5 installation and wiring> 5-2 – Yokogawa Extractive Oxygen Gas Analyzer TDLS220 User Manual
Page 25
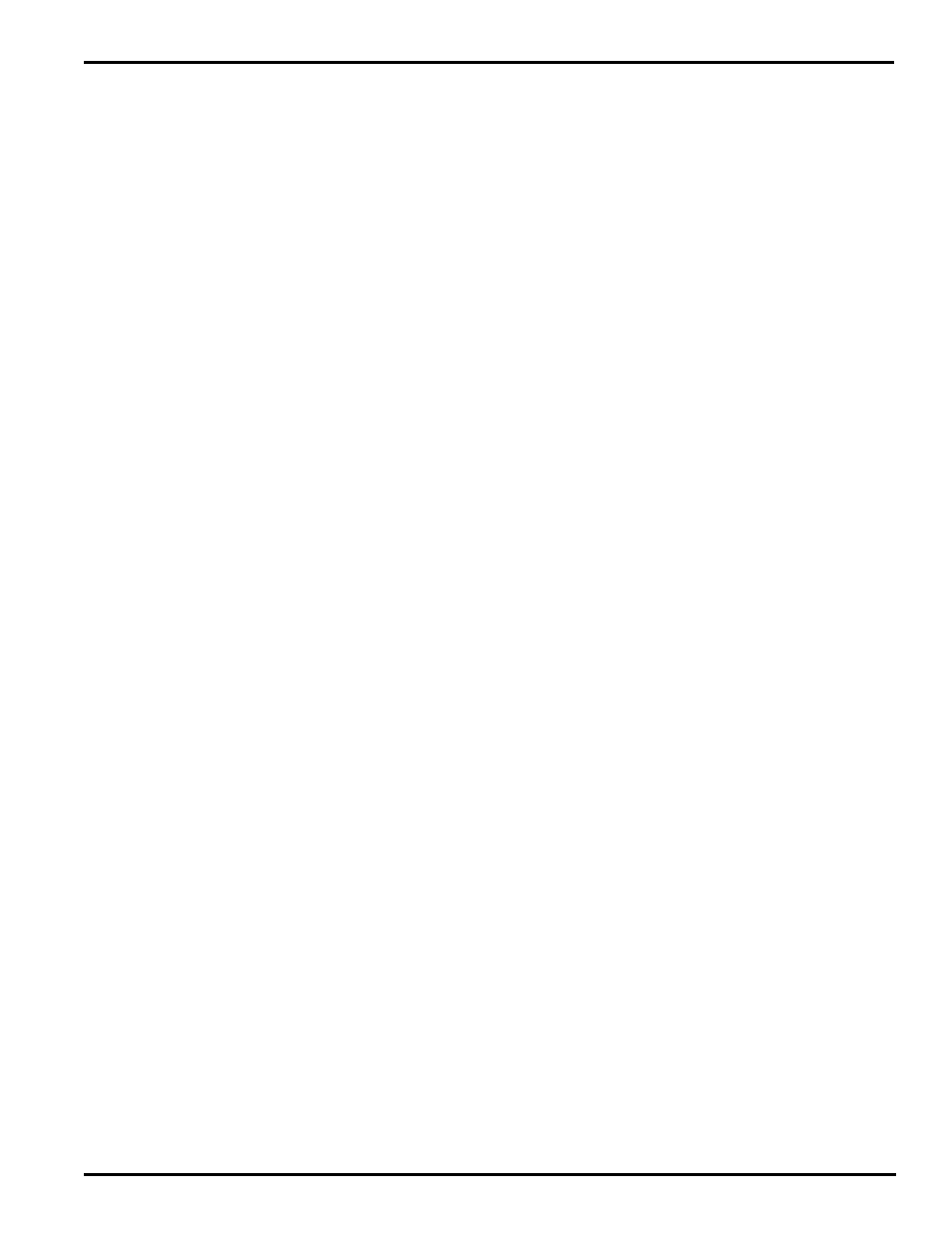
<5 INSTALLATION AND WIRING> 5-2
IM 11Y01B02-01E-A 4th Edition September 11, 2012-00
5.2 Sample Inlet and Outlet Considerations
The following criteria should be considered when selecting the installation point in respect to the process
conditions (1/4” OD Swagelok tube fittings):
Process Gas Condition: - The sample should be clean, dry, non-condensing at the inlet to the
sample cell. The dew point of the sample should be below the sample cell operating temperature.
If the sample cell is not heated and un-insulated then the sample must be non-condensing through
the entire ambient operating conditions.
NOTE: Oils, waxes, impure cleaners, and other deposits on the sample cell/mirror will cause
optical noise and subsequent analytical performance degradation. Please take all necessary
precautions to ensure the incoming sample gas is clean and dry at all times!
Process Gas Flow Conditions – Typically 1-10lts/min sample flow. A so-called normal flow-rate
would be in the order of 2-3lts/min. Higher flow-rates will improve the sample lag time within the
measurement cell. Sample flowmeter can be typically installed on the inlet when equipped with
needle valve. Excessive flow-rates may result in gas temperature control issues if the delta T of
incoming gas and cell temperature set-point exceed 15 deg C.
Process Gas Temperature – It is recommended that the sample gas inlet remains within +/-15deg
C of the sample cell temperature set-point. If the sample cell is un-heated then the sample gas
should be with +/-10 deg C of the ambient temperature. Please ensure that the process gas
entering the sample cell is above the dew point. If necessary, utilize membrane or coalescing type
filter device on the inlet.
Lower gas temperatures generally lead to better measurements.
• Process Gas Pressure – It is recommended that the analyzer be installed at a location where
pressure fluctuations are minimized. Generally as a guide, if the temperature of the gas at the point
where the analyzer is to be installed is to vary by more than +/-0.05Bar (+/-0.725psi) then an
“Active” input signal should be used for compensation.
Ensure the analyzer has been selected and configured to suit the maximum operating gas
pressure.
Ensure the process isolation windows have been selected and configured to suite the maximum
design gas pressure.
Lower gas pressures generally lead to better measurements.
Process Dust/Particulate Matter – It is recommended that the process gas is filtered to <2u using pro-
cess analytical grade filtration systems.