Where to mount, Internal heat - cause, effect, solution, Cleanliness – Gradall 534B (9103-1390) Service Manual User Manual
Page 69: How to mount, Importance of bleeding, Mico, incorporated mico west division
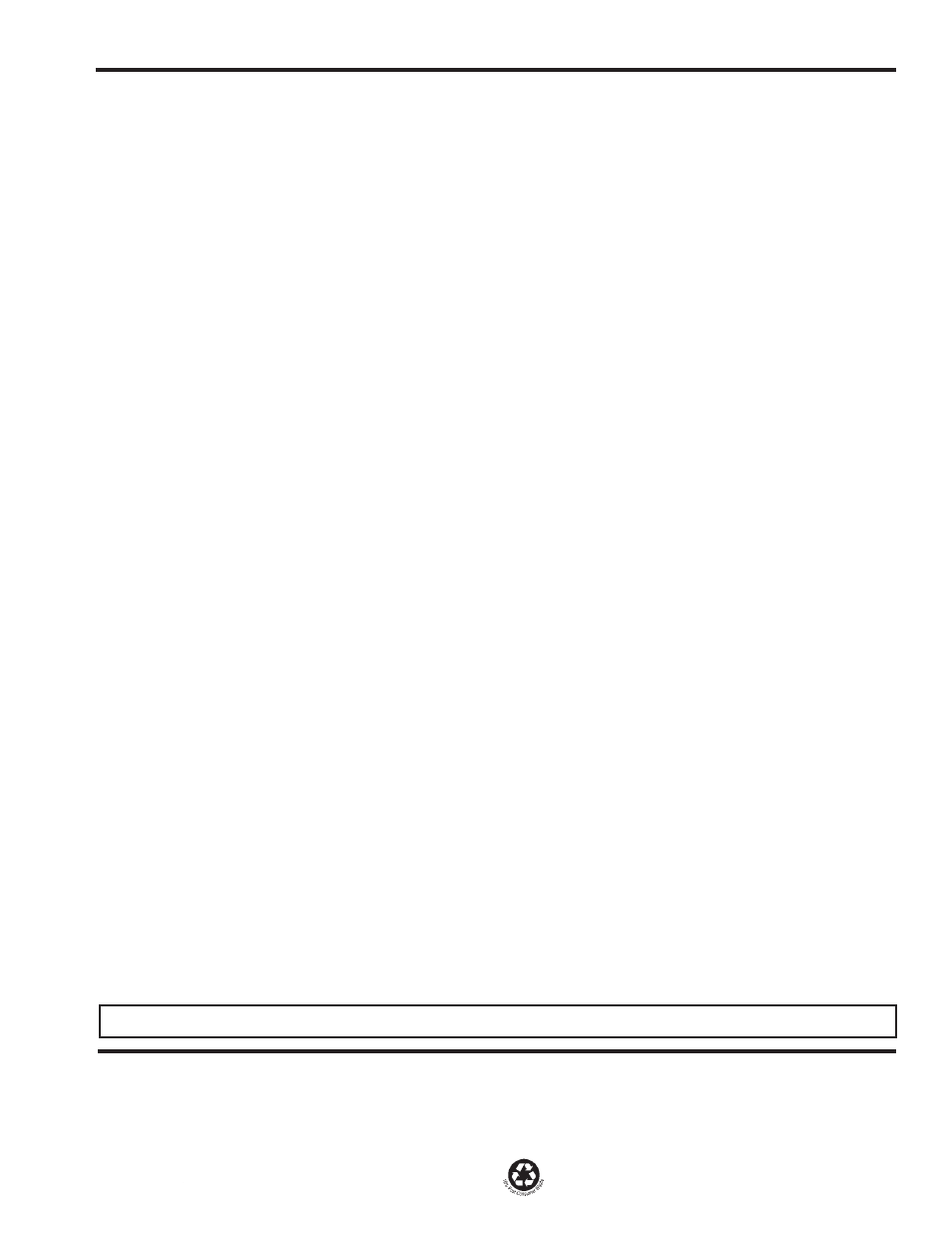
General Guidelines for installing Hydraulic Brake Components
MICO Hydraulic Brake Components are precision built devices
and must be treated as such. The following guidelines must be
followed at the time of installation to ensure optimum performance.
Where to Mount
To properly locate the brake component or brake line, you must. . .
1. Make it convenient for operator.
2. Use the shortest and most protected route. Protect
components from road salts and general debris.
3. Avoid exposing components and lines in wheel
compartments.
4. Avoid mounting near engine, exhaust lines, muffler or
anywhere that heat may be generated. NOTE: Excessive
heat transferred to brake fluid may result in damage to
lines or seals.
5. Mount units that have to be bled lower than master cylinder
and with bleeder screws on top to facilitate bleeding.
