KROHNE ALTOSONIC V EN User Manual
Page 75
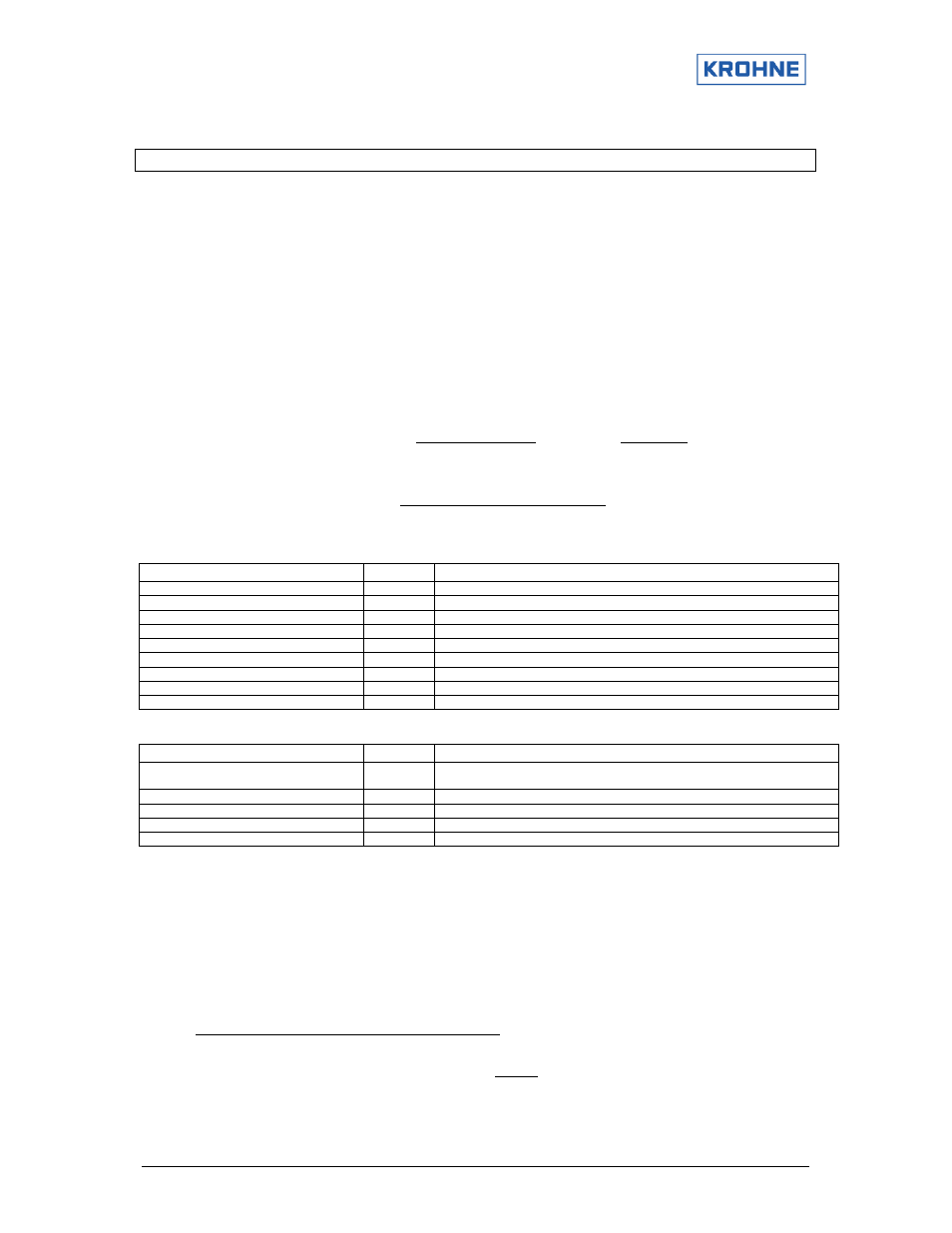
ALTOSONIC V
Operating Manual rev02 E
7.30850.34.00
Page 75 of 106
6.11.2 Measurement alarms batch validation
There are 2 methods for the batch validation:
1. Validation using the maximum flow. This is the method as used in previous versions of this
program. Using the maximum flow for validation has shown in practice that it can lead to
overrated Batch Error% values.
2. Validation using the current flow as long as the current flow is calculated. Since version
03.00.50.01.
The method is set in the CLNT0300.DAT file item: “21.17 Method of weighing”
6.11.2.1 Method 1 static maximum flow
To validate a batch when a measurement alarm has occurred over a period of time (Alarm in [s]) the
following calculation is used to validate the batch within a 0.04% error.
100
[%]
]
[
3600
]
/
3
[
]
3
[
_
Error
s
Alarm
h
m
MaxFlow
m
error
Volume
⋅
⋅
=
[%]
100
]
3
[
_
_
]
3
[
_
[%]
⋅
=
m
proces
Volume
Batch
m
error
Volume
Deviation
Secondary inputs measurement Error% on occurred alarm:
Secondary inputs
Error% Explanation
Temperature body
1
10°C is 0.036% deviation: 2% caused by >500°C
Temperature process
25
1°C is 0.1% deviation: 25% caused by 250°C deviation
Temperature proving external flow meter
25
1°C is 0.1% deviation: 25% caused by 250°C deviation
Temperature densito meter
25
1°C is 0.1% deviation: 25% caused by 250°C deviation
Pressure proces
2.5
1 bar is 0.01% deviation: 2.5% caused by 250 bar deviation
Pressure proving external flow meter
2.5
1 bar is 0.01% deviation: 2.5% caused by 250 bar deviation
Pressure densito meter
2.5
1 bar is 0.01% deviation: 2.5% caused by 250 bar deviation
Density densito meter
100
Standard volume correction uncertain therefore 100% errror
Density standard
100
Standard volume correction uncertain therefore 100% errror
UFP measurement Error% on occurred alarm:
Secondary inputs
Error% Explanation
1-4 channels down
0.5
Correction curve over viscosity never > 0.5%. (together with Real time
profile out of range error will lead to 4% error)
All channels down
100
System is not measuring flow therefore 100% error
API group mismatch
100
Standard volume correction uncertain therefore 100% errror
System alarms
10
Over estimated value on alarms as file not found, overrun etc
Real time profile out of range
3.50
Correction curve over viscosity never > 3.5%. To secure validity value=10%
Each alarm is measured in seconds, and the Volume_Error it causes, is calculated.
All Volume_error values are summated and the total deviation is calculated.
Example: How long may a certain error be active during a batch before the batch is Not Valid:
•
Only alarm 1-4 channels down: alarm time is x
•
Maximum flow rate is 1200m3/h
•
Batch time is 24 hours at 80% of the maximum flow rate
The batch volume in 24 hours at 80% flow rate:
]
3
[
23040
]
/
3
[
1200
100
[%]
80
]
[
24
]
3
[
Pr
_
_
m
h
m
h
m
oces
Volume
Batch
=
⋅
⋅
=