Functions, 2 velocity monitor and analog monitor, 3 brake signal – Parker Hannifin Dynaserv G2 User Manual
Page 72
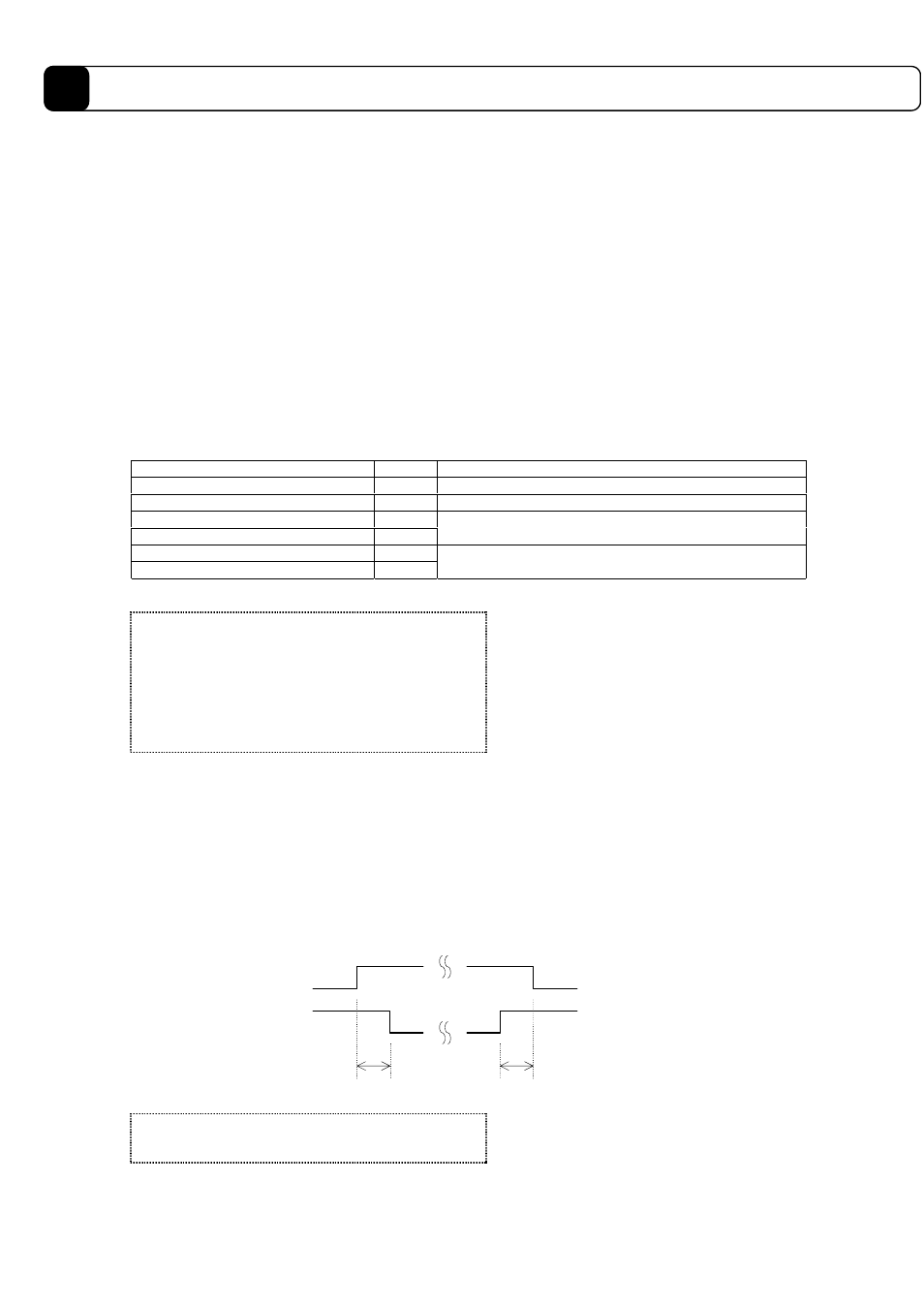
5-18
Functions
5
5.6.2
Velocity Monitor and Analog Monitor
The current velocity value of the motor is output to “VEL” of the CN3 analog monitor interface as the velocity
monitor signal.
The signal sensitivity of the velocity monitor ([V/rps] in case of a rotating DYNASERV motor and [V/mps] in
case of a linear LINEARSERV motor) can be obtained by multiplying the #69 Velocity monitor gain parameter
setting by the #356 Digital velocity sensitivity monitor value. For example, if the setting of #69 is 6.55V/8192
digits and the value of #356 is 4800 [digit/rps] in a rotating motor, the signal sensitivity of the velocity monitor is
3.84 [V/rps]. The velocity monitor signal is output in the range of
± 6.55V.
Moreover, it is possible to output only the AC element of the current velocity value of the motor via the setting
of the #75 Velocity monitor selection parameter.
One of the data items below is output to “AMON” of the CN3 analog monitor interface as an analog monitor
signal.
The content of the analog monitor can be selected by the #70 Analog monitor selection parameter. Depending
on the selected content, the signal sensitivity is adjusted using the corresponding monitor gains #71 to 74. The
analog monitor signals are output in the range of
± 6.55V.
Analog monitor selection
Unit
Monitor gain
Position deviation
Pulse
#71 Positioning error monitoring gain (Analog monitor)
Test operation response
Pulse
#72 Test operation monitoring gain (Analog monitor)
Position command value
Pulse
Position current value
Pulse
#73 Position monitoring gain (Analog monitor)
Position command differential value
pps
Position current differential value
pps
#74 Position differential value monitor gain (Analog
monitor)
[Related parameters]
#69
Velocity monitoring gain
#70
Analog monitor selection
#71
Positioning error monitoring gain (Analog monitor)
#72
Test operation monitoring gain (Analog monitor)
#73
Position monitoring gain (Analog monitor)
#74
Position difference value monitor gain (Analog
monitor) #74
#75
Velocity monitor selection
5.6.3 Brake Signal
BRK+ and BRK- are output to the TB2 external sensor interface as brake signal outputs that operate linked to
the Servo ON status. The brake signal is a relay contact output. The contact opens when the brake should be
applied such as when the power is disconnected or the driver is in Servo OFF status, and the contact short
circuits when the brake should be released.
The Servo ON status and the brake signal operate according to the timing diagram shown below via the #89
Brake turn OFF delay time upon Servo ON and #90 Advanced brake turn ON before Servo OFF
parameters.
#90
#89
Servo ON status
ON
OFF
Brake signal
Open-circuit
Short-circuit
[Related parameters]
#89
Brake turn OFF delay time upon Servo ON
#90
Advanced Brake turn ON before Servo OFF