Flowserve 3400IQ Digital Positioner User Manual
Page 82
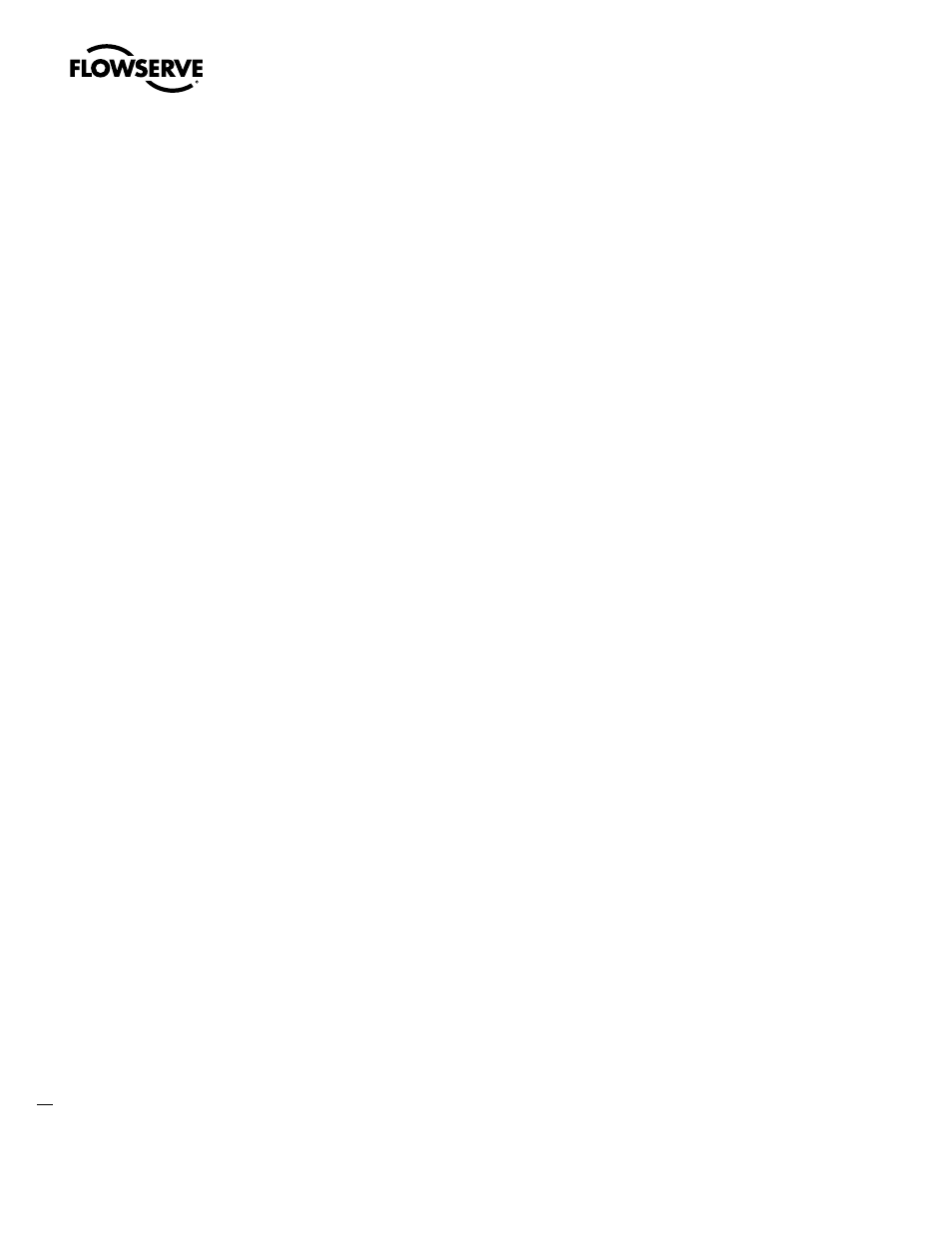
Logix 3400IQ Digital Positioner FCD LGENIM3402-00 – 0/07
2
Top Sensor, Bottom Sensor Each sensor is checked during actuator calibration. If a calibration
reading appears to be out of range, the appropriate alarm will become active. The pressure sensors
are located on the collector board assembly.
Internal Positioner Alerts
MPC (FINAL_VALUE_CUTOFF_HI, FINAL_VALUE_CUTOFF_LO) The MPC or tight shutoff feature of
the Logix 3400IQ digital positioner allows the user to control the level at which the command signal
causes full actuator saturation in the closed (or open) position. This feature can be used to guarantee
actuator saturation in the closed (or open) position or prevent throttling around the seat at small
command signal levels. To enable, use configuration to apply the desired MPC threshold. Note: The
positioner automatically adds a 1 percent hysteresis value to the MPC setting to prevent jumping in
and out of saturation when the command is close to the MPC setting.
Question: I set the FINAL_VALUE_CUTOFF_LO at 5 percent. How will the positioner operate?
Answer: Assume that the present command signal is at 50 percent. If the command signal is
decreased, the positioner will follow the command until it reaches 5 percent. At 5 percent, the spool
will be driven in order to provide full actuator saturation. The positioner will maintain full satura-
tion below 5 percent command signal. Now, as the command increases, the positioner will remain
saturated until the command reaches 6 percent (remember the 1 percent hysteresis value added by
the positioner). At this point, the stem position will follow the command signal.
Question: I have FINAL_VALUE_CUTOFF_LO set to 3 percent but the valve will not go below 10 percent?
Answer: Is a lower soft limit enabled? The lower soft limit must be less than or equal to 0 percent
in order for the MPC to become active. If soft stops are active(SOFTSTOP_LOW>30, SOFTSTOP_
HIGH<100) FINAL_VALUE_HI or _LO is disabled.
Position Alerts
Position alerts notify the user that the valve has traveled past a configured limit. The default settings
are –10 percent and 110 percent which are outside normal travel and, therefore, disabled. Position
alerts only notify the user that a limit has been exceeded and do not limit stem movement. Position
alerts will cause a green LED code to blink.
Soft Limits
Unlike position alerts, soft limits (SOFTSTOP_LOW, SOFTSTOP_HIGH) prevent the stem position
from going below or above the configured limits. If the command signal is trying to drive the position
past one of the limits, the green LED code will blink, but the stem position will remain at the set limit.
Travel Accumulator
The travel accumulator is equivalent to a car odometer and sums the total valve movement. Using the
user-defined stroke length and travel dead band, the Logix 3400IQ digital positioner keeps a running
total of valve movement. When the positioner first powers up, high and low dead band limits are
calculated around the present position. When the stem position exceeds the travel dead band, the
movement from the center of the dead band region to the new position is calculated and added to the
travel accumulator. From this new position, dead band high and low limits are again calculated.
Example: The Logix 3400IQ digital positioner has a default dead band configuration of 20 percent
and the valve has a 4- inch linear stroke. When the valve first powers up, the command signal is 50
percent. The unit will calculate a high-travel threshold of 70 percent (50 percent present position plus
20 percent dead band) and a low-travel threshold of 30 percent (50 percent present position minus
20 percent dead band). As long as the stem position remains greater than 30 percent and less than
70 percent, no additions are made to the travel accumulator. Now, assume the stem position moves
to 80 percent, which is outside the present dead band. The Logix 3400IQ digital positioner calculates
the stem movement and adds this number to the travel accumulator.