Inputs – Watlow Series SD PID Profiling Controller User Manual
Page 66
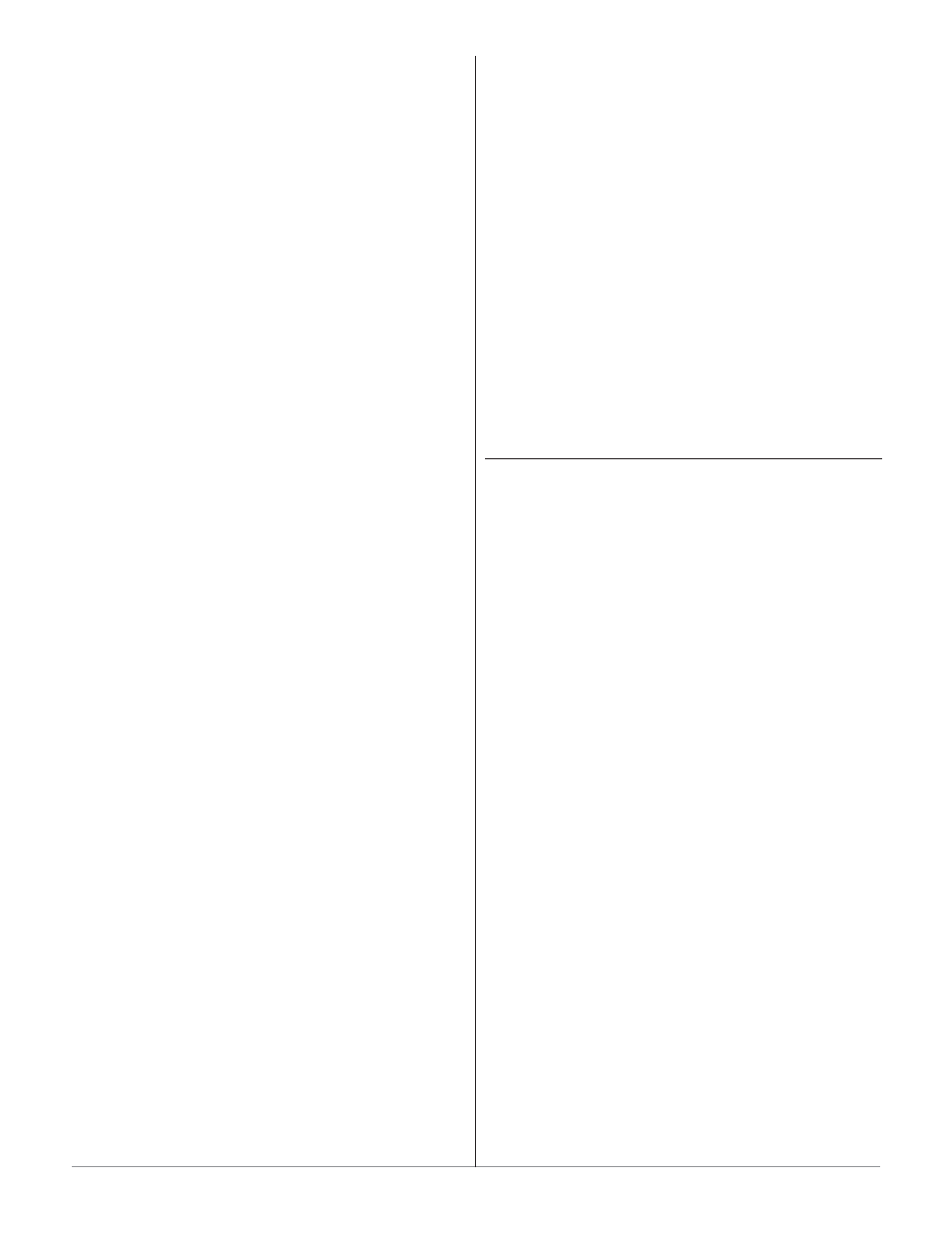
Wa t l o w S e r i e s S D
•
6 4
•
C h a p t e r 1 2 F e a t u r e s
Autotune Enable
[`Aut]: The Autotune Enable pa-
rameter appears in the Operations Page.
The autotune feature can be enabled if TRU-
TUNE+™ is enabled or disabled.
