Using modbus tcp, Common industrial protocol (cip), Introduction to cip – Watlow EZ-ZONE RMA Modul User Manual
Page 55: Cip implicit assemblies, Compact implicit assembly class, Ethernet communications
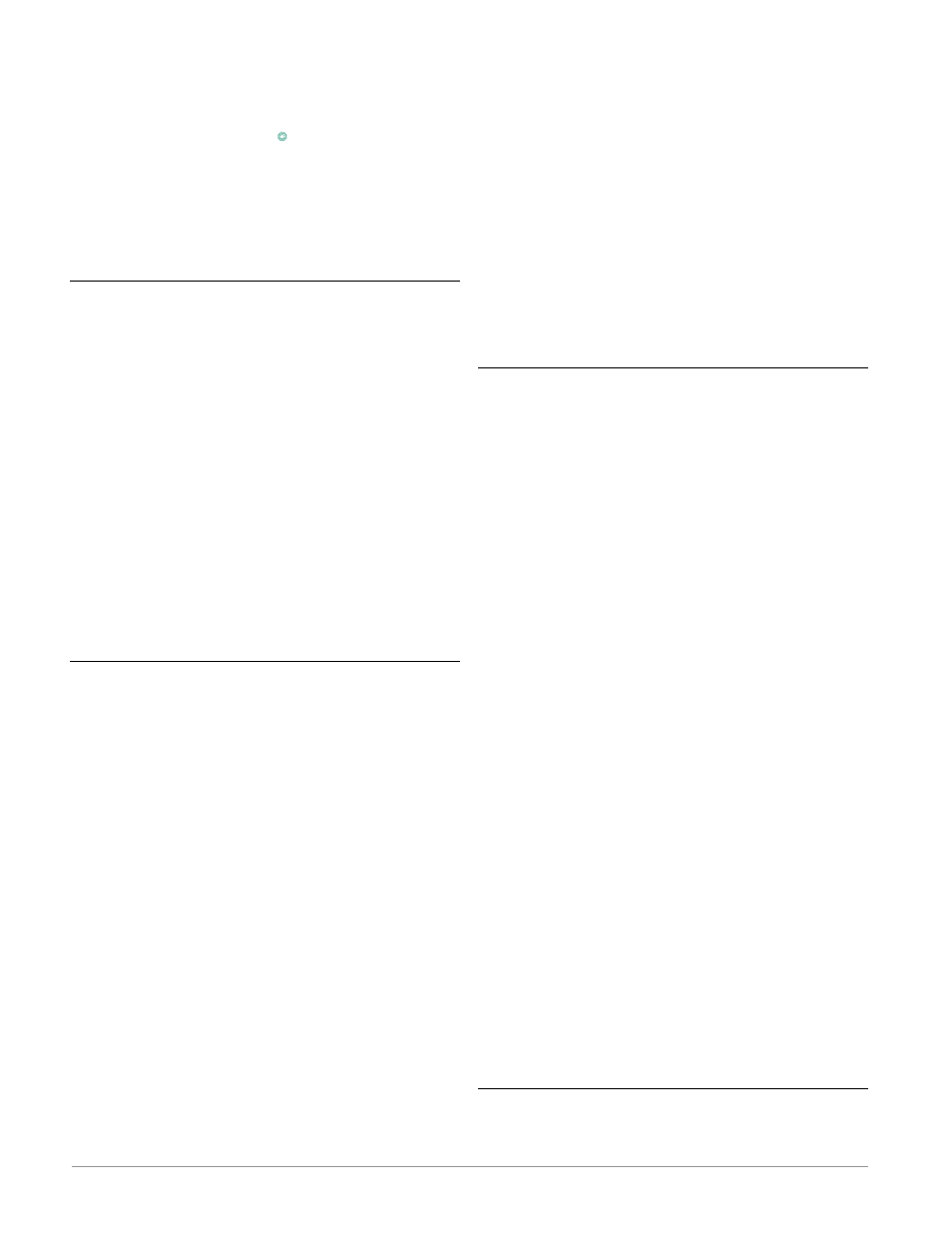
Watlow EZ-ZONE
®
RMA Module
•
52
•
Chapter 7 RMA Communications
perature units. The upper display shows [```f]
and lower display shows [`C_f]. Use the up
or down arrow key to change the temperature
units.
9. Push the Advance Key
‰
to change the Non-
volatile Save setting. The upper display shows
[`yes]
and lower display shows [`nU;s]. Use
the up or down arrow key to change the Non-
volatile Save setting.
