12 special functions – HEIDENHAIN CNC Pilot 4290 User Manual
Page 173
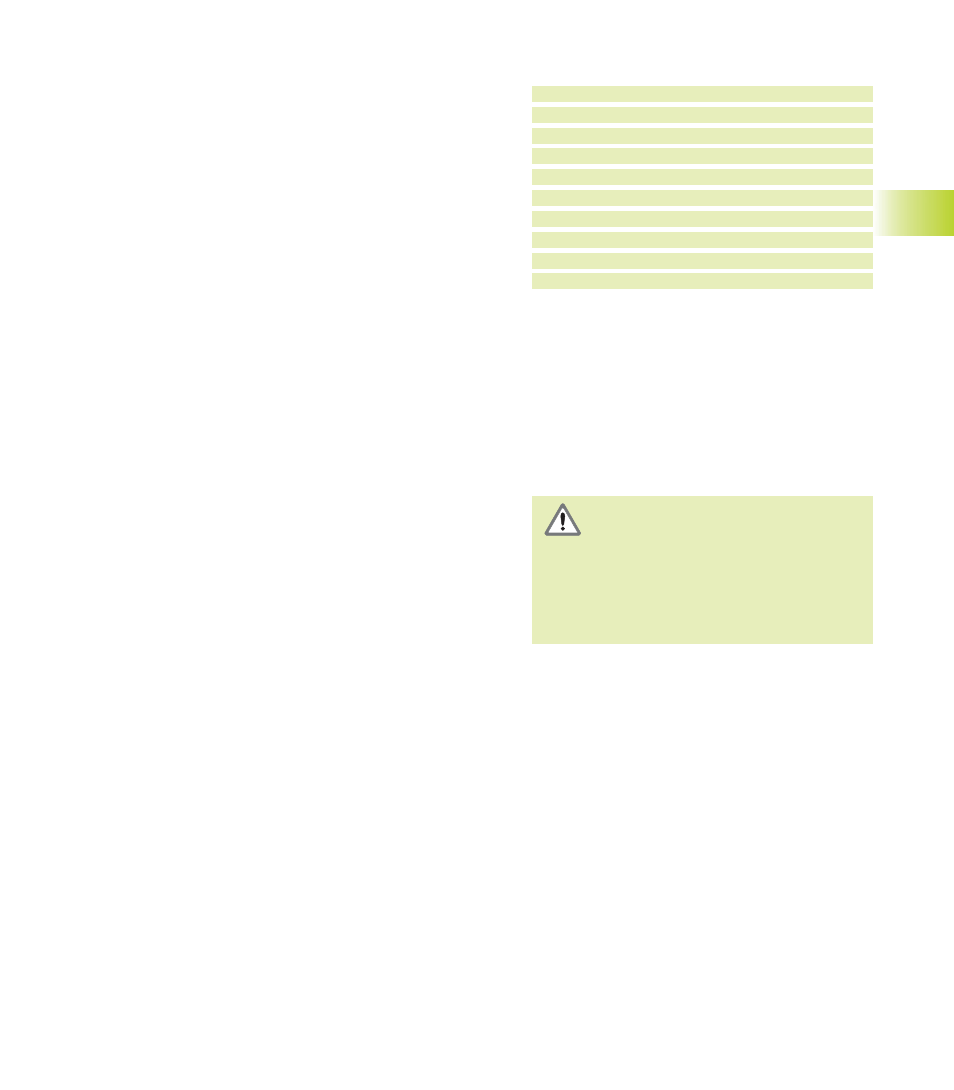
HEIDENHAIN CNC PILOT 4290
161
Example: G720
. . .
N.. G397 S1500 M3 [speed and direction
of master spindle]
N.. G720 C180 S4 H2 Q2 F–1 [synchronization
of master spindle to slave spindle. The slave
spindle precedes the master spindle
by 180°. Slave spindle: Direction of rotation M4;
speed 750]
. . .
4.12.3 Spindle Synchronization, WorkpieceTransfer
Spindle synchronization G720
G720 controls the workpiece transfer from the master to the slave
spindle and synchronizes functions such as polygonal turning jobs.
Program the speed of the master spindle with Gx97 S.. and define
the speed ratio between the master spindle and the slave spindle
with ”Q, F.” If you enter a negative value for Q or F, the direction of
rotation of the slave spindle will be reversed. If you synchronize
more than one slave spindle with a master spindle, use G720 for
each of the slave spindles.
The following rule applies: Q * master speed = F * slave speed
Parameters
S:
Number of the master spindle [1..4]
H:
Number of the slave spindle [1..4] – no input or H=0: Switches
off the spindle synchronization
C:
Offset angle [°] – default: 0°
Q:
Master speed factor – default: 1;
Range: –100 <= Q <= 100
F:
Slave speed factor – default: Q is transferred;
range: –100 <= F <= 100
C-angle offset G905
G905 measures the ”angular offset” of workpiece transfer with
rotating spindle. The sum of angle C and the angle offset goes into
effect as ”zero point shift of C axis.” This value is saved in the
variable V922 (C axis 1) or V923 (C axis 2).
The zero offset stays in effect until another NC program is activated.
Parameters
Q:
Number of the C axis
C:
Angle of additional zero point shift for offset gripping – range: –
360° <= C <= 360°; default: 0°
Measuring angular offset during spindle
synchronization G906
G906 writes the angular offset between the master spindle and the
slave spindle into variable V921.
Programming notes:
■
Program G906 only for active angular synchronization – both chucks
must be closed.
■
Program G906 in a separate NC block.
■
Program G909 (interpreter stop) before processing variable V921.
■
G906 generates an ”interpreter stop.”
Danger of collision!
■
For narrow workpieces the jaws have to
grip at an offset.
■
The ”zero point shift of C axis” is
retained:
– When changing from Automatic to
Manual mode
– After switch-off
4.12 Special Functions