0 electrical and wiring, 1 general, 2 supply wiring – Reznor YDSA Unit Installation Manual User Manual
Page 23
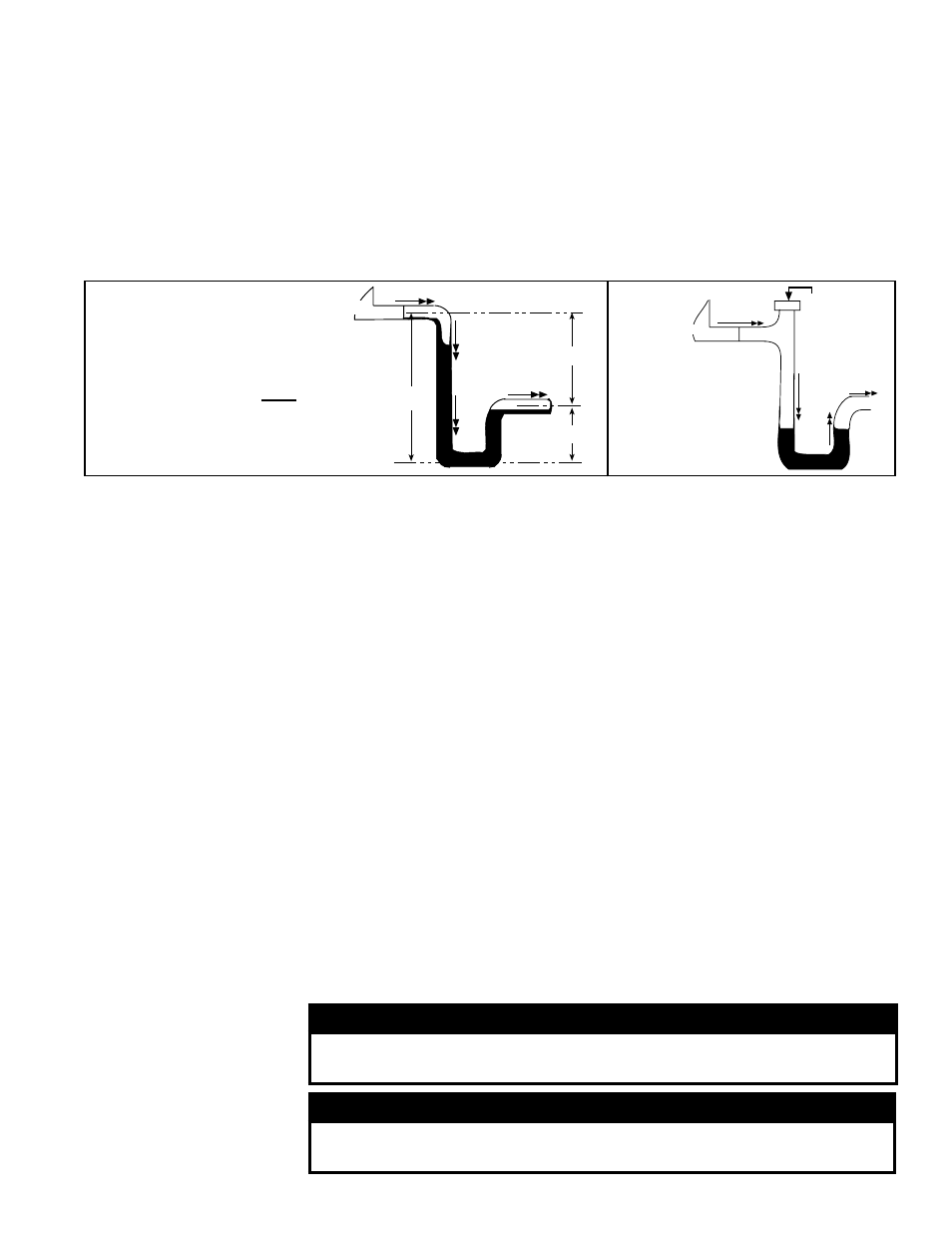
Form I-Y, P/N 273646R6, Page 23
All electrical wiring and connections including electrical grounding MUST be made in
accordance with the National Electric Code ANSI/NFPA No. 70 (latest edition). In addi-
tion, the installer should be aware of any local ordinances or electric company require-
ments that might apply.
7.1 General
Check the rating plate for the supply voltage and current requirements. Run a separate
line voltage supply directly from the main electrical panel, making connection at the
disconnect switch. See
FIGURE 2 on page 7, FIGURE 3 on page 8 or FIGURE 4 on
page 9 for location of supply wiring entrance.
If the system has dual disconnect switches (Option BA7), two supply wires are required
(See
FIGURE 17A, page 24 and FIGURE 17B, page 24).
7.2 Supply Wiring
7.0 Electrical and
Wiring
7.2.1 Disconnect
Switch
The system must have a remote disconnect switch, a built-in disconnect switch, or
both.
If ordered with a built-in disconnect switch, the system will be factory equipped with
one or two built-in non-fusible, lockable disconnect switch(es). The built-in disconnect
switch(es) (Option BA6 or BA7) require copper wiring with amp capacity based on
75°C maximum temperature rating at the line side terminals.
If the system does not have a built-in disconnect switch, a field-provided or optional
shipped-separate, wall-mounted disconnect switch is required. It is recommended
that there is at least four feet (1.2M) of service room between the switch and system
access panels. All external wiring must be within approved conduit and have a mini-
mum temperature rise rating of 60°C.
Run conduit so that it does not interfere with
the system access panels. When providing or replacing fuses in a fusible disconnect,
use dual element time delay fuses and size according to the rating plate.
WARNING
To prevent injury or death due to electrocution or contact
with moving parts, lock an open disconnect switch.
WARNING
If the unit includes a gas furnace, always turn off the gas
when you turn off the power supply.
The design of the drain trap is important. Since the condensate drain pan is on the
blower inlet side, there is a negative pressure at the drain relative to the ambient. The
trap height must account for this static pressure difference. Maximum negative static
can be determined by reading the negative pressure at the blower inlet and adding .2”
iwc to allow for dirty filters.
If dimension "B" in
FIGURE 16A shown below is not tall enough, the water seal will not
hold, and air will be drawn through the drain pipe into the unit. If the outlet leg of the
trap is too tall, water will back up into the drain pan. As condensate forms during normal
operation, the water level in the trap rises until there is a constant outflow.
FIGURE 16A
shown below illustrates the appropriate dimensions for trapping a negative pressure
system.
Condensate Drain Trap in Cooling Coil Drain
To prevent air
from entering
always close
the cleanout.
Water Flow
Unit
FIGURE 16B -
Drain Trap with
Clean out
B
A
A/2
C
L
C
L
C
L
Unit
Water Flow
Water Flow
A = 1" (25mm) for each 1"
(25mm) of maximum
static pressure plus 1"
(25mm)
B = A + A/2
FIGURE 16A - Condensate
Drain Trap Dimensions
6.3 Cooling Section
Condensate
Drain (cont’d)