Brookfield DV-III Ultra Rheometer User Manual
Page 6
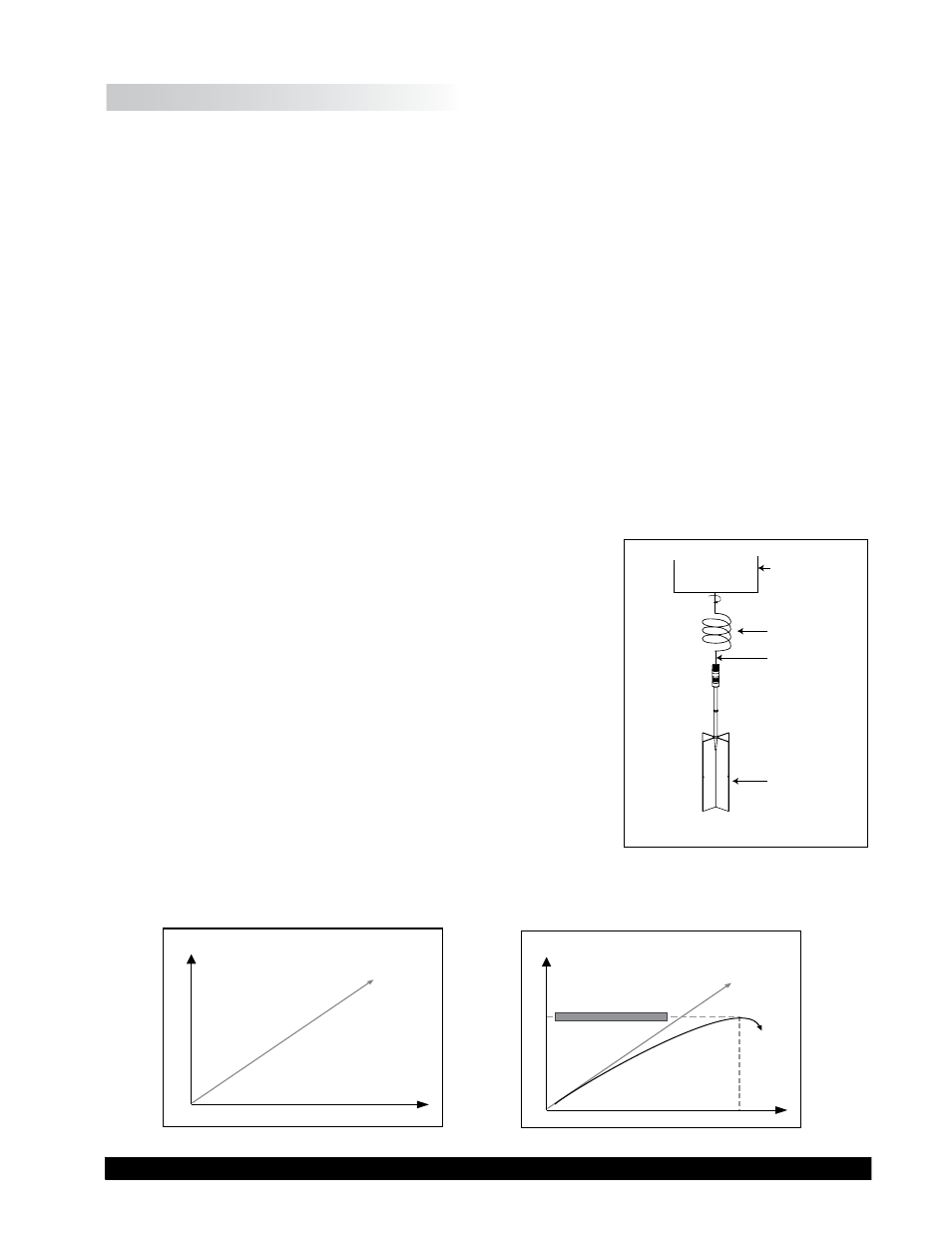
Brookfield Engineering Laboratories, Inc.
Page 6
Manual No. M98-211-E0912
I.3 Yield Stress Measurement
Another feature now available in the DV-III Ultra Rheometer is the yield stress test.
The yield point is the point at which a material begins to flow. The associated properties are the
yield stress and yield strain. The yield stress is the critical shear stress, applied to the sample, at
which the material begins to flow as a liquid. The yield strain is the deformation in the material,
resulting from the applied stress prior to the start of flow.
Many materials are designed to have a yield point, so that the behavior of their products satisfies
various customer needs. Foods often have yield points. Ketchup in particular must flow out of a
bottle when shaken or squeezed, but then solidify on the targeted food such as french fries. Shaking
or squeezing the bottle stresses the ketchup so that it flows; after the ketchup settles on the fries, its
structure rebuilds so the ketchup “sits” in place rather than flowing off the fries like water. Puddings
have yield points, as well. The “body” of the pudding appeals to consumers – it is solid at rest,
yet it’s easily spooned out of its cup and is easy to eat. Thus, the yield behavior of many foods
contributes to the food texture that we like.
Many paints have low yield stresses. Many latex house paints, for example, are easily stirred or
poured. Brushing or spraying provides enough stress so that the paint flows easily and smoothly
over a painted wall. However, a thin layer of applied paint (if a good one!), that is allowed to rest
undisturbed on the surface, regains its structure quickly so that there is very little unsightly “dripping”
afterwards. The smooth appearance of the painted surface is very appealing to the homeowner.
Motor
Calibrated
Spiral Spring
Drive
Shaft
Vane
Spindle
The operating principle is to drive a vane spindle through the
calibrated spiral spring connected to a motor drive shaft (see
Figure I-1). The vane spindle is immersed in the test material.
The resistance of the material to movement is measured by
observing increasing torque values as the DV-III Ultra motor
rotates. The amount of shaft rotation is measured by the deflection
of the calibrated spiral spring inside the instrument. Spring
deflection is measured with a rotary transducer.
If the vane spindle did not move at all, the data would look like
the graph in Figure I-2. The data often looks like the graph in
Figure I-3 because there is usually some deformation of the test
material due to the increasing force imparted by the vane spindle.
The maximum torque value is the yield point. The straight line
in Figure I-3 is a repeat of what was shown in Figure I-2. An
algorithm in the firmware converts the maximum torque value
into a yield stress value.
The shear stress measurement range of the DV-III Ultra (in Pascals) is determined by the size and
shape of the vane spindle and the full scale torque range of the calibrated spring.
Figure I-2
Maximum Torque Value
TIME
TORQUE
TIME
TORQUE
Figure I-3
Figure I-1