IAI America PCON-CFA User Manual
Page 193
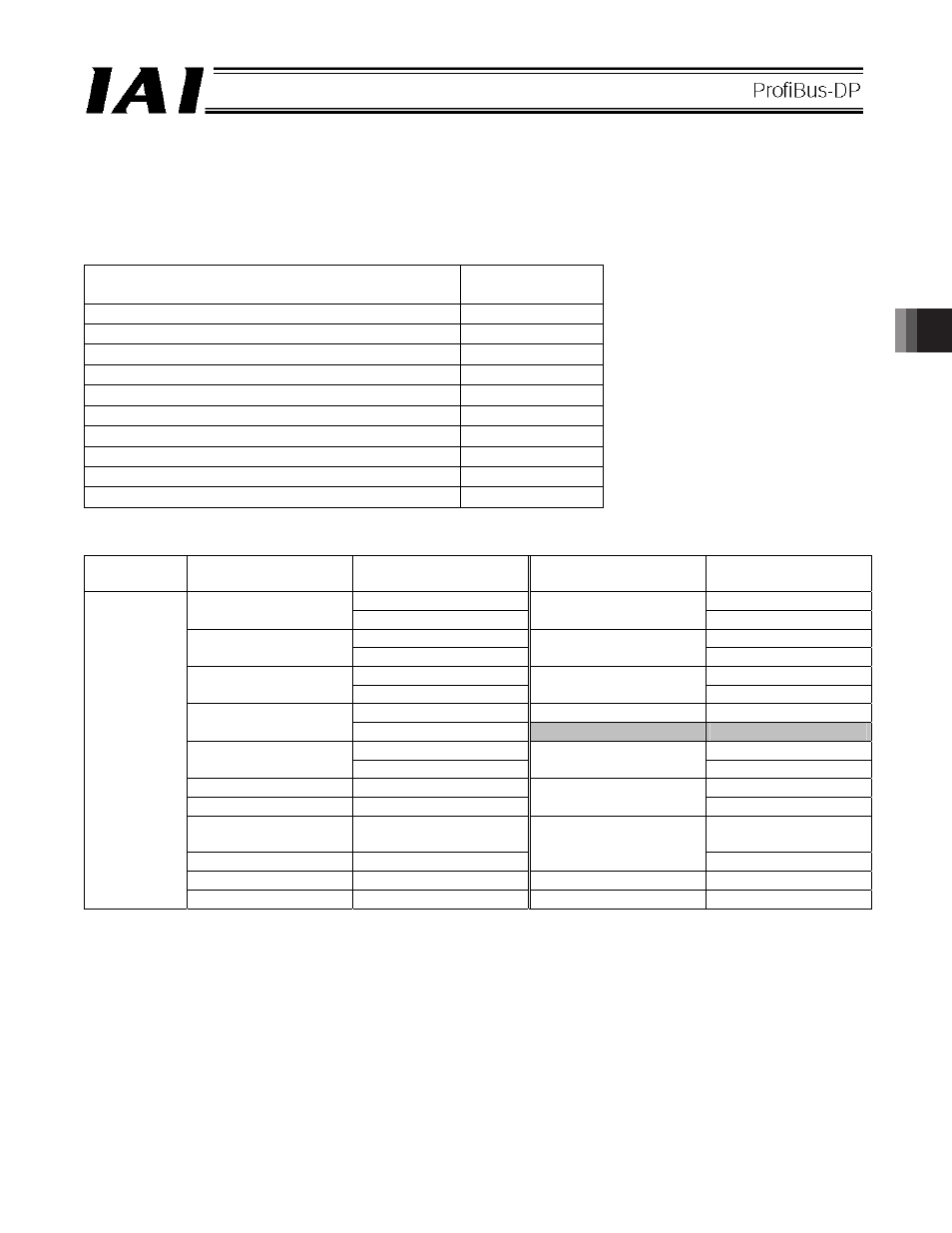
5. Flow and Commands of Basic MECHA
TROLINK Communication
187
5.4.5 Full Direct Mode (Number of Occupied Bytes: 32)
In this mode, the actuator is operated by specifying all values relating to position control (target position, speed,
etc.) directly as values from the PLC.
Set each value in an I/O address.
The key functions that are available on ROBO Cylinders controllable in this mode are shown in the table below.
ROBO Cylinder function
{: Direct control
x: Invalid
Home return operation
{
Positioning operation
{
Speed & acceleration/deceleration setting
{
Pitch feed (inching)
{
Push-motion operation
{
Speed change during movement
{
Operation at different acceleration and deceleration
{
Pause
{
Zone signal output
{
PIO pattern selection
x
(1) PLC address configuration (* n indicates the initial input/output address for each axis.)
Parameter
No. 84
SCON-CA input
register
PLC output address
SCON-CA output
register
PLC input address
n+0 n+0
Target position
n+1
Current position
n+1
n+2 n+2
Positioning band
n+3
Command current
n+3
n+4 n+4
Speed
n+5
Current speed
n+5
n+6 Alarm
code n+6
Zone boundary+
n+7
Occupied area
n+7
n+8 n+8
Zone boundary-
n+9
Force feedback data
n+9
Acceleration n+10
n+10
Deceleration n+11
Total moving count
n+11
Push-current limiting
value
n+12 n+12
Load current threshold
n+13
Total moving distance
n+13
Control signal 1
n+14
Status signal 1
n+14
3
Control signal 2
n+15
Status signal 2
n+15
(Note) The [occupied area] cannot be used for any other purpose.
Also pay attention to use of duplicate addresses.