Fluke Biomedical VT Plus HF User Manual
Page 129
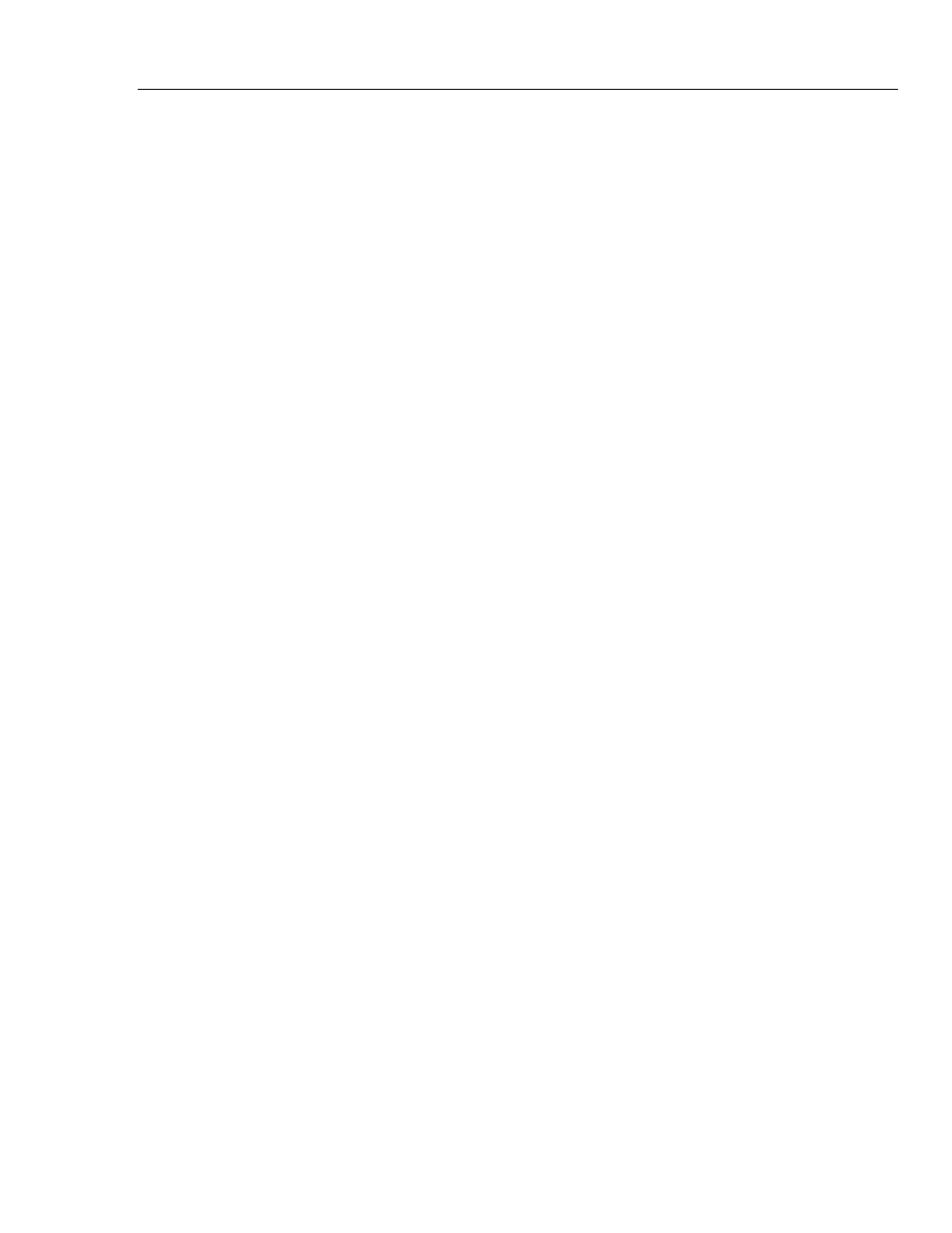
Appendices
Gas Analyzer Tutorial
A
A-3
Oxygen Measurements
Oxygen measurement is performed using a galvanic oxygen cell on the high-flow port
near the exhaust. The Analyzer interprets the measurement from the oxygen sensor as a
partial pressure of the total pressure in the high-flow circuit. The total pressure is the
airway pressure plus the barometric pressure.
The oxygen percentage is calculated as the fraction of the partial pressure of oxygen
relative to the total pressure. It should be noted that changes in the total pressure (airway
pressure) result in a change in the partial pressure of the measured oxygen even though
the percentage of oxygen is the same. Because the pressure can change much faster than
the response time of the oxygen sensor, a small transient (1 to 2 % of full-scale) error can
occur in the oxygen measurement when there is a fast change in the pressure at the
oxygen sensor.
Whenever an oxygen measurement is made, or when the oxygen sensor is calibrated or
zeroed, there should be sufficient gas flow past the oxygen sensor. Only a small flow of
gas (say, 10 LPM) is needed to ensure that the oxygen concentration at the oxygen sensor
is as expected. For example, just opening the high-flow exhaust to room air does not
ensure that the oxygen sensor detects 20.9 % oxygen. The oxygen concentration at the
sensor does not equilibrate with the room air unless a small amount of flow is present to
ensure gas mixing.
The oxygen sensor should last for more than one year, and is replaced during an annual
calibration of the unit. Sensor life is shortened, the longer the sensor is exposed to
oxygen. This includes oxygen in room air as well as higher flow rates of oxygen-
containing gases past the sensor. The Analyzer checks to detect if the oxygen sensor is
depleted every time an oxygen zero is performed.
The oxygen sensor should be recalibrated by the user with 100 % oxygen and dry air at
the beginning of any testing day in which oxygen concentrations are to be measured.
Flow Measurements
The flow measurements in the Analyzer are made by measuring the differential pressure
across a resistive screen mesh. The resulting differential pressure is nearly linear with
respect to the volumetric flow. Simple corrections are applied to correct for any
nonlinearities. A table of correction factors is applied for each the low- and high-flow
sensors. The information regarding these tables can be seen using the
Setup > Utilites
> Linearization
screen on the Analyzer.
Gas Settings
The flow measurement sensors in the Analyzer are linearly dependent on the viscosity of
the applied gas. The Analyzer setup options allow the user to specify what type of gas is
being used. Additional choices are available using the User Define mode. The user
defined gas settings are set using the PC software. The gas calculator on the PC software
can determine the effective viscosity for a combination of various gases.
The Analyzer calculates the temperature dependent viscosity for the gas type selected
(except for user-defined gases). Therefore, when a new flowing gas temperature is
entered by the user, the Analyzer calculates the new viscosity. For air, the sensitivity to
temperature is about 0.25 % of reading per °C.
The Analyzer viscosity calculation for the gas settings assumes that dry gas is being used.
Increased water vapor content can slightly affect the flow accuracy. At room temperature,
a flow measurement error of -0.5 % of reading can occur if the relative humidity of the
flowing gas is 50 %.