2 mac hine p a ra met ers – HEIDENHAIN CNC Pilot 4290 User Manual
Page 357
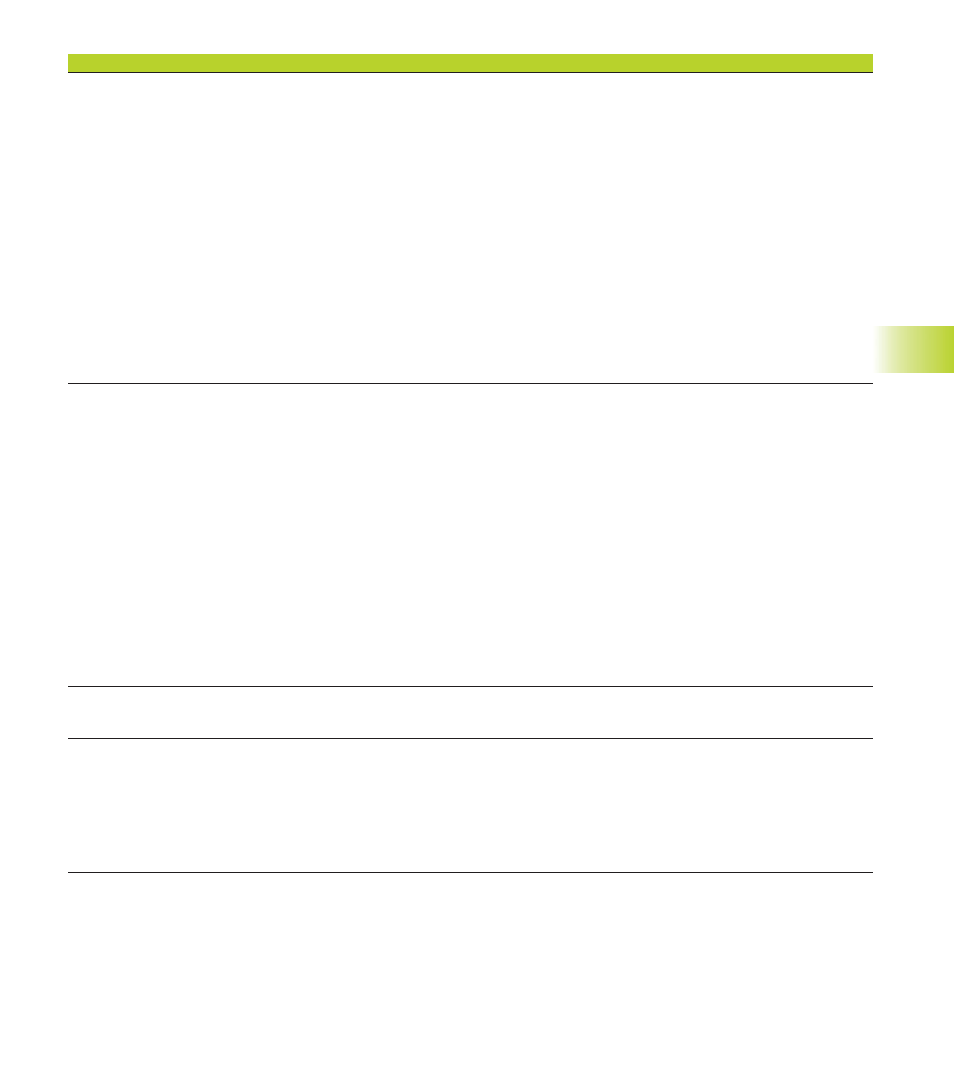
HEIDENHAIN CNC PILOT 4290
345
7.2 Mac
hine P
a
ra
met
ers
Parameters for C axes
1007, 1057 Backlash compensation, C axis
In backlash compensation the “value of backlash
compensation“ is calculated into every change in
direction.
■
Type of backlash compensation
■
0: No backlash compensation
■
1: Encoder is built into the motor. The backlash compensation
accounts for the reversal error between the motor and table. During
each change in direction, the nominal value is adjusted by the value
entered in the “backlash compensation value“ option.
■
2: With direct measurement, the backlash compensation
compensates the reversal error between the motor and encoder.
During each change in direction, the nominal value is corrected by
the value entered in the “Backlash compensation value“ option.
■
Backlash compensation value:
■
For type=1: compensation value with positive sign
■
For type=2: compensation value with negative sign
1010, 1060 Load monitoring, C axis
Evaluation: Load monitoring
■
Start-up time for monitoring [0 to 1000 ms]—(evaluated if “Omit
paths of rapid traverse” is active): The load monitoring function is not
activated if the nominal acceleration of the spindle exceeds the limit
value (limit value = 15% of acceleration ramp / brake ramp). As soon
as nominal acceleration falls below the limit value, the monitoring
function is activated after the start-up time for monitoring has
elapsed.
■
Number of measured values to be averaged [1 to 50]: The mean
value is calculated from the number of values to be averaged. This
reduces the sensitivity to short-term peak load during monitoring.
■
Maximum torque—not used at present
■
Reaction delay time P1, P2 [0 to1000 ms]
The system reports a limit violation as soon as the delay time for P1
or P2 (limit torque 1 or 2) has been exceeded.
1016, 1066 Limit switches and rapid traverse rates, C axis
■
Rapid traverse rate, C axis: Maximum speed for spindle positioning
1019, 1069 General data, C axis
This parameter is evaluated if “pre-positioning“ is
switched on (“configuration code 1“—machine
parameter 18). For digital drives, pre-positioning is
usually not necessary.
■
Pre-positioning of spindle with M14: Angle at which the spindle is
positioned before the C axis is swiveled in.