Profibus dp, Introduction to profibus dp – Watlow EZ-ZONE RMA Modul User Manual
Page 60
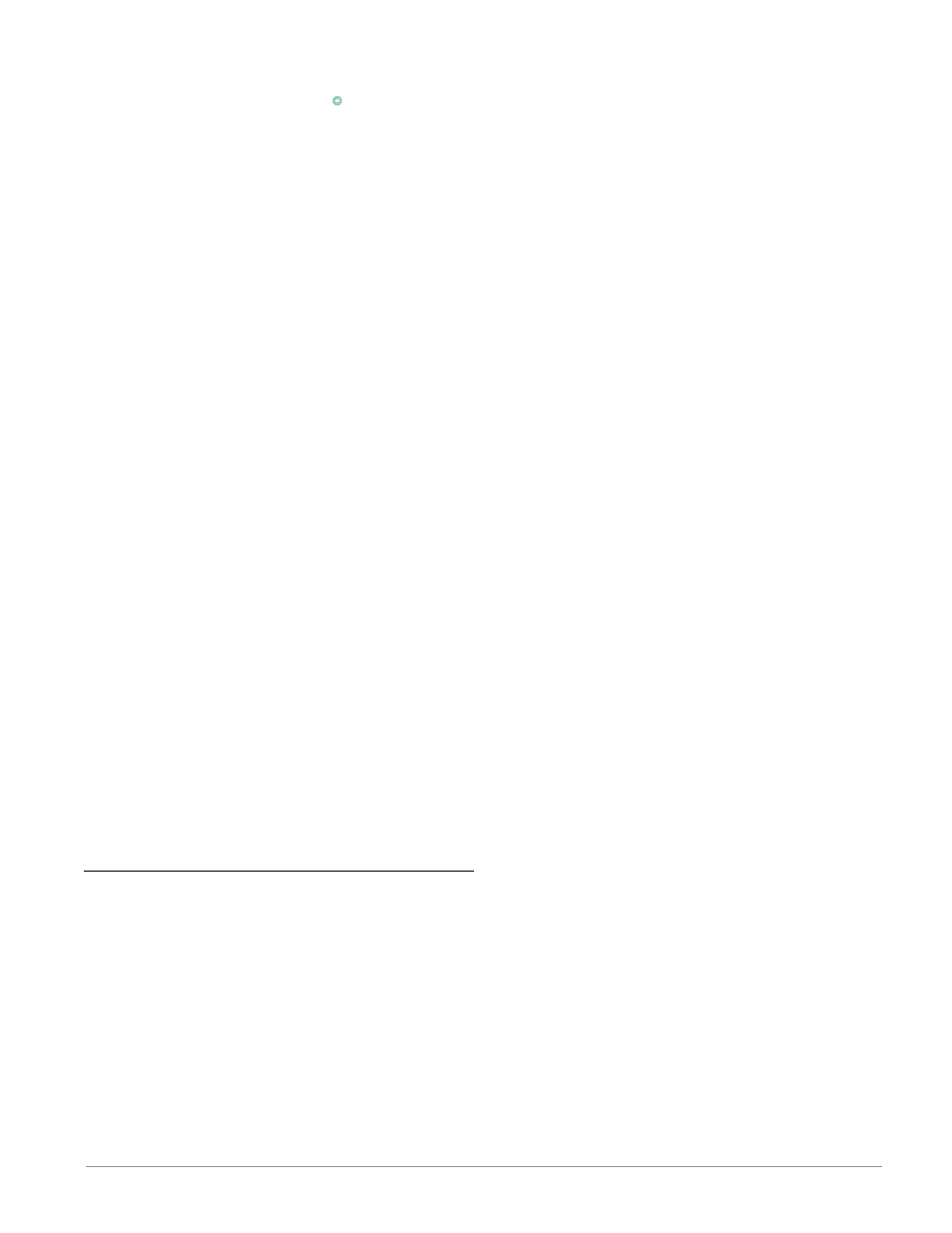
Watlow EZ-ZONE
®
RMA Module
•
57
•
Chapter 7 RMA Communications
8. Push the up or down arrow key to enable or dis-
able the quick connect feature.
