Functions, 2 position control part, 3 feed forward – Parker Hannifin Dynaserv G2 User Manual
Page 66
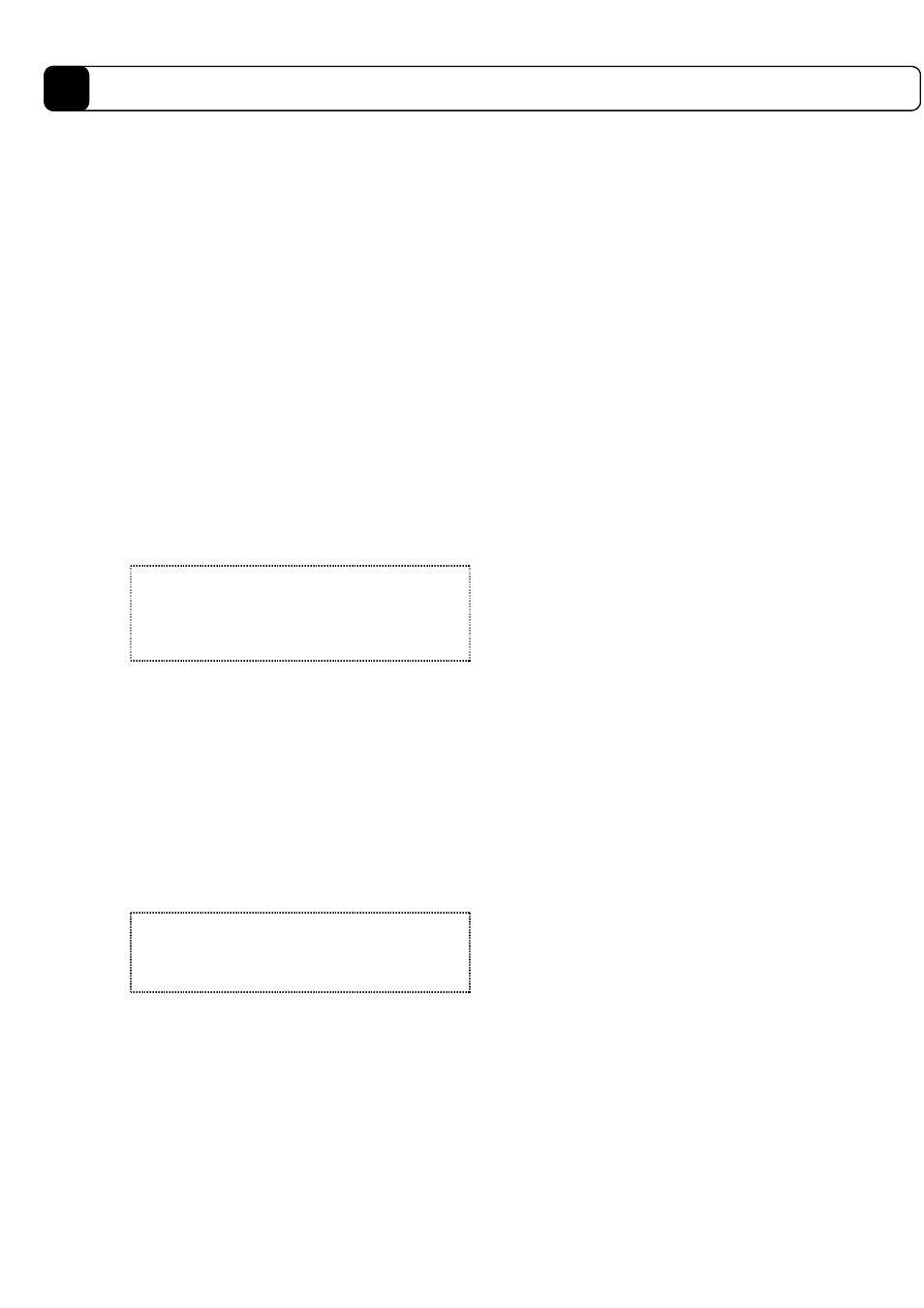
5-12
Functions
5
5.4.2
Position Control Part
For the position control bandwidth, either the value set with the #50 Position control bandwidth 1 parameter or
the #48 Position control bandwidth 2 parameter is selected, according to the status of the controller interface
input signal IN_FN. The selected value is displayed in the #375 Position control bandwidth monitor.
The position control part calculates the proportional control gain, integral control gain, and differential feedback
gain, according to the position control bandwidth value.
The position integral limiter set by the #53 Position integral limiting value parameter is effective in suppressing
integrator windup due to motor torque and thrust saturation. Decrease the value in order to suppress windup
further. On the other hand, if you set the value too small, the motor torque and thrust are limited; set a value as
large as possible in the range where windup does not occur.
The integral operation of the position control part can also be set either to be active (allow) or inactive (prohibit).
If you clamp the motor with an external device when the motor is stopped, the integral operation should be
prohibited after clamping in order to prevent overloading the controller. Refer to Chapter 6 “Controller
Interface” and Chaper 7 “RS232C Interface” for details of the operation.
The position current value filter outputs the result obtained by filtering the position current value to the #384
Motor linear coordinate current value after filtering monitor. The filter bandwidth is set with the #59
Position current value filter frequency parameter. The position control part outputs a value before or after
being filtered to the #321 Pulse position current value monitor, according to the setting status of the #203
Using position current value filter parameter. It also calculates the value of the #322 Pulse position
deviation monitor, using the current value before or after being filtered, according to the setting status of the
#203 parameter.
[Related parameters]
#50
Position control bandwidth 1
#48
Position control bandwidth 2
#53
Position integral limiting value
#59
Position deviation filter frequency
#203
Using position current value filter
5.4.3
Feed Forward
Three types of feed forward functions are available: position feed forward, velocity feed forward, and
acceleration feed forward. Feed forward function is effective for quick positioning.
The position feed forward can be set by percentage in the #54 Position feed forward percentage parameter.
The position feed forward makes the position deviation at equal velocity move smaller and helps to achieve a
smooth settling at acceleration/deceleration.
The velocity feed forward can be set by percentage in the #55 Velocity feed forward percentage parameter.
The acceleration feed forward calculates the acceleration feed forward gain from the #155 Load inertia/load
mass parameter values, which are measured and set by the auto-tuning operation or set directly by numerical
values, based on the #56 Acceleration feed forward gain parameter. #56 parameter is given as a percentage.
[Related parameters]
#54
Position feed forward percentage
#55
Velocity feed forward percentage
#56
Acceleration feed forward percentage
#155
Load inertia/load mass