4 process controller, 5 canopen communication – NORD Drivesystems BU0550 User Manual
Page 13
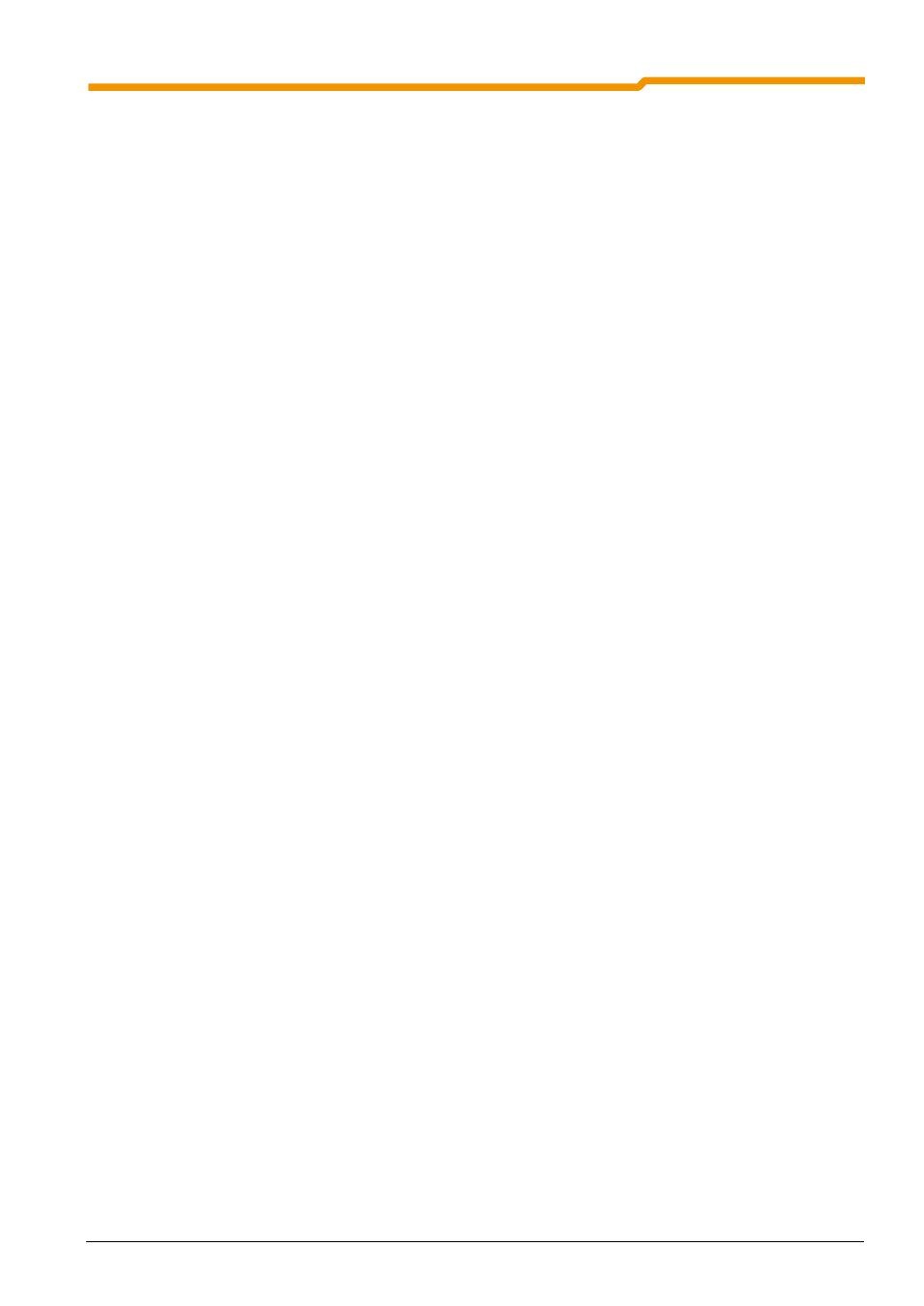
1 General
BU 0550 GB-0813
13
1.3.4
Process controller
The process controller is a PID-T1 controller with a limited output size. With the aid of this function module
in the PLC it is possible to simply set up complex control functions, by means of which various processes,
e.g. pressure regulation can be implemented in a considerably more elegant manner than with the
commonly used two-point controllers.
1.3.5
CANopen communication
In addition to the standard communication channels, the PLC provides further possibilities for
communication. Via the internal CAN bus of the inverter (connection via the RJ45 sockets), it can set up
additional communications with other devices. The protocol which is used for this is CANopen.
Communications are restricted to PDO data transfer and NMT commands. The standard CANopen inverter
communication via SDO, PDO1, PDO2 and Broadcast remains unaffected by this PLC function.
PDO (Process Data Objects)
Other frequency inverters can be controlled and monitored via PDO. However, it is also possible to connect
devices from other manufacturers to the PLC. These may be IO modules, CANopen encoders, or panels
etc. With this, the number of inputs and outputs of the frequency inverter can be extended at will. Analog
outputs would then also be possible.
NMT (Network Management Objects)
All CANopen devices must be set to the CANopen bus state "Operational" by the bus master. PDO
communication is only possible in this bus state. If there is no bus master in the CANopen bus, this must be
performed by the PLC. The function module FB_NMT is available for this purpose.