Measuring (touch probe cycle 3), 7 a u to matic w o rk piece measur ement – HEIDENHAIN TNC 320 (340 551-02) User Manual
Page 458
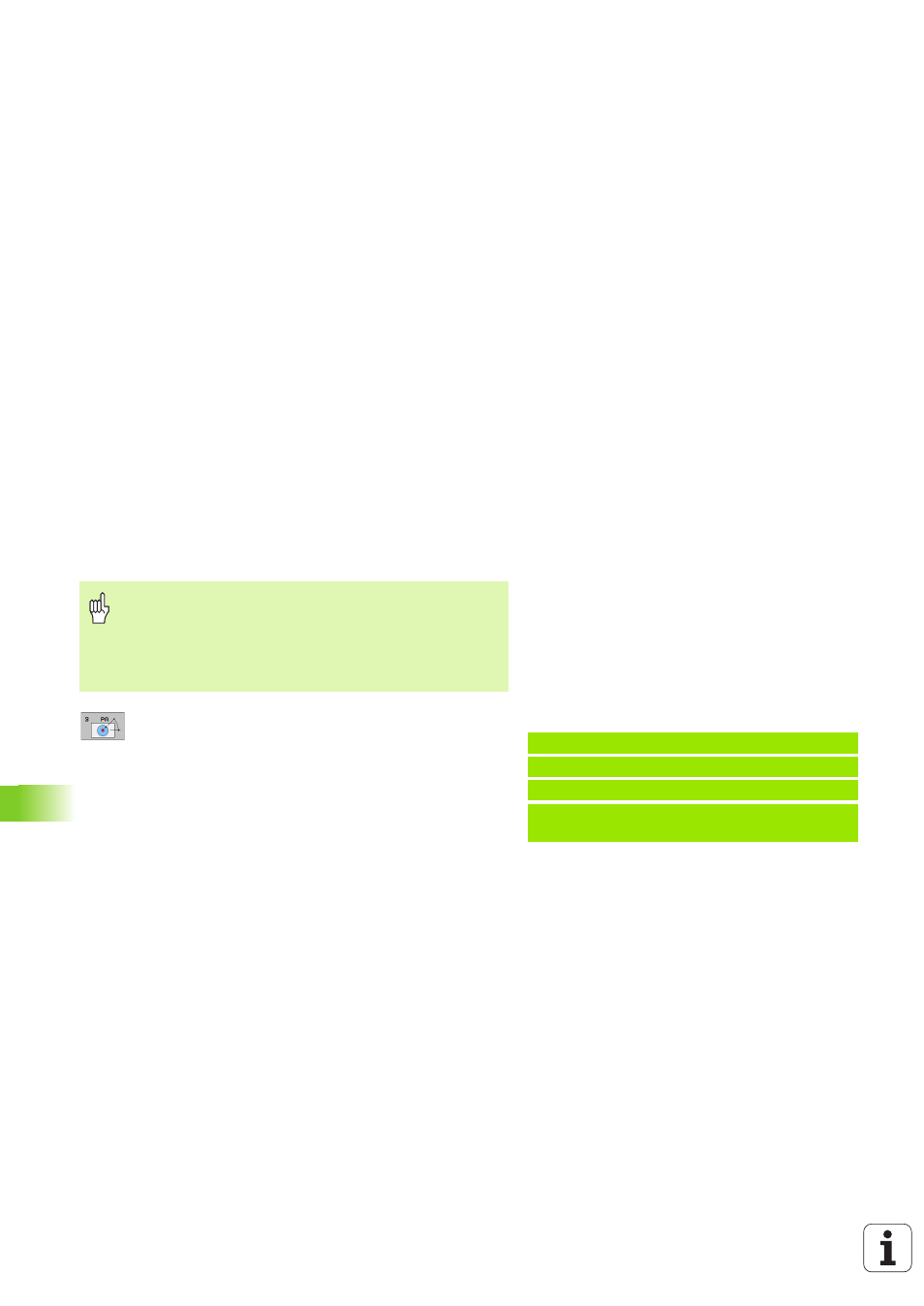
458
13 Touch Probe Cycles in the Manual and Electronic Handwheel Modes
13.7 A
u
to
matic W
o
rk
piece Measur
ement
MEASURING (touch probe cycle 3)
Touch probe cycle 3 measures any position on the workpiece in a
selectable direction. Unlike other measuring cycles, Cycle 3 enables
you to enter the measuring path and feed rate directly. Also, the touch
probe retracts by a definable value after determining the measured
value.
1
The touch probe moves from the current position at the entered
feed rate in the defined probing direction. The probing direction
must be defined in the cycle as a polar angle.
2
After the TNC has saved the position, the touch probe stops. The
TNC saves the X, Y, Z coordinates of the probe-tip center in three
successive Q parameters. You define the number of the first
parameter in the cycle.
3
Finally, the TNC moves the touch probe back by that value against
the probing direction that you defined in the parameter MB.
8
Parameter number for result:
Enter the number of
the Q parameter to which you want the TNC to assign
the first coordinate (X).
8
Probe axis:
Enter the reference axis of the working
plane (X for tool axis Z, Z for tool axis Y, and Y for tool
axis X), and confirm with ENT.
8
Probing angle:
Angle, measured from the probing
axis, at which the touch probe is to move. Confirm
with ENT.
8
Maximum measuring path:
Enter the maximum
distance from the starting point by which the touch
probe may move. Confirm with ENT.
8
Feed rate:
Enter the measuring feed rate in mm/min.
8
Maximum retraction path:
Traverse path in the
direction opposite the probing direction, after the
stylus was deflected.
8
REFERENCE SYSTEM (0=ACT/1=REF):
Specify whether
the result of measurement is to be saved in the actual
coordinate system (ACT), or with respect to the
machine coordinate system (REF).
8
To conclude the input, press the ENT key.
Before programming, note the following:
Enter the maximum retraction path MB to be just large
enough to prevent a collision.
If the TNC could not determine a valid touch point, the
fourth result parameter will have the value –1.
Example: NC blocks
5 TCH PROBE 3.0 MEASURING
6 TCH PROBE 3.1 Q1
7 TCH PROBE 3.2 X ANGLE: +15
8 TCH PROBE
3.3 DIST +10 F100 MB:1 REFERENCE SYSTEM:0