3 calibration – Flowserve 3400IQ Digital Positioner User Manual
Page 98
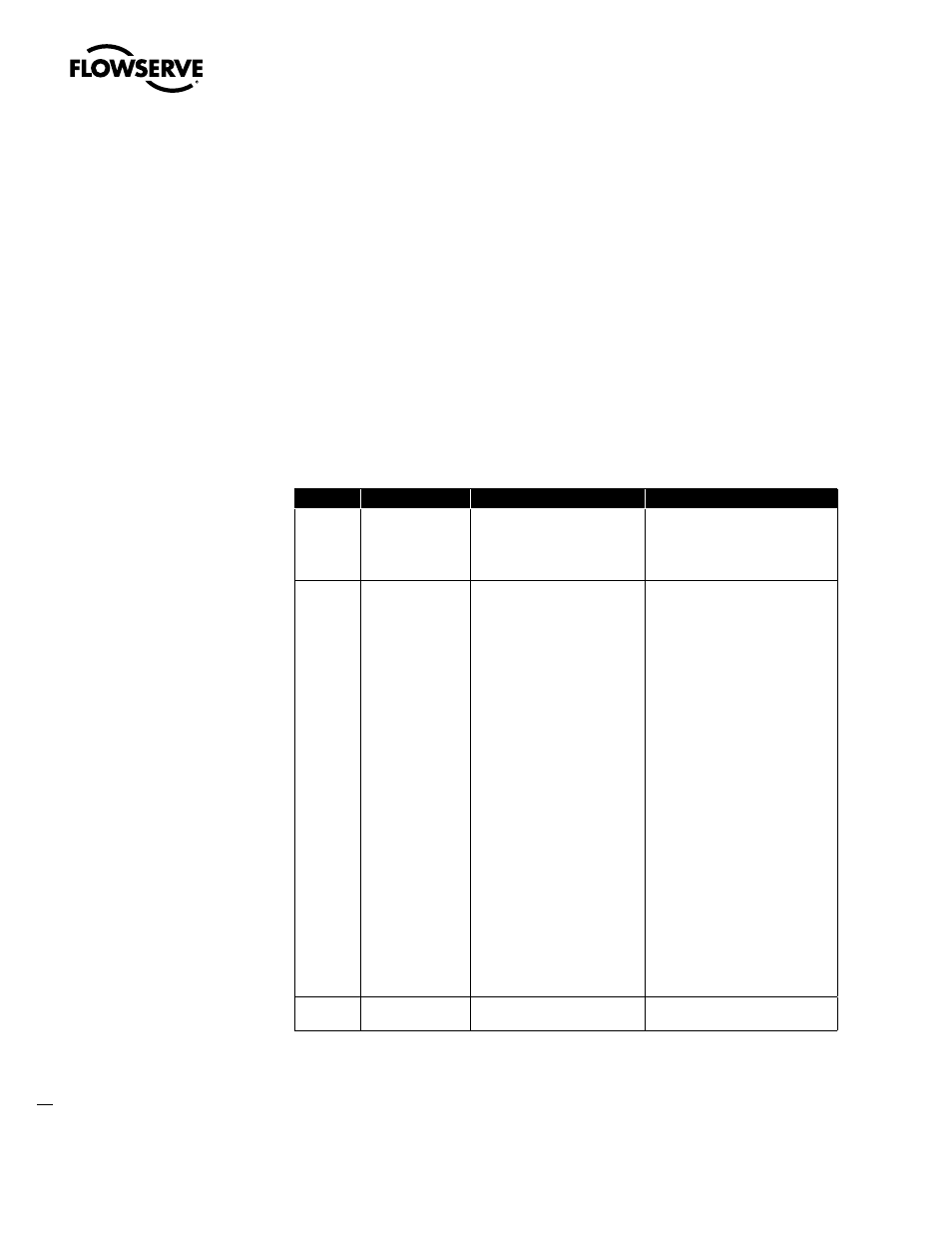
Logix 3400IQ Digital Positioner FCD LGENIM3402-00 – 0/07
3. Press and hold the Re-Cal button for at least five seconds to initiate the stroke calibration. (NOTE:
The transducer block must be out-of-service before the Re-Cal button will be active.) If Auto Tune
is selected, this will also auto tune the positioner response.
4. Replace cover and return to operation. (Refer to Logix 3400IQ Digital Positioner IOM for more
details.)
9.3 Calibration
The output position of the Logix 3400IQ digital positioner is calibrated using the transducer block
CALIBRATE parameter. The positioner performance must be verified by the operator.
Calibration Parameters
Table 9.1 lists transducer block parameters and their values used in the calibration procedures.
Table 9.1 Transducer Block Calibration Parameters
Two-point Calibration
The Logix 3400IQ digital positioner has two-point calibration. The stroke position feedback poten-
tiometer and the actuator pressure transducers are calibrated this way. The positioner must be
pre-configured to the proper air action, valve type (linear or rotary), positioner model (standard or
advanced) before the calibration is done. (CONTROL_FLAGS =16 -> Air to Open, Linear, Advanced =
default values)
Parameter
Description
Value - Meaning
Comments
MODE_BLK The operating mode of
the transducer block
Permitted modes:
The transducer block must be in the OOS
mode to perform Logix 3400IQ digital
positioner calibration.
Auto — Auto (target mode)
OOS — Out of Service
CALIBRATE
One-byte value which
selects the calibration
operation to be per-
formed.
0 Normal operation. Valve tracks Calibration and correction commands are
executed when the command is written.
FINAL_VALUE
1 Initiates stroke calibration. Closes
valve.
2 Initiates actuator pressure
transducers calibration.
3 Moving valve to closed position
Messages only
4 Moving valve to open position
5 Calibrating Supply
6 Calibrating actuator sensor
- closed
7 Calibrating actuator sensor - open
8 Monitoring of Re-Cal button.
9 Error occurred during calibration
10 Inner-loop offset adjustment
Nulls the spool block
11 Auto Tune Positioner
Only active when Re-Cal is done
12 JogCal - Waiting for user to set point
Initiates the monitoring of the button for
five seconds
13 Range Checking
14 Normal Operation (Rev 0x23).
Checkjog call setting in
MISC_FLAGS
Jog Cal must be enabled in MISC_FLAGS
before it can be initiated
PRES_CAL
Input supply pressure
for calibration
0 – 150 psig max.
Used to calibrate the span of the actuator
pressure sensors