Flow sensor measurement techniques – ADS Environmental Services Model 3600 530002 A2 User Manual
Page 29
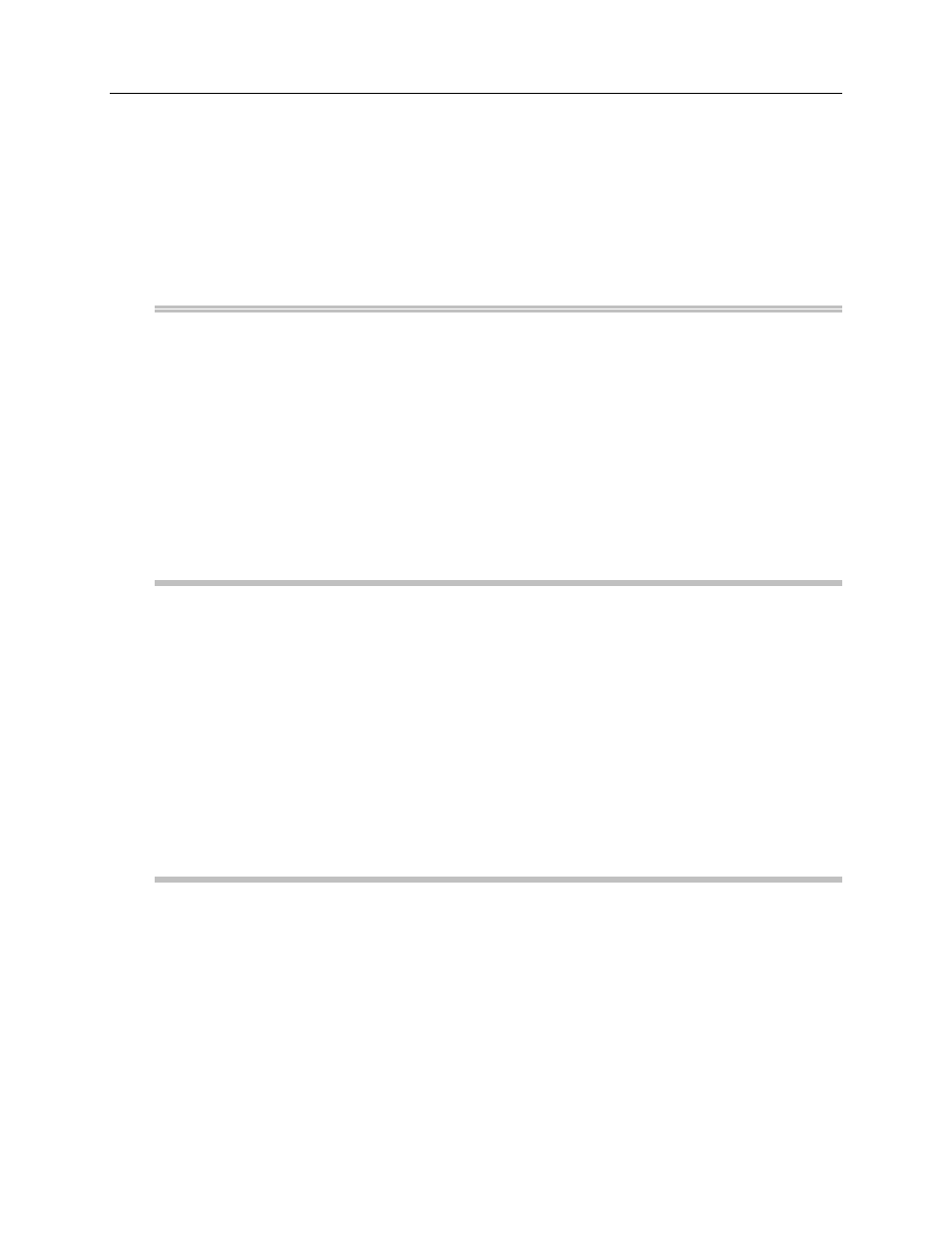
3-4
ADS 3600 Flow Monitor O&M Manual
Flow Sensor Measurement Techniques
The ultrasonic depth sensor, the pressure depth sensor, and the Doppler velocity
sensor gather raw flow data. The ultrasonic and pressure depth sensors use
independent measurement techniques to collect information about the depth of flow.
The Doppler velocity sensor gathers flow velocity data.
Upstream Installation
The sensors are mounted on a ring that is installed in the sewer pipe upstream from a
manhole. Upstream installation minimizes hydraulic effects and erroneous data
readings.
The process of installing the sensors in the incoming pipe is patented by ADS. The
system's hydraulics are much more stable and uniform in the incoming pipe than they
are in the manhole invert or in the outgoing pipe. In addition, upstream installation
minimizes monitoring errors caused by foamy waters, flow waves, sewer line noise,
and non-laminar flow.
Quadredundancy
Each ultrasonic depth sensor contains four ultrasonic transducers. To take a reading,
one transducer transmits a sound wave while a second transducer listens for the
returning echo. Taking readings with four transducer pairs gives the sensor
quadredundancy, which ensures greater sensor reading reliability.
In one firing of the ultrasonic depth sensor, each of the four sensor pairs takes thirty-
two readings. All false and multiple echoes are discarded. The good readings are
averaged to arrive at the final reading for each pair. The readings from each sensor
pair are then averaged into one final value. Refer to Appendix A for a technical
discussion of the ultrasonic depth system.
Ultrasonic Depth Sensor
The ultrasonic depth sensor, also known as a bat, is mounted at the crown (soffit) of
the pipe. The ultrasonic depth sensor transmits sound waves from the top of the pipe
to the surface of the flow. Then, it measures the time elapsed between transmission
and reception of the sound signal. This distance between the sensor face and flow
surface is the range. Using this elapsed time and the speed of sound, the ultrasonic
depth sensor can calculate the depth of the flow by subtracting the range from the pipe
diameter. The monitor compensates for air temperature by using the temperature