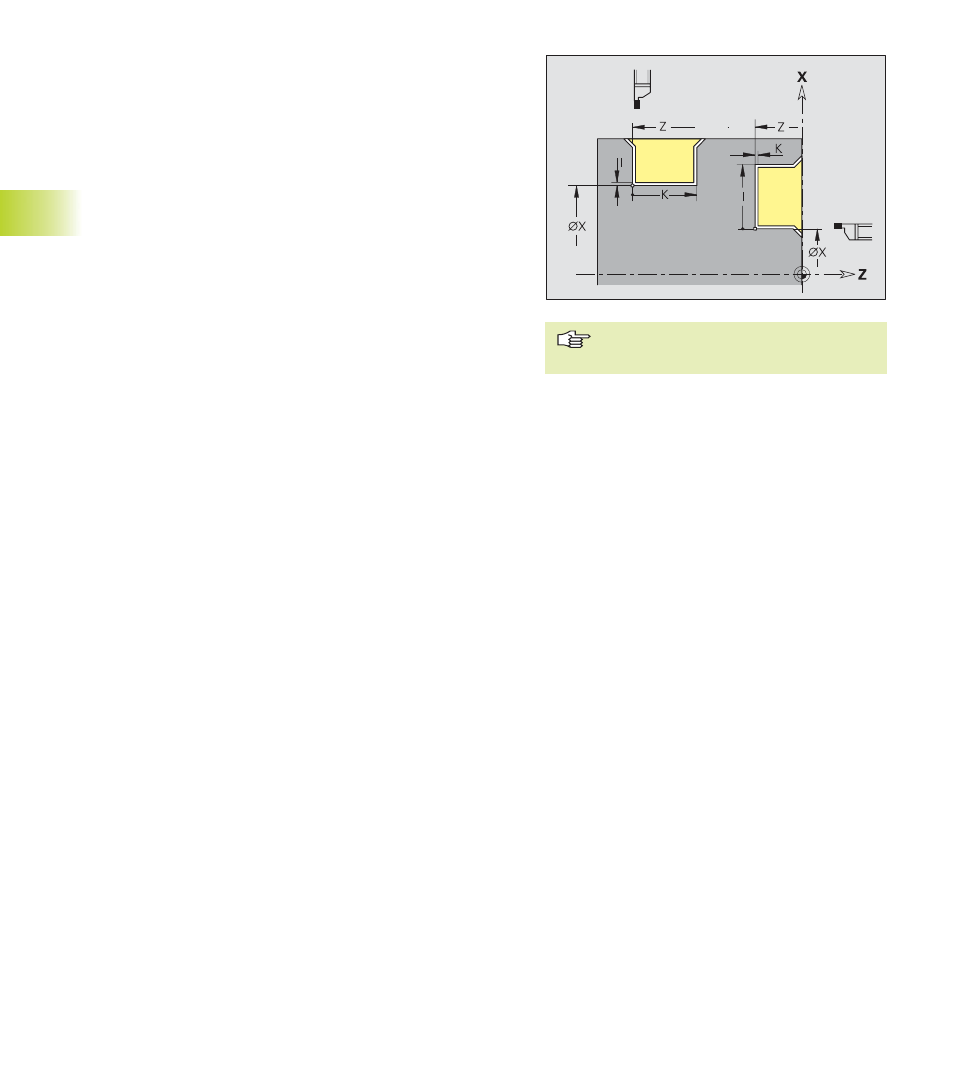
4 DIN PLUS
138
Recessing G86
G86 machines simple radial and axial recesses with chamfers. From
the tool position the CNC PILOT calculates a radial/axial or an inside/
outside recess.
”Oversize K” programmed: First pre-recessing, then finish recessing
(finishing)
G86 machines chamfers at the sides of the recess. If you do not wish
to cut the chamfers, you must position the tool at a sufficient distance
from the workpiece. Calculate the starting position XS (diameter) as
follows:
XS = XK + 2 * (1,3 – b)
XK:
Contour diameter
b:
Chamfer breadth
Cycle run
1 Calculate the cutting segmentation – maximum offset: SBF *
cutting width (For SBF, see machining parameter 6).
2 Approach to clearance height at rapid traverse on paraxial path.
3 Execute the first cut - taking finishing allowance into account.
4 Without finishing allowance: ”E” period of dwell.
5 Retract and approach for next pass.
6 Repeat 2 to 4 until the complete recess has been machined.
7 With finishing allowance: Finish-machine the recess.
8 Return to starting point at rapid traverse.
Parameters
X, Z: Target point (X diameter)
Radial recess:
I:
Allowance
■
I>0: Allowance (roughing and finishing)
■
I=0: No finishing
K:
Recess width – no input: a single cut is machined (recess width
= tool width)
Axial recess:
I:
Recess width – no input: a single cut is machined (recess width
= tool width)
K:
Allowance
■
K>0: Allowance (roughing and finishing)
■
K=0: No finishing
E
Period of dwell (for chip breaking) – default: Length of time for
one revolution
■
With finishing allowance: Only during finishing
■
Without finishing allowance: For each recess
■
Cutter radius compensation: Active.
■
Allowances are not calculated.
4.7 T
u
rning Cy
cles