FEC AFC1500 User Manual
Page 17
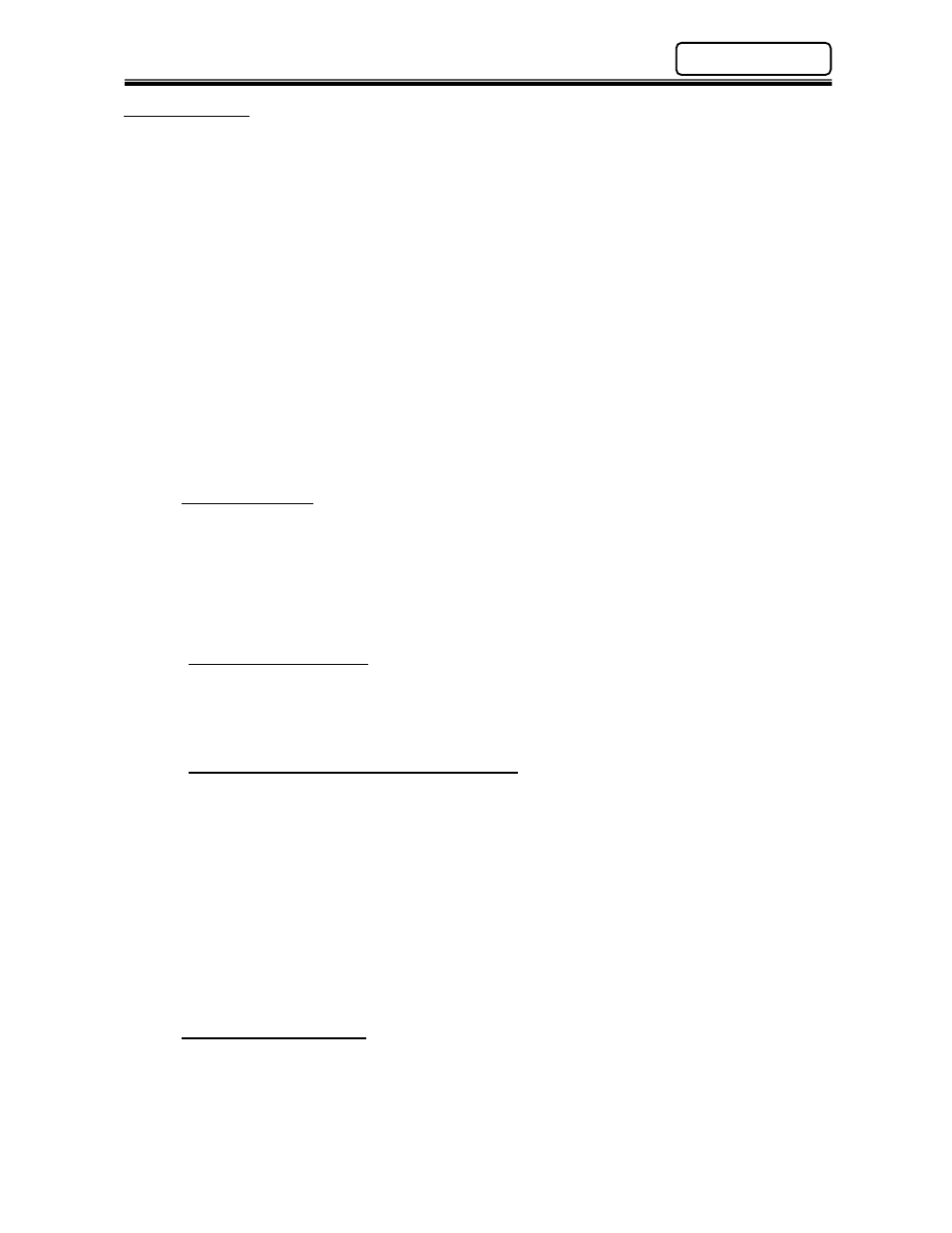
AFC1500 Multi-2 Unit Hardware Manual (Rev. 2)
PAGE 1 - 3
Chapter 1: Outline
1.2 Functions
The Multi-2 Unit is a complimentary controller device to enhance the AFC1500 SAN Unit capabilities
by providing the communication and the sequence control features required by larger or more
sophisticated multi spindle applications. When a group of AFC1500 Servo Controllers (SAN Units) are
linked to a Multi-2 Unit, the Multi-2 Unit assumes control (over these spindles) of the following
functions:
Input / Output (I/O) connection (including Fieldbus interfaces)
Sequence Control
Parameter Programming
Fastening Data Monitoring & Communication
General Status Indication
♦
Input / Output (I/O) Connection
The Multi-2 Unit assumes control of the control signals (Ex.: STOP, START, REVERSE,
BYPASS, etc.) to all of the AFC1500 Servo (SAN) Controllers connected to it via the RS485
communication port, thus eliminating direct connection & control to the individual spindles
saving costly I/O connection. The control signals for the multi-spindle array can be of
different sources: Signals manually generated by pressing the Control Buttons on the front of
the Multi-2 Unit or I/O (Input/Output) signals from a PLC and / or PC Based Controller.
Additionally, a multitude of (direct connect) Fieldbus interfaces are available when using a
Multi2 Unit.
♦
♦
♦
♦
Sequence Control
The Multi-2 Unit controls the fastening sequencing eliminating the need for external control
devices (PLC) to perform complicated spindle control sequencing. All fastening sequencing is
handled by the Multi-2 Unit. This built in feature allows the Multi-2 Unit to control a variety of
complex sequencing strategies including; incremental fastening steps, spindle grouping,
reject (reverse) strategies, wait timing, multiple starts, etc. Also available are sequence
Input / Output interfaces which allow external control of sequence starting / stopping with
outside automation while in sequence.
♦
♦
♦
♦
Parameter Programming
A Windows® compatible computer running the AFC User Console software package can be
connected to the Multi-2 Unit in order to upload or download the preset data to all the SAN
(Servo) Controllers connected in the multi spindle array. This eliminates the need to program
individual spindles manually.
♦
♦
♦
♦
Fastening Data Monitoring & Communication
The Multi-2 Unit can monitor and process the fastening results collected by the AFC1500 Servo
(SAN) Controllers connected to it. It has four (4) configurable RS232C ports to input and output
fastening data results. Data monitoring / saving is also a function of the AFC User Console
software package.
As an added feature, the Multi-2 Unit stores previous fastening data in RAM (non-volatile) for
uploading at another time. The number of cycles stored is based on the number of spindles
connected (see chart on page 2-2). The data can be uploaded using the AFC User Console
software package.
Additionally, the Multi -2 comes standard with an dedicated ethernet port to connect to a
computer running the AFC User Console Software package making it easier to connect to most
computers without serial convertors. As an option, the Multi - 2E comes with an additional
ethernet port for reporting of resultant fastening data to host systems.
♦
♦
♦
♦
General Status Indication
A set of indicator LED’s provide the status for Power On, Busy, Total Accept, Total Reject and
Abnormal conditions.