Cable for discrete drive i/o, Analog signal and encoder cable – Rockwell Automation 1336T Wiring and Grounding Guide, (PWM) AC Drives User Manual
Page 21
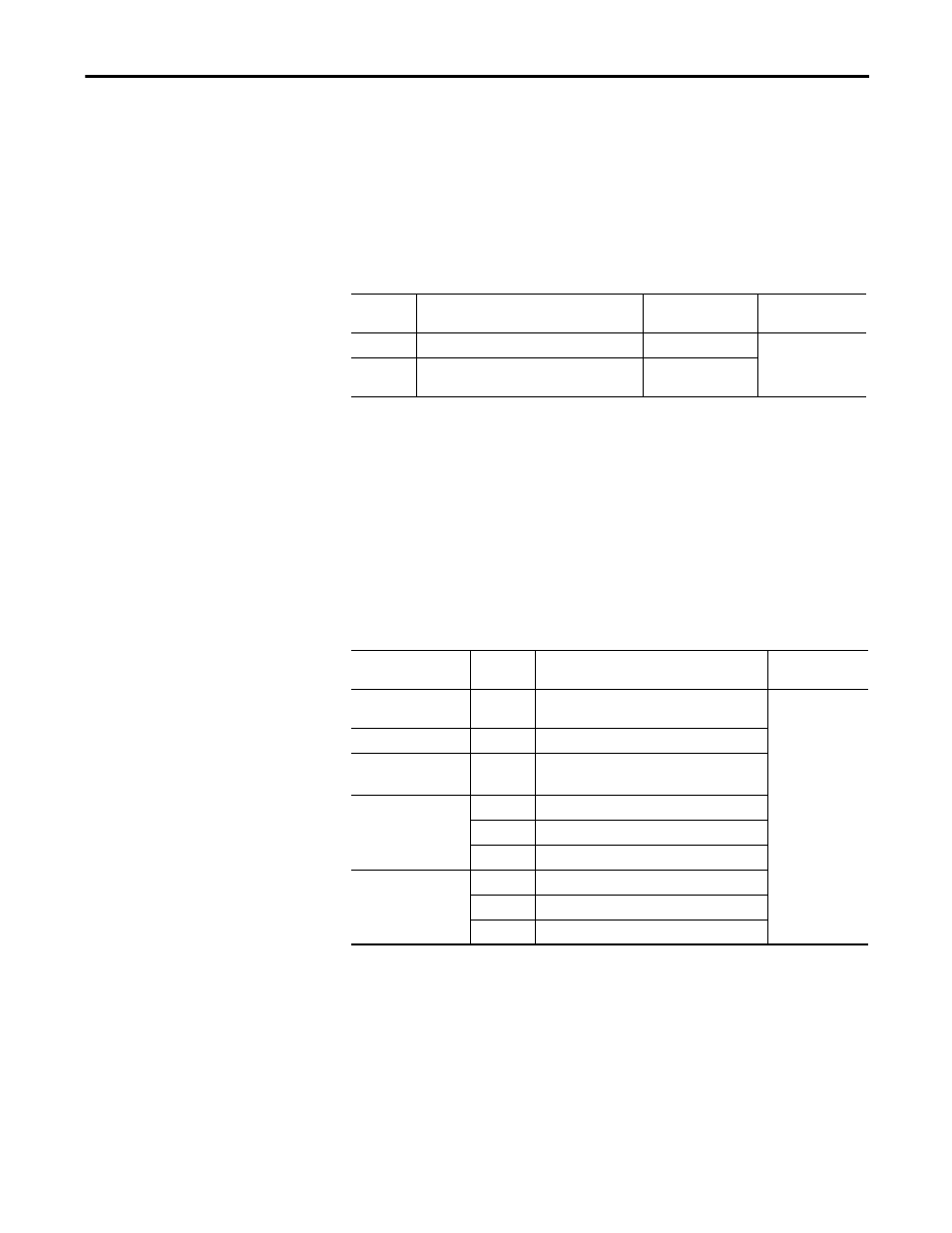
Rockwell Automation Publication DRIVES-IN001M-EN-P - March 2014
21
Wire/Cable Types Chapter 1
Cable for Discrete Drive I/O
Discrete I/O, such as start and stop commands, can be wired to the drive with a
variety of cabling. We recommend shielded cable to reduce cross-coupled noise
from power cables. Standard individual conductors that meet the general
requirements for type, temperature, gauge, and applicable codes are acceptable if
they are routed away from higher voltage cables to minimize noise coupling.
