5 sl cy cles – HEIDENHAIN TNC 320 (340 551-02) User Manual
Page 275
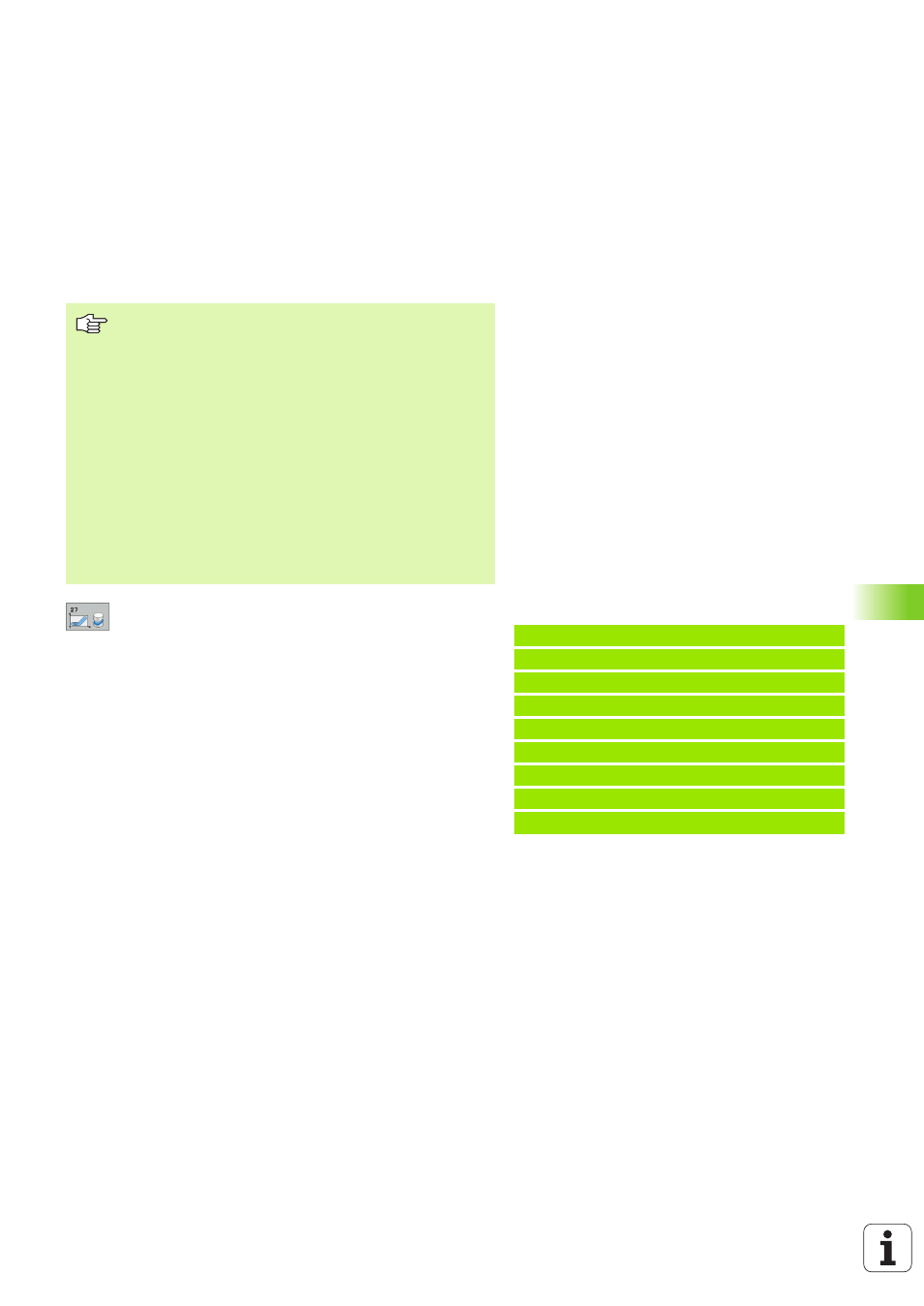
HEIDENHAIN TNC 320
275
8.5 SL Cy
cles
8
Milling depth
Q1 (incremental value): Distance
between the cylindrical surface and the floor of the
contour.
8
Finishing allowance for side
Q3 (incremental
value): Finishing allowance in the plane of the unrolled
cylindrical surface. This allowance is effective in the
direction of the radius compensation.
8
Set-up clearance
Q6 (incremental value): Distance
between the tool tip and the cylinder surface.
8
Plunging depth
Q10 (incremental value): Dimension
by which the tool plunges in each infeed.
8
Feed rate for plunging
Q11: Traversing speed of the
tool in the tool axis.
8
Feed rate for milling
Q12: Traversing speed of the
tool in the working plane.
8
Cylinder radius
Q16: Radius of the cylinder on which
the contour is to be machined.
8
Dimension type ? (ANG/LIN)
Q17: The dimensions for
the rotary axis (X coordinates) of the subprogram are
given either in degrees (0) or in mm/inches (1).
Before programming, note the following:
In the first NC block of the contour program, always
program both coordinates.
The memory capacity for programming the cycle is limited.
You can program up to 1000 contour elements in one cycle.
The cycle can only be run with a negative depth. If a positive
depth is entered, the TNC will output an error message.
This cycle requires a center-cut end mill (ISO 1641).
The cylinder must be set up centered on the rotary table.
The tool axis must be perpendicular to the rotary table.
If this is not the case, the TNC will generate an error
message.
This cycle can also be used in a tilted working plane.
Example: NC blocks
63 CYCL DEF 27 CYLINDER SURFACE
Q1=-8
;MILLING DEPTH
Q3=+0
;ALLOWANCE FOR SIDE
Q6=+2
;SET-UP CLEARANCE
Q10=+3
;PLUNGING DEPTH
Q11=100
;FEED RATE FOR PLUNGING
Q12=350
;FEED RATE FOR MILLNG
Q16=25
;RADIUS
Q17=0
;TYPE OF DIMENSION