Brookfield DV-III Ultra Rheometer User Manual
Page 67
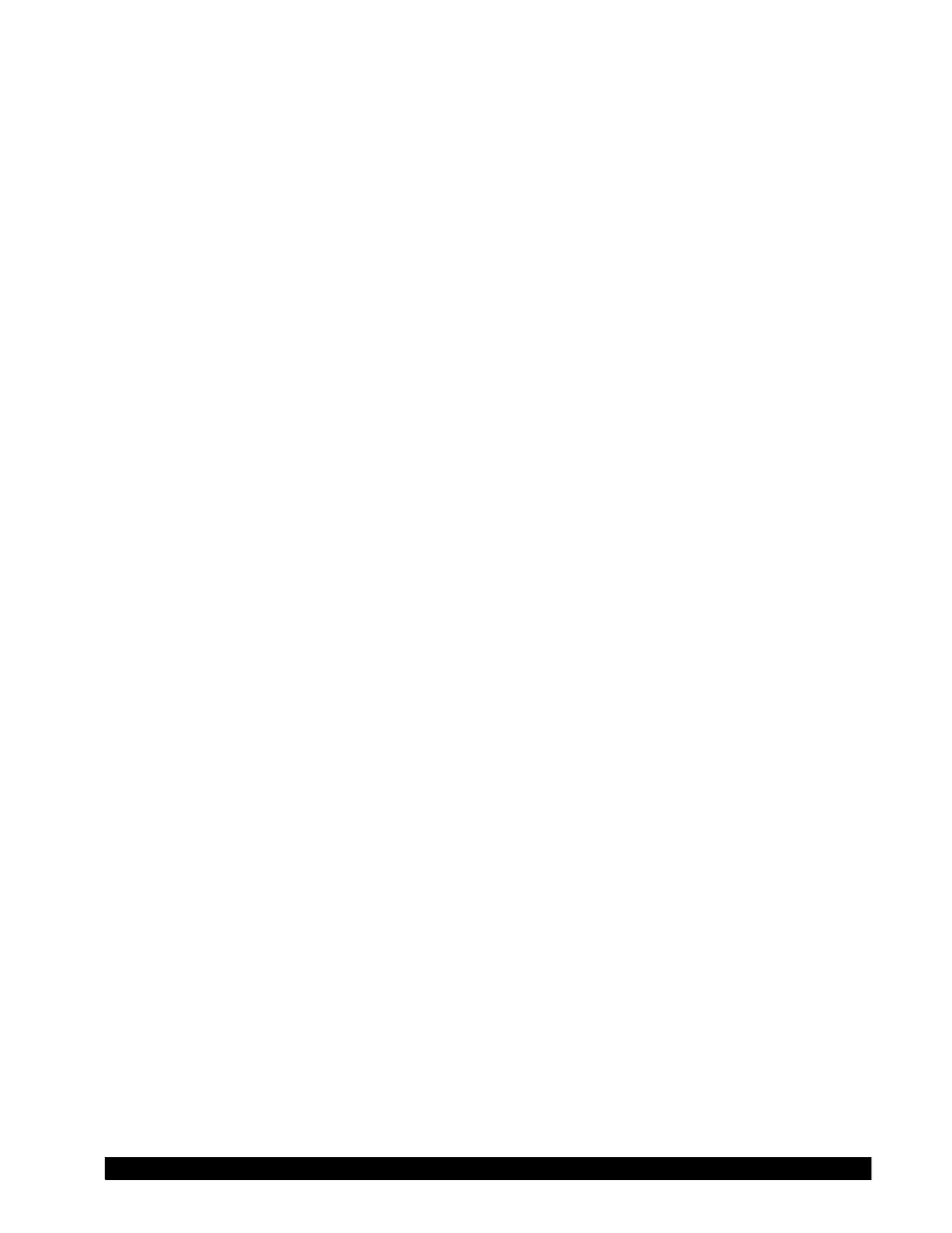
Brookfield Engineering Laboratories, Inc.
Page 67
Manual No. M98-211-E0912
Pre-shearing is the shearing of sample before measuring its yield properties. This process breaks
down the sample’s structure. It is particularly useful if the investigator wants to eliminate previous
shear history (e.g., bumping, transferring) of the sample before testing and observe the structural
rebuilding of the sample. This may simulate the following: ketchup pumped out of a bottle will
rebuild after it comes to rest on the French Fries. There are materials whose measured yield stress
will be lower after pre-shearing than if tested without pre-shearing. This may be used to compare
the rate at which different materials rebuild. The yield stress measured in a pre-sheared sample is
the “dynamic yield”, while the yield stress measured for an originally undisturbed material is the
“static yield”. Zeroing after pre-shearing is performed on the sample is highly recommended for
every test. The next section explains how to do this.
Zero
An optional, but highly recommended, torque Zero step can be included in the test parameters. If
the Zero box is checked on the Test Parameter page of the EZ-Yield software, the rheometer will
rotate the motor in the appropriate direction until 0% torque is achieved.
This may be necessary because the spindle sometimes twists a small amount during insertion into
the sample. This results in a small, although possibly significant, torque applied to the sample.
Slow zeroing speeds are used to eliminate this initial torque and minimize effects on the sample’s
structure before the test is started.
Zeroing is an essential step after preshearing.
This gives a consistent starting point for each test. A speed for the step must be supplied in the
appropriate box. Faster speeds achieve a “zero” quicker but may cause a more variable starting
point. See Appendix D2 for a complete list of zero step speeds.
Wait Time
An optional Wait step can be included in the test parameters. If the Wait Time box is checked on
the Test Parameters page of the EZ-Yield software, there will be a time delay after zeroing before
the actual test run begins. During this delay, the motor shaft will be at zero (0) RPM.
Wait Time is the time the sample is allowed to rest between the completion of zeroing and the start
of the yield measurement. Some samples rebuild structure more slowly than others after shearing,
such as during handling, pouring sample into a beaker, etc. Certain low-viscosity paints may also
have a low yield stress. Waiting 30 seconds, for example, after immersing the spindle may allow
the sample to rebuild, producing a more consistent test method.
Run Speed
Run Speed is the motor speed for the DV-III Ultra at which the material is tested. It is common for
materials to appear stiffer when tested at higher speeds. That is, the slope of the stress-vs.-strain
curve increases with increasing speed. This is because the material structure has less time in which
to react to dissipate the applied stress. Increasing the speed will, in most cases, increase the yield
stress measured by the instrument. Most yield tests are conducted at relatively low speeds (<1
rpm) to minimize any inertial effects when using vane spindles. See Appendix D2 for a complete
list of run speeds.
Base Increment
Base Increment is the amount of time in milliseconds between data points used for taking torque
(stress) readings. The software automatically calculates base increment values. Smaller base
increment values are used during faster speed tests to ensure that data are taken fast enough to
properly determine the yield point. Larger base increment values are used during slower speed
tests because these tests are expected to take longer and the longer time between data points helps
prevent typical data files from becoming very large. However, the user may still wish to set this
value to suit the required need after some familiarity is gained with the material being tested.
The % torque data are used to determine when a yield point is reached. The rigid line incremental
torque value is automatically calculated by the EZ-Yield software and depends on the Run Speed