Flowserve 3400IQ Digital Positioner User Manual
Page 52
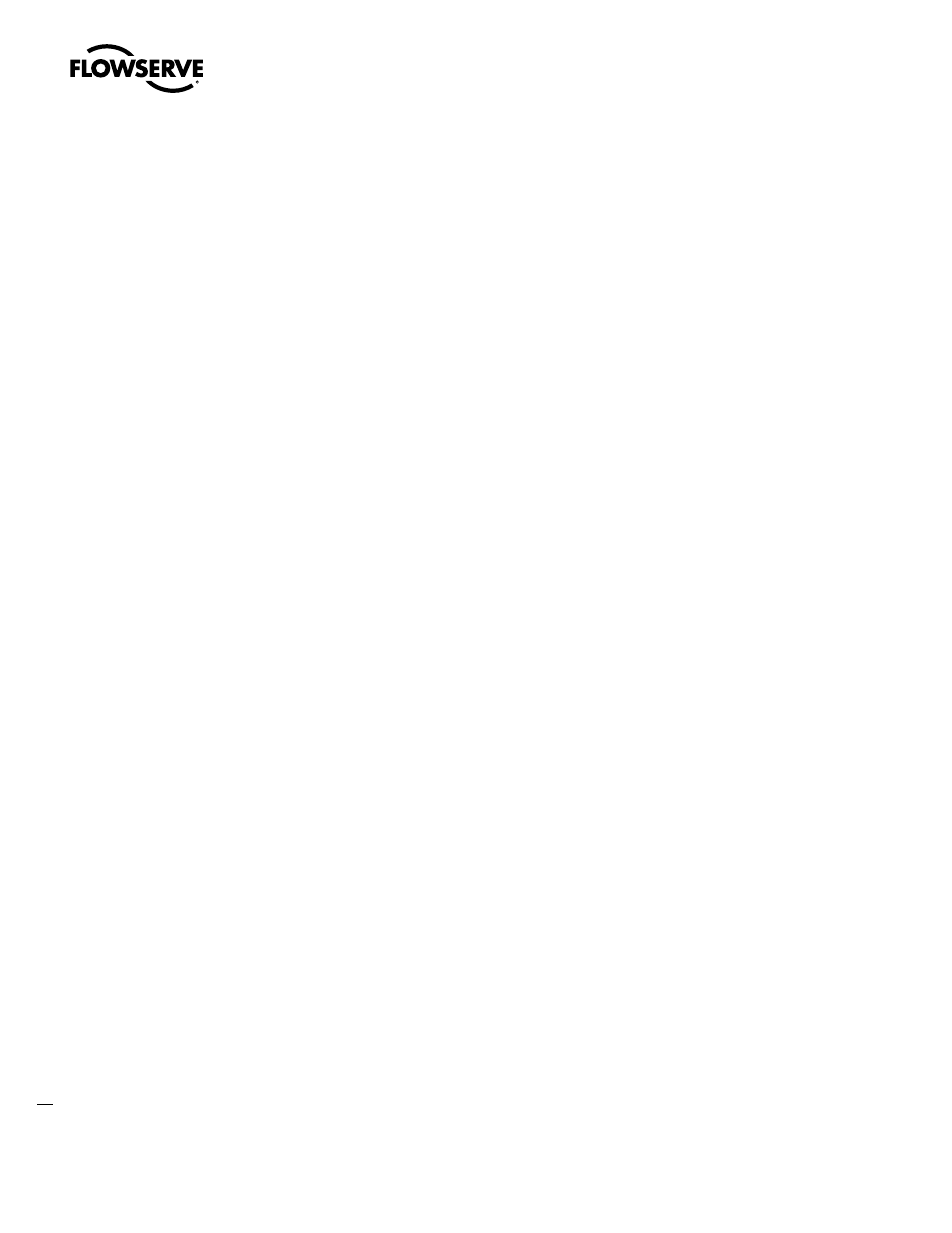
Logix 3400IQ Digital Positioner FCD LGENIM3402-00 – 0/07
2
CYCLE_COUNTER This parameter counts the number of cycles that have occurred.
CYCLE_DEADBAND In order for a cycle to be counted it must be greater than the value in this field.
CYCLE_LIMIT If CYCLE_COUNTER exceeds this value, the LED lights will start to blink Green,
Green, Red, Green and a warning will be generated in TRAVEL_FLAGS.
TRAVEL_ENG Total distance the valve stem has traveled.
TRAVEL_DEADBAND Amount in percent of stroke the valve must move in order for the movement
to be added to TRAVEL_ENG.
TRAVEL_ALERT If TRAVEL_ENG exceeds this value, the LED lights will start to blink Green, Green,
Red, Yellow and a warning will be generated in TRAVEL_FLAGS.
STROKE_ENG Stoke length of valve. This value is used to calculate TRAVEL_ENG.
TRAVEL_UNITS Units of measure used to calculate TRAVEL_ENG.
PRESS_UNITS Units of measure that pressure sensor readings are expressed in.
TEMP_UNITS Units of measure that temperature is expressed in.
FAIL_MODE Should a loss of communications occur between the fieldbus card and positioner card
this parameter sets the fail mode of the valve. Nothing selected will cause the positioner to hold the
last known command should a loss of communications occurs.
STROKE_TIME_OPEN: Allows the user to limit the stroking speed of the positioner. Input the
number of seconds for the desired opening stroke speed. Disable this feature by writing 0 to the
variable.
STROKE_TIME_CLOSE: Allows the user to limit the stroking speed of the positioner. Input the
number of seconds for the desired closing stroke speed. Disable this feature by writing 0 to the
variable.
Note: The stroke limiting feature could be used to make a valve very responsive to small steps. By
increasing the nominal gain values, and limiting the stroke speed, small steps would be subject to
very high gains. When active, the algorithm scales back large step sizes, thus limiting the undesired
effects large gains normally demonstrate on large step sizes, such as overshoot.
CAL_FULLSCALE: This variable allows the user to determine the minimum amount of movement
(A/D counts) required to prevent a calibration error. To use this feature, first make sure the positioner
is configured as a rotary valve in CONTROL_FLAGS. With the air removed from the positoner,
carefully loosen the follower farm on the back of the positioner, or the potentiometer screws inside
the positioner so that it can be rotated. Move the arm, or rotate the pot, until just barely in range - the
LED code that is blinking will change. Set ‚Auto Feedback Gain Enabled‘ in MISC_FLAGS. Re-start
the calibration. This time calibration should complete with out any problems. Refer to the Logix
3400IQ IOM for more details on this adjustment.
AUTO_TUNE_MULT: The positioner gains can be set automatically during a stroke calibration.
Adjustments to the auto gain settings can be adjusted by using this variable.
NVRAM_WRITE_CYCLES: This is a diagnostic parameter that allows the user to monitor the number
of times the NVRAM is written to. This can be a useful diagnostic tool for checking if the host system
is writing to the Fieldbus board memory too often. This is often a configuration error in the host
system setup. Excessive write cycles can cause configuration upsets and possible communications
slowdowns and errors. It also will shorten the operational life of a Fieldbus device by exceeding the
finite number of write cycles NVRAM chips can be used reliably to. These devices typically have a