10. Push the Infinity Key ˆ three times or push
and hold for approximately 3 seconds to navi-
gate back to the Home Page.
Ethernet Communications
Using Modbus TCP
Communications To/From a Master:
When Modbus TCP is enabled there are Modbus
related prompts (violet as shown in the following
graphic) that need to be addressed. They are:
1. Modbus TCP Enable [mb;e], turns Modbus on or
off.
2. Modbus TCP Word Order [m;hl], which allows
the user to swap the high and low order 16 bit
values of a 32 bit member.
3. Modbus TCP Offset [m;of], which defines each
of the available Modbus registers for each gate
way instance as well as the parameter. For fur-
ther information on this prompt see the section
on the previous page entitled "
".
Common Industrial Protocol (CIP)
Introduction to CIP
With the introduction of CIP a user can now collect
data, configure a device and control industrial de-
vices. CIP is an open protocol at the application layer
fully managed by the Open DeviceNet Vendors As-
sociation (ODVA,
this is an open protocol there are many independent
vendors offering a wide array of devices to the end
user. CIP provides the ability to communicate utiliz-
ing both implicit messaging (real-time I/O messag-
ing), and explicit messaging (information/configura-
tion messaging). For implicit communications using
a PLC simply configure the module (RMA) assembly
size into the I/O structure of the PLC (See:
). The assembly structure can also
be changed by the user.
Explicit communications requires the use of specific
addressing information. DeviceNet requires that
the node address be specified where EtherNet/IP re-
quires just the Class, Instance and Attribute.
• Node address or MAC ID (0 - 63, DeviceNet only)
• Class ID (1 to 255)
• Instance ID (0 to 255)
• Attribute ID (1 to 255)
EtherNet/IP and DeviceNet are both based on CIP.
EtherNet/IP (Industrial Protocol) is a network com-
munication standard capable of handling large
amounts of data at speeds of 10 Mbps or 100 Mbps,
and at up to 1,500 bytes per packet. It makes use
of standard off-the-shelf Ethernet chip sets and the
currently installed physical media (hardware con-
nections). DeviceNet was the first field bus offering
of the ODVA group and has been around for many
years. DeviceNet can communicate at 125, 250 and
500 kilobytes per second with a maximum limitation
of 64 nodes (0 to 63) on the network. The RMA mod-
ule equipped with Ethernet and DeviceNet hardware
supports implicit and unconnected explicit messages.
To enable Ethernet communications with legacy
Allen-Bradley PLCs the Ethernet card also supports
the PCCC protocol.
CIP Implicit Assemblies
Communications using CIP (EtherNet/IP and De-
viceNet) can be accomplished with any RM module
using the RMA. As was already mentioned, reading
or writing when using CIP can be accomplished via
explicit and or implicit communications. Explicit com-
munications is usually executed via a message in-
struction within the PLC but there are other ways to
do this as well outside of the focus of this document.
Implicit communications is also commonly re-
ferred to as polled communications. When using im-
plicit communications there is an I/O assembly that
would be read or written to. The default assemblies
and the assembly size is embedded into the firmware
of the specific module in use and they can be differ-
ent from module to module. Watlow refers to these
assemblies as the T to O (Target to Originator) and
the O to T (Originator to Target) assemblies where
the Target is always the EZ-ZONE controller and
the Originator is the PLC or master on the network.
There is also a common industry reference to these
assemblies that may be encountered For most RM
modules the O to T assembly is made up of 40 (32-
bit) members where the T to O consists of 41 (32-bit)
members. All assembly members are user configu-
rable with the exception of the first T to O member.
The first member of the T to O assembly is called the
Device Status, it is unique to the RMA and cannot be
changed. Bits 16 - 31 of this 32-bit word represents
the communications status of the RM modules (zones)
on the Standard Bus side of the RMA when enabled.
Once a Zone is enabled, valid communications will be
represented with the bit set to a "1", if set to "0", the
RMA is not communicating with the zone. Bit 16 rep-
resents Zone 1 where bit 31 represents Zone 16. The
40 members that follow Device Status are user con-
figurable. The Appendix of this User's Guide contains
the assemblies for each of the RM modules (See
Ap-
pendix:
CIP Implicit Assembly Structure
by product).
Compact Implicit Assembly Class
Along with the standard implicit assembly where
each module parameter (member) occupies one 32-