Internal Heat - Cause, Effect, Solution
It is possible for heat to come from within the system itself as in
the case of heat generated by the friction of lining to drum when
braking. This heat can cause the fluid to expand. If the fluid is
then held captive, subsequent cooling and contracting can cause
a pressure drop.
MICO Hydraulic Locking Devices that include a pressure
accumulator are designed to dampen these fluctuations of
pressure and to absorb the increase in pressure within its
operating range.
Cleanliness
It is impossible to overemphasize the importance of cleanliness
during installation. All lines, fittings and adjacent areas must be
cleaned of dirt or road residue before any lines or fittings are
disconnected. Special care must be taken so dirt and road
residue are not allowed to enter the hydraulic brake system.
This can contaminate the system and interfere with the proper
operation of the brakes and other hydraulic components.
Always. . .
1. Use good, clean, quality fluid. Improper or contaminated
brake fluid may cause gummy deposits and softening
and swelling of other rubber seals in the entire brake
system. Such a condition must be corrected immediately.
a. Use brake fluid which conforms to SAE Spec. No.
J1703 or DOT 3 or 4 if the product is used with a
system utilizing automotive brake fluid.
b. Refer to vehicle manufacturer for fluid specification if
product is used with:
1. Mineral based hydraulic oil.
2. Phosphate ester base fluid.
3. Water/glycol fluid.
4. Water-in-oil emulsion fluid.
5. DOT 5 or silicone fluid.
2. Be sure fittings and seats are clean before making
connections. Do not use sealants, tapes, teflon or cement
compounds on any connections or fittings. These sealants
or compounds can contaminate the hydraulic brake
system and interfere with the operation of brake system
components.
3. Clean top of master cylinder before removing filler cap.
How to Mount
To properly mount components and brake lines to withstand the
most severe vibration conditions, always. . .
1. Follow the procedures outlined in Vehicle Manufacturer’s
Service Manual or SAE Standards when making new
connections or adding to existing brake system. Use only
steel brake tubing conforming to SAE specifications.
2. Use the proper size bolt for the hole and secure with a
steel lock washer whenever possible.
3. Secure tubing to frame with proper size tube clamps to
avoid possible fractures or fittings loosening and leaking.
4. Use good, factory flared lengths of steel tubing. Hand
made flares, when used, must be double flared. Any
flash or loose particles must be moved.
5. Use flexible brake line between frame and body.
6. Use grommets or some other means to protect brake
lines that pass through the frame or firewall.
7. Make sure fittings and connections are in good condition
and tightened to proper torque values as specified in
the installation and service instructions.
Importance of Bleeding
The hydraulic brake system must be bled whenever any line has
been disconnected. Air trapped in the system can cause spongy
and inadequate brakes. There are two methods of bleeding
hydraulic systems, pressure bleeding and manual bleeding. Both
methods are acceptable and adequate but pressure bleeding is
recommended if the equipment is available. Follow bleeding
instructions as specified by vehicle manufacturer.
To properly bleed the system. . .
1. Be certain all fittings are tight to avoid leaking.
2. Depress pedal and open up bleeder screws to allow air
to escape. Air will always seek the highest level.
3. Retighten bleeder screws and allow pedal to return.
4. Repeat cycle until pedal is firm.
5. Make several static brake applications and then repeat
cycle once more.
Leak in the System
Even the smallest leak in a brake system will adversely affect
the system. A leak may eventually deplete the reserve supply
and reduce braking pressure. To help prevent leaking. . .
1. Check connections during bleeding and static brake
processes to be sure they are tight.
2. Always reinstall new hoses, lines and fittings if they look
the least bit questionable.
3. Brake hoses, brake lines, MICO locking device, brake
components, cylinders, and all fittings must be routinely
inspected for leaks, damage or wear. Adequate fluid
levels must be maintained. In the event of any loss of
fluid, the brake system must be carefully inspected for
leaks.
MICO is a registered trademark of MICO, Incorporated. MICO is registered in the U.S. Patent and Trademark Office as well as in Canada, Great Britain, South Korea and Australia.
MICO, Incorporated
MICO West Division
1911 Lee Boulevard (Zip Code 56003-2507)
701 East Francis Street (Zip Code 91761-5514)
P.O. Box 8118 / North Mankato, MN U.S.A. 56002-8118
P.O. Box 9058 / Ontario, CA U.S.A. 91762-9058
(
(507) 625-6426
Facsimile (507) 625-3212
(
(909) 947-4077
Facsimile (909) 947-6054
Form No. 81-600-001
Revised 5/97
Printed in U.S.A.
MICO has made every attempt to present accurate information in catalogs, brochures and other printed material. MICO can accept no responsibility for errors from uninten-
tional oversights that may exist. Due to a continuous program of product improvement, both materials and specifications are subject to change without notice or obligation.