7 t u rning cy cles – HEIDENHAIN CNC Pilot 4290 User Manual
Page 136
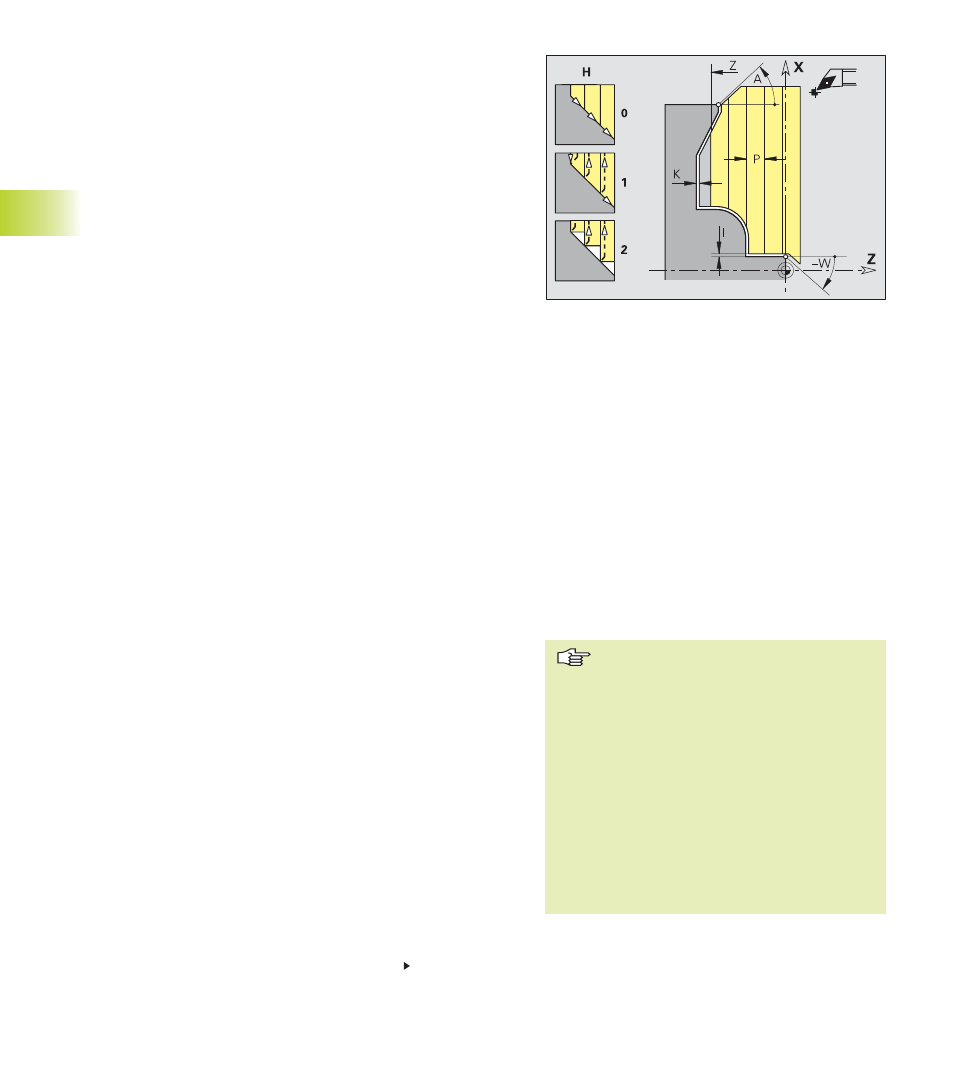
4 DIN PLUS
124
4.7 T
u
rning Cy
cles
Continued
Face roughing G820
G820 machines the contour area defined by “NS, NE.” The CNC
PILOT uses the tool definition to distinguish between external and
internal machining. With “NS – NE” you specify the machining
direction.
If the contour to be machined consists of one element, then:
■
If you program only NS, machining is in contour definition
direction
■
If you program NS and NE, machining is against the contour
definition direction
If required, the area to be machined is divided into several sections,
for example, for machining contour valleys.
The simplest way of programming is specifying NS, NE and P.
Parameters
NS:
Starting block number (beginning of contour section)
NE:
End block number (end of contour section)
P:
Maximum infeed
I:
Oversize in X direction (diameter value)—default: 0
K:
Oversize in Z direction—default: 0
E:
Approach behavior
■
E=0: Descending contours are not machined
■
E>0: Approach behavior
■
No input: Feed rate reduced depending on approach
angle—maximum reduction: 50%
X:
Cutting limit in X direction (diameter value)—default: no
cutting limit
Z:
Cutting limit in Z direction—default: no cutting limit
H:
Type of contour smoothing—default:
■
H=0: smoothing after each cut
■
H=1: lift off at under 45°, smoothing after last cut
■
H=2: lift off at under 45°, no smoothing
A:
Approaching angle (reference: Z axis)—default: 90°/270°
(perpendicular to Z-axis)
W:
Departing angle (reference: Z axis)—default: 0°/180° (parallel
to Z-axis)
Q:
Type of retraction after machining—default: 0
■
Q=0: Return to starting point (first in X direction, then in Z)
■
Q=1: Position in front of finished contour
■
Q=2: Move to clearance height and stop
V:
Identifier beginning/end—default: 0
A chamfer/rounding arc is being machined:
■
V=0: At beginning and end
■
V=1: At beginning
■
V=2: At end
Cycle run
1 Calculate the areas to be machined and the
cutting segmentation (infeeds).
2 Approach workpiece for first pass from starting
point, taking the safety clearance into account
(first in X direction, then in Z).
3 Move at feed rate to target point X.
4 Depending on H:
■
H=0: Cut along the contour
■
H=1 or 2: Retract at 45°
5 Return at rapid and approach for next pass.
6 Repeat 3 to 5 until target point Z has been
reached.
7 If required, repeat 2 to 6 until all areas have been
machined.
8 H=1: Smoothen contour.
9 Retract according to “Q.”
Cutting limitation: The tool position
before the cycle call determines the
effect of a cutting limit. The CNC PILOT
machines the area to the right or to the
left of the cutting limit, depending on
which side the tool has been positioned
before the cycle is called.
Cutter radius compensation: Active
G57 oversize: “Enlarges” the contour
(also inside contours)
G58 oversize:
■
>0: “enlarges” the contour
■
<0: is not considered
G57/G58 oversizes are deleted after
cycle end