Autotuning with TRU-TUNE+™ adaptive control is
a process by which the Series SD controller calculates
the PID settings for optimum control. Both heating and
cooling PID parameter settings are determined. The au-
totune feature can also be enabled if TRU-TUNE+™ has
been disabled. The autotune generated PID settings are
used until the autotune feature is rerun or the PID vari-
able values are manually adjusted by the user or if TRU-
TUNE+™ is enabled.
The preferred and quickest method for tuning the
Series SD controller when TRU-TUNE+™ is enabled is
to use the autotune feature to establish initial control
settings and continue with the adaptive mode to fine
tune the settings. Enabling the autotune function from
the Operations Page starts this two-step tuning func-
tion. First the autotune determines initial, rough settings
for the PID parameters. Second the loop automatically
switches to the adaptive mode, which fine tunes the PID
parameters. This function can be used for heat-only, heat-
and-cool, and cool-only PID control systems.
Once the process value has been at set point for a
suitable period of time (about 30 minutes for a fast pro-
cess to roughly 2 hours for a slower process) and if no
further tuning of the PID parameters is desired or need-
ed, TRU-TUNE+™ can then be disabled. However, only
operating the controller in the adaptive mode allows it to
automatically adjust to load changes and compensate for
differing control characteristics at various set points for
processes that are not entirely linear.
Once the PID parameters have been set by the TRU-
TUNE+™ adaptive algorithm, the process, if shut down for
any reason, can be restarted in the adaptive control mode.
Autotune Aggressiveness
[AgrS]: This parameter
appears in the Setup Page. This parameter is used by the
autotune feature to determine how aggressively power
is applied to the controllers output to enable the process
value to reach the set point.
[Undr] Under damped. Aggressive PID values are se-
lected during autotune that bring the load quickly to the
set point. Overshoot is not critical and is allowed.
[OuEr] Over damped. PID values are selected during
autotune that minimize overshoot. It is not critical that
the load reach the set point quickly. Overshoot is critical
and is not allowed or kept to a minimum.
[Crit] Critical damped. PID values are selected dur-
ing the autotune that bring the load up to the set point
at power levels that allow for some overshoot. It is criti-
cal to get the load to the set point as fast as possible with
minimal overshoot.
[Crit] Critical damped is the default setting.
Tune Band
[t;bnd]: This parameter appears in the
Setup Page if TRU-TUNE+™ is enabled. Set the control-
ler to automatically adjust the range around set point
over which the controller will continuously tune the con-
trol parameters, or enter a fixed value. This parameter
is provided for use only in the unlikely event that the
controller is unable to automatically tune and stabilize at
set point. This may occur with very fast processes. In that
case select a large value, such as 300. Otherwise, leave
this parameter set to auto.
Values: auto (0) and 1 (1) to 999 (999)
Default: auto (0)
Tune Gain
[`t;gn] This parameter appears in the Set-
up Page if TRU-TUNE+™ is enabled. Choose the target
responsiveness of the control algorithm. Settings range
from 1, with the least aggressive response and least
potential overshoot (lowest gain), to 7, with the most ag-
gressive response and most potential for overshoot (high-
est gain). The default setting, 4, is recommended for loops
with thermocouple feedback and moderate response and
overshoot potential.
Values: 1 (1) to 7 (7)
Default: 4 (4)
Inputs
INFOSENSE™ Temperature Sensing
Watlow’s INFOSENSE™ feature can improve temper-
ature sensing accuracy by 50%. Watlow’s INFO-SENSE™
thermocouples and RTD temperature sensors must be
used together to achieve these results.
Each INFOSENSE™ “smart” sensor contains four nu-
meric values that are programmed into the SD memory.
These values characterize Watlow sensors, for the con-
troller to provide greater accuracy.
Turn the INFOSENSE™ feature on or off with INFO-
SENSE™ Enable
[IS;En] (Setup Page). Set the four nu-
merical values supplied with Watlow’s INFO-SENSE™ in
the
[IS;P1], [IS;P2], [IS;P3] and [IS;P4] parameters.
The four numerical values are found on the tag at-
tached to the INFOSENSE™ sensor. Contact your Wat-
low salesperson or Watlow authorized distributor for the
pricing and availability of Watlow INFOSENSE™ prod-
ucts.
Calibration Offset
Calibration offset allows a device to compensate for an
inaccurate sensor, lead resistance or other factors that af-
fect the input value. A positive offset increases the input
value, and a negative offset decreases the input value.
The input offset value can be viewed or changed with
Calibration Offset
[`CAL] (Operations parameters).