However, multi-conductor cable can be less expensive to install. Separate control
wires from power wires by at least 0.3 m (1 ft)
Table 2 - Recommended Control Wire for Digital I/O
Analog Signal and Encoder
Cable
Always use shielded cable with copper wire. We recommend wire with an
insulation rating of 300V or greater. Separate analog signal wires from power
wires by at least 0.3 m (1 ft). Run encoder cables in a separate conduit. If signal
cables must cross power cables, cross at right angles. Terminate the shield of the
shielded cable as recommended by the manufacturer of the encoder or analog
signal device.
Table 3 - Recommended Signal Wire
Type
(1)
(1) The cable choices shown are for 2-channel (A and B) or 3-channel (A,B, and Z) encoders. If high resolution or other types of
feedback devices are used, choose a similar cable with the correct gauge and number of conductor pairs.
Wire Type(s)
Description
Minimum
Insulation Rating
Unshielded
Per US NEC or applicable national or local code
–
300V, 60 °C
(140 °F)
Shielded
Multi-conductor shielded cable
0.750 mm
2
(18 AWG),
3-conductor, shielded.
Signal Type/
Where Used
Wire
Type(s)
Description
Minimum
Insulation Rating
Standard analog I/O
–
0.750 mm
2
(18 AWG), twisted pair, 100% shield
with drain
(1)
(1) If the wires are short and contained within a cabinet that has no sensitive circuits, the use of shielded wire is not always necessary,
but is recommended.
300V,
75…90 °C
(167…194 °F)
Remote pot
–
0.750 mm
2
(18 AWG), 3-conductor, shielded
Encoder/Pulse I/O
< 30.5 m (100 ft)
Combined
0.196 mm
2
(24 AWG), individually shielded
Encoder/Pulse I/O
30.5…152.4 m
(100…500 ft)
Signal
0.196 mm
2
(24 AWG), individually shielded
Power
0.750 mm
2
(18 AWG)
Combined
0.330 mm
2
or 0.500 mm
2
Encoder/Pulse I/O
152.4…259.1 m
(500…850 ft)
Signal
0.196 mm
2
(24 AWG), individually shielded
Power
0.750 mm
2
(18 AWG)
Combined
0.750 mm
2
(18 AWG), individually shielded pair
- 1336E Wiring and Grounding Guide, (PWM) AC Drives 1336F Wiring and Grounding Guide, (PWM) AC Drives 1336S Wiring and Grounding Guide, (PWM) AC Drives 1336VT Wiring and Grounding Guide, (PWM) AC Drives 1336 Wiring and Grounding Guide, (PWM) AC Drives 1305 Wiring and Grounding Guide, (PWM) AC Drives 25B Wiring and Grounding Guide, (PWM) AC Drives 20N Wiring and Grounding Guide, (PWM) AC Drives 20M Wiring and Grounding Guide, (PWM) AC Drives 22C Wiring and Grounding Guide, (PWM) AC Drives 22B Wiring and Grounding Guide, (PWM) AC Drives 22A Wiring and Grounding Guide, (PWM) AC Drives 20D Wiring and Grounding Guide, (PWM) AC Drives 20C Wiring and Grounding Guide, (PWM) AC Drives 20B Wiring and Grounding Guide, (PWM) AC Drives 20A Wiring and Grounding Guide, (PWM) AC Drives 1336R Wiring and Grounding Guide, (PWM) AC Drives