Xylem System 5000 User Manual User Manual
Page 87
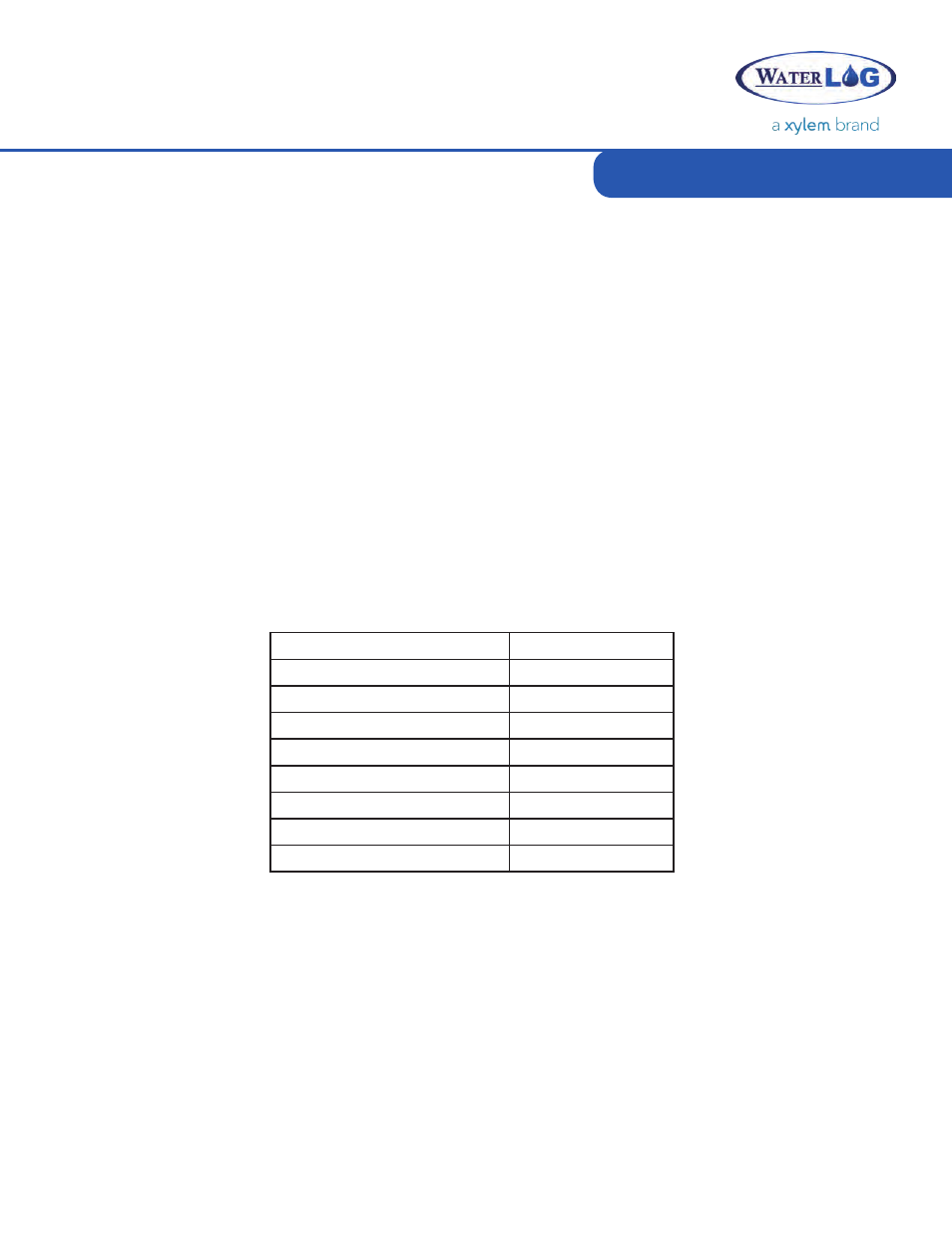
Modbus
85
Modbus is an industry standard field bus for interconnecting Programmable Logic Controllers
(PLCs), intelligent sensors, and other devices. The System 5000™ can act as a Modbus Master
and/or Modbus Slave over the serial and network ports as of firmware version 1.4.2.
As a Modbus Master, the data logger can read and write registers on connected Modbus Slave
devices. As a Modbus Slave, the data logger can respond to Modbus Master read and write
requests by reporting and updating data values for any source that can normally be logged or
transmitted. All external Modbus Master requests return the most recent measured value of the
assigned Task.
Modbus supports communication over the RS-232 and Ethernet ports, supporting the RTU,
ASCII, and TCP Modbus protocols. Modbus Master also supports Modbus over TCP or RTU/IP.
Multiple Modbus setups can exist on multiple ports. Serial ports can be configured as needed,
allowing differing baud rates, data bits, parity, etc. Modbus Registers can also be configured to
accept and report a wide of value types.
Modbus Overview
Supported Function Codes
The System 5000
™
supports the following Modbus functions:
Function name
Function Code
Read Coils
0x01
Read Discrete Inputs
0x02
Read Holding Registers
0x03
Read Input Register
0x04
Write Single Coil
0x05
Write Single Register
0x06
Write Multiple Coils
0x0F
Write Multiple Registers
0x10
Configuring Modbus
A Modbus Master or Modbus Slave setup can be easily created or modified by selecting the
corresponding Modbus entry in a Task’s Input or Output select menu. The similarities between
the Master and Slave operations of Modbus allow the setup screens and processes to be very
similar.
Determining Modbus Master or Modbus Slave
Both Modbus Master and Modbus Slave devices can support read and write operations. For this
reason, Modbus Master and Modbus Slave options are available in both the Select Input and Add
Output menus of the Edit Task screen of the System 5000
™
.