9. Push the green Advance key
‰
once to change
the temperature units passed over DeviceNet
where the lower display shows [`C_F] and the
top display will show [```f] or [```C] based
on the current setting.
10. Push the up or down arrow to change to the
temperature units.
11. Push the Infinity Key ˆ three times or push
and hold for approximately 3 seconds to navi-
gate back to the Home Page.
There are three prompts delivered to the user from
the RUI when attached to the RMA that are re-
lated to DeviceNet. Two of which are defined above,
[bAud]
(network baud rate or speed) and [`Ad;d]
(network node address). There is one other which is
identified and explained below:
[FC;E]
(Quick Connect)
The Quick Connect feature is an option enabled on a
node-by-node basis. When enabled, a device transi-
tions to the on-line state concurrently with sending
the first Duplicate MACID request message. The
device is still required to execute the network State
Tranisition Diagram (STD, used to describe object
behavior), including going offline anytime a Dupli-
cate MACID response message is received.
Note
:
Although this feature allows a device to begin com-
municating on the network faster, it is at the expense
of a delay in the duplicate node detection algorithm.
It is left up to the user to guarantee that no nodes ex-
ist with the same MAC ID and that no more than one
client device is configured to access the same device
using the predefined Master/Slave connection set. Bus
errors may occur if either of these conditions exists.
This feature is enabled within a device through a non-
volatile attribute in the DeviceNet object. A device
shall have this feature disabled (attribute set to ‘0’) as
the factory default.
Once the above parameters have been changed cycle
power on the DeviceNet network for the new param-
eters to take affect.
Profibus DP
Introduction to Profibus DP
Profibus was created by the German government in
the late 80's due to industrial automation demand.
Profibus DP (Decentralized Periphery) is a serial
communications fieldbus using EIA-485 as the physi-
cal layer and is in accordance with the European
Electrical Specification EN50170.
Profibus DP uses a master slave network configu-
ration where RM modules equipped with this protocol
serve as the slave. The RMA equipped with the Pro-
fibus DP protocol supports cyclic (DP-V0) and acyclic
(DP-V1) communications. For your reference, cyclic
communications implies that a set of defined param-
eters (user configured as it relates to the RMA) are
periodically read and or written. The frequency or
period of the read/write operations is determined
(setup) via the master on the network. You can con-
figure the cyclic parameter set by installing the soft-
ware (Profibus GSD Editor for EZ-ZONE Products)
which can be found on the CD that came with the
product (Controller Support Tools) or by clicking on
the link below where it can be downloaded free of
charge, point your browser to:
Once the GSD (Generic Station Description) file is
created, simply upload it to the master device.
Acyclic communications will read and or write
data on demand and is based on the Slot Offset (as
defined in the RMA configuration) and the specific
parameter index (as can be found in the menus of the
modules User's Guide). Most of the discussion that
follows is related to acyclic communications.
As with all of the other available protocols, prior
to establishing communications between master and
the slave the gateway instance must first be enabled
[du; en]
. Once enabled, the user must define the Slot
Offsets for each enabled EZ-ZONE controller.
Use the graphic below (RUI being used as a Profi-
bus DP Gateway) in reference to the descriptions that
follow below.
[`s;of]
Slot Offsets are used exclusively with acyclic
(DP-V1) communications and define the in-
dividual EZ-ZONE controller on the network
as well as the instance of the parameter to
be read or written to. The offset defaults are
as shown in the graphic in increments of 20,
however, they can be changed based on user
needs.
As an example, when programming the master de-
vice ensure that the Slot Offset and the Profibus In-
dex (found in each product User's Guide in the vari-
ous menus) are defined. To read the first instance
of the Analog Input Value in RM 2 use the following
information when programming the Master:
Slot Offset = 20
Index = 0 (See the EZ-ZONE RMC User's Guide,
Operations Page under the Analog In-
put Menu)
Note that RM 2 and instance 1 is identified in the
Slot Offset where the parameter, in this case, Analog
Input Value 1 is identified via the Profibus Index. If
it were instance 2 of the same parameter that was
needed the Slot Offset would change to 21. Likewise,
to read the Analog Input Value instance 2 of RM 4
the following information would need to be entered
when programming the Master:
Slot Offset = 61
